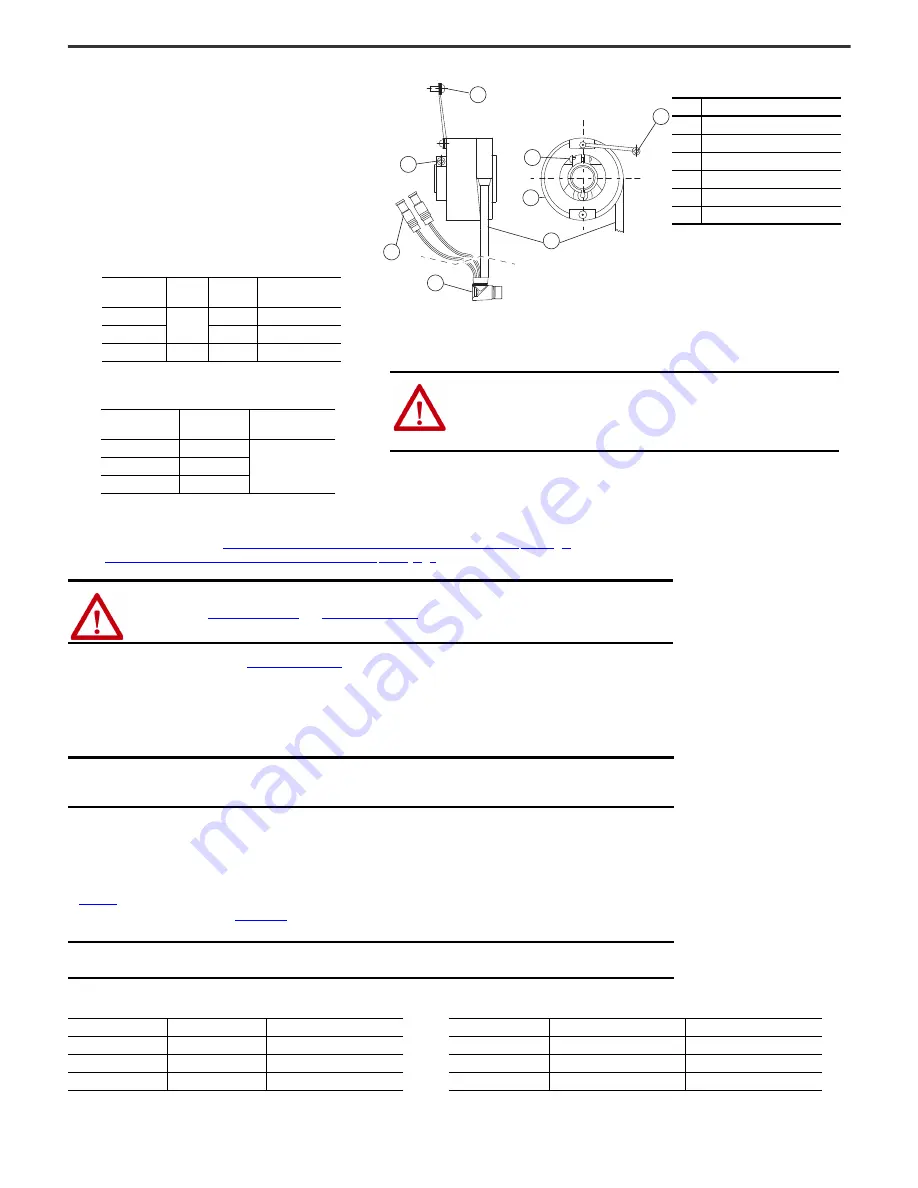
Rockwell Automation Publication MM-IN001B-EN-P - February 2022
57
Kinetix MMA Asynchronous Main Motors Installation Instructions
3.
Remove the encoder.
a. For encoders S1, S3, S4, M1, M3, and M4
- Loosen shaft-clamp screw
- Remove the four mounting hardware screws
b. For encoder L2
- Loosen shaft-clamp screw
- Remove single fixed-arm screw
4.
Remove encoder from motor shaft.
5.
Disconnect the thermostat connectors from the motor
feedback cable.
6.
Install the new encoder onto the motor shaft and insert
the mounting screws.
Torque per the table that follows:
7.
Tighten the shaft-clamp screw.
Torque per the table that follows:
8.
Use the existing motor cable clamps to attach the encoder harness to the screws on the motor plate.
9.
Reconnect the thermostat connectors to the motor feedback cable.
10. Follow the instructions in
Instructions to Reposition or Replace the Radial Blower Assembly
to install your radial blower or
Install the IC17 Clean-air Kit (Includes: Replace Axial Blower)
to install your axial blower and the feedback connector.
Encoders are preprogrammed. See the
for the drive user manuals that include information on how to reconnect the encoder to your system.
Safety Encoders
For motors that have an S2 or M2 (SIL 2/PLd rated) safety-rated encoder, the customer is not allowed to replace the encoder.
Shaft Seals
Shaft seals are not provided as a replacement part from Rockwell Automation. The customer must supply their own Kinetix MMA main motor shaft seal using the information
in
. Shaft seals are made of nitrile and kits should include a lubricant to reduce wear. Consistent and regular inspection is recommended. See Shaft Seal Kits
Installation Instructions, publication
for general guidance on replacing a shaft seal.
Encoder
Cat. No.
Screw
Type
Screw
Quantity
Torque
N•m (lb•in)
S1, M1
M3
4
1.2 (10.62)
S3, S4, M3, M4
4
1 (8.85)
L2
M4
1
1.5 (13.28)
Encoder Cat. No.
Screw Type
Torque
N•m (lb•in)
S1, M1
TX10
1.1 (9.74)
S3, S4, M3, M4
TX8
L2
TX10
ATTENTION:
During reassembly, verify that the ground wire for the motor feedback connector is properly
and
for additional information, the ground spade
connector is located inside the blower housing near the feedback connector.
IMPORTANT
Only Rockwell Automation trained personnel, Rockwell Automation approved motor repair center, or
certified field service engineer (FSE) shall be allowed to perform the field replacement service on Kinetix
MMA main motors with functional safety-rated encoder.
IMPORTANT
Shaft seals are subject to wear and require periodic inspection and replacement. Replacement is
recommended every 3 months, not to exceed 12 months, depending on use.
Table 58 - Shaft Seal Dimensions by Catalog Number
Motor Cat. No.
Dimensions (mm)
Type
Motor Cat. No.
Dimensions (mm)
Type
MMA-B080
xxx
30x52x7
Oil seal type A 30x52x7
MMA-B160
xxx
60x85x8
Oil seal type A 60x85x8
MMA-B100
xxx
45x62x8
Oil seal type A 45x62x8
MMA-B180
xxx
70x85x8
Oil seal type A 70x85x8
MMA-B132
xxx
45x72x8
Oil seal type A 45x72x8
MMA-B225
xxx
90x110x12
Oil seal type A 90x110x12
3
4
2
1
2
3
5
6
Encoder L2
Encoder Diagram Call-out Descriptions
#
Description
1
Encoder
2
Single fixed-arm screw
3
Shaft clamp
4
Encoder harness
5
Thermostat connector
6
Feedback connector
ATTENTION:
The encoder shaft clamp can break if overtightened. A broken
shaft clamp could cause unexpected motor shaft rotation and corresponding
machine motion, due to loss of encoder feedback. Failure to observe safety
procedures could result in personal injury or damage to the motor and other
equipment.