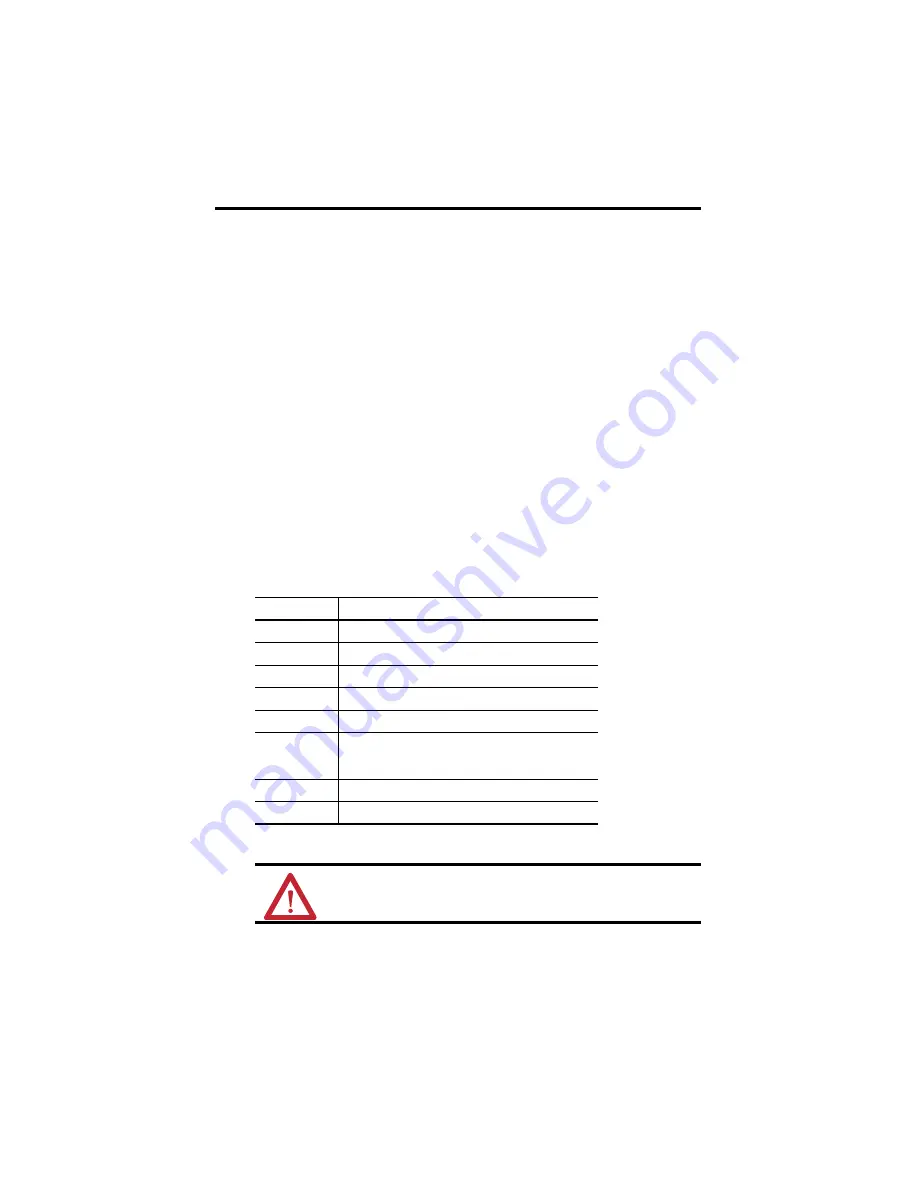
36
LDAT-Series Integrated Linear Thrusters
Rockwell Automation Publication LDAT-IN001B-EN-P - March 2020
Fine Tune
Use the Gains tab to fine tune your linear thruster. The following bullets show you how to get
the best results.
•
For precise positioning applications, add position integral gain and increase the position
proportional gain as necessary.
•
For stiffer and more precise tracking of motion profiles, increase the velocity gain.
•
For stable operation increase the velocity gain until you hear the axis oscillate, and then
reduce the velocity gain by one half.
•
For applications with very high acceleration, > 30 m/s/s (1.2 in/s/s), add acceleration
feed forward.
•
For linear thrusters with long travel, > 500 mm (20 in.) or with large mass attached to
the slider, you may notice the axis is vibrating or resonating after AutoTune. If it does, use
the Output screen to add a low pass filter or a notch filter to remove the resonance.
Set up Homing
Enter these parameters to set up homing for the linear thruster.
Parameter
Entry/Selection
Mode
Active
Position
0, typical
Offset
10 mm
(1)
(1)
The 10mm offset sets the home position to an axis location clear of the spring stops.
Sequence
Torque Level-Marker
Direction
Reverse Bi-directional
Torque Level
20%, min
Greater if the system friction, force, or weight exceeds 30% of the
Continuous Force Rating at any point in the range of motion
Speed
5 mm/s
Return Speed
10 mm/s
ATTENTION:
Avoid excessive force while homing the linear thruster. Do not exceed
100 mm/s (4.0 in/s) during a home routine. Speeds greater than 100 mm/s (4.0 in/s)
may damage the linear thruster when the slider reaches the end of travel.