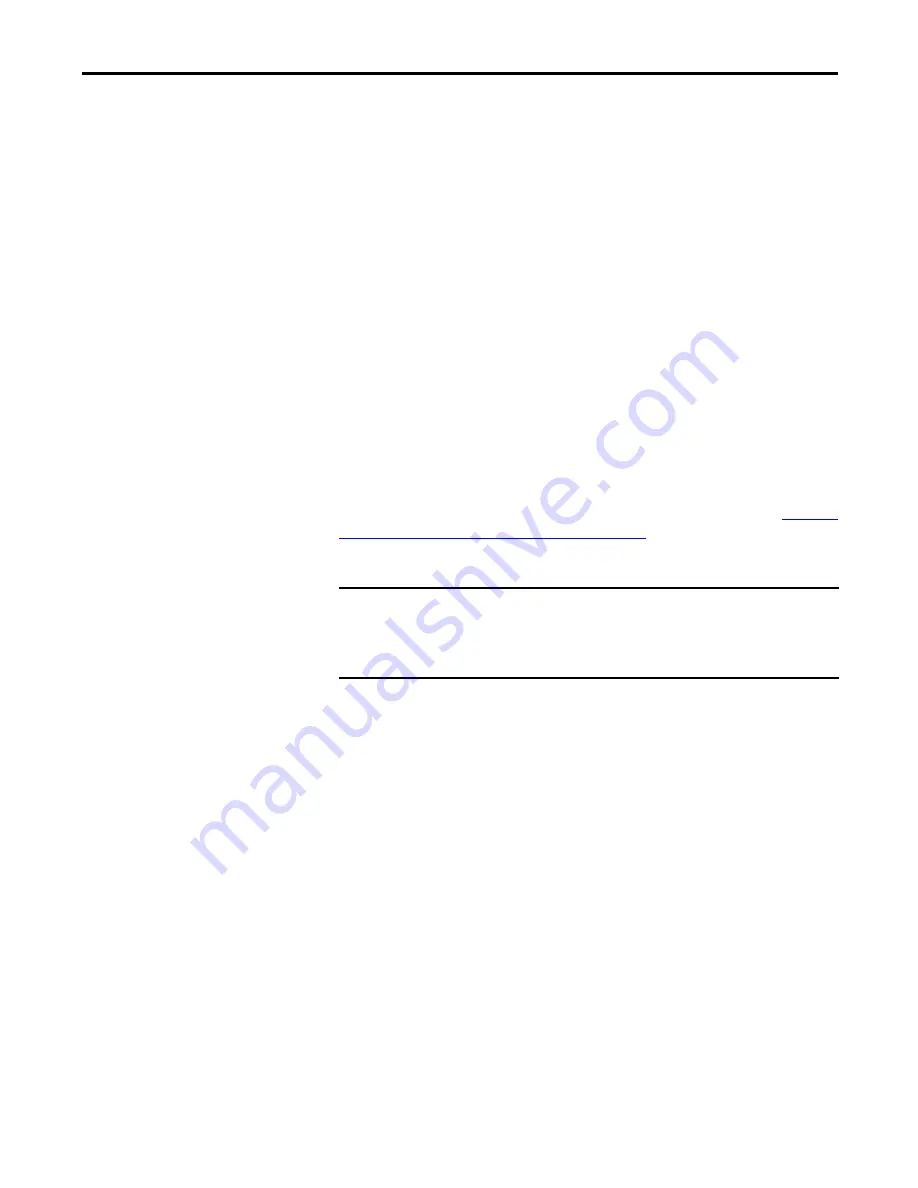
Rockwell Automation Publication 7000L-UM301F-EN-P - March 2020
83
Drive Installation
Chapter 2
Power and Control Wiring
Drive line-ups (i.e. Drive and Input Starter) which are delivered in two or more
sections, for ease of handling, will require that the power and control wiring be
re-connected. After the sections are brought together, the power and control
wiring is to be reconnected as per the schematic drawings provided.
Control Cables
Control cable entry/exit should be located near the terminal block “TBC” – the
customer’s connections are to be routed along the empty side of the TBC
terminals. These terminals are sized to accept a maximum AWG #14 wire gauge.
The low voltage signals (includes 4-20mA) are to be connected using twisted
shielded cable, with a minimum AWG #18 wire gauge. (Based on using a W4
terminal block for customer connections, comparable wire sizes would be
0.5...4 mm
2
as equivalent to #22-#10 AWG.)
Of special concern is the encoder signal. Two encoder inputs are provided to
accommodate a quadrature encoder (senses motor direction). The encoder power
supply is isolated and pr15V and a ground reference. Many encoder
outputs have an open collector output, in which case a pull-up resistor must be
added to ensure that proper signals are fed to the system logic. (Refer to
an Encoder Required? on page 416 (Appendix A)
supplied.)
Encoder Installation Guidelines
The most frequent problems encountered when transmitting an encoder’s
signal(s) to the drive are signal distortion and electrical noise. Either of these
problems can result in a gain or loss of encoder data counts (quadrature encoders)
or corrupt positional data (absolute encoders). Many of these problems can be
avoided by applying good installation and wiring practices. This section is a
general guideline and recommended practices for field installed equipment. It
applies to either encoder board and both quadrature and absolute encoders.
Protection from Radiated and Conducted Noise
Reasonable care should be taken when connecting and routing power and signal
wiring on a machine or system. Radiated noise from nearby relays, solenoids,
transformers, non linear loads (such as motor drives) etc. can couple onto signal
wires producing undesired pulses. In fact the encoder itself may induce noise into
signal lines run adjacent to it.
IMPORTANT
Low voltage signals are to be connected using twisted shielded cable with the
shield connected at the signal source end only. The shield at the other end is to
be wrapped with electrical tape and isolated. Connections are to be made as
shown on the drawings provided.
Содержание Allen-Bradley PowerFlex 7000
Страница 32: ...32 Rockwell Automation Publication 7000L UM301F EN P March 2020 Chapter 1 Overview of Drive Notes ...
Страница 90: ...90 Rockwell Automation Publication 7000L UM301F EN P March 2020 Chapter 2 Drive Installation Notes ...
Страница 174: ...174 Rockwell Automation Publication 7000L UM301F EN P March 2020 Chapter 4 Commissioning NOTES ...
Страница 264: ...264 Rockwell Automation Publication 7000L UM301F EN P March 2020 Chapter 4 Commissioning Notes ...
Страница 412: ...412 Rockwell Automation Publication 7000L UM301F EN P March 2020 Chapter 5 Component Definition and Maintenance ...
Страница 420: ...420 Rockwell Automation Publication 7000L UM301F EN P March 2020 Appendix A Catalog Number Explanation Notes ...
Страница 428: ...428 Rockwell Automation Publication 7000L UM301F EN P March 2020 Appendix C Meggering Notes ...
Страница 432: ...432 Rockwell Automation Publication 7000L UM301F EN P March 2020 Appendix D Preventative Maintenance Schedule Notes ...
Страница 433: ......