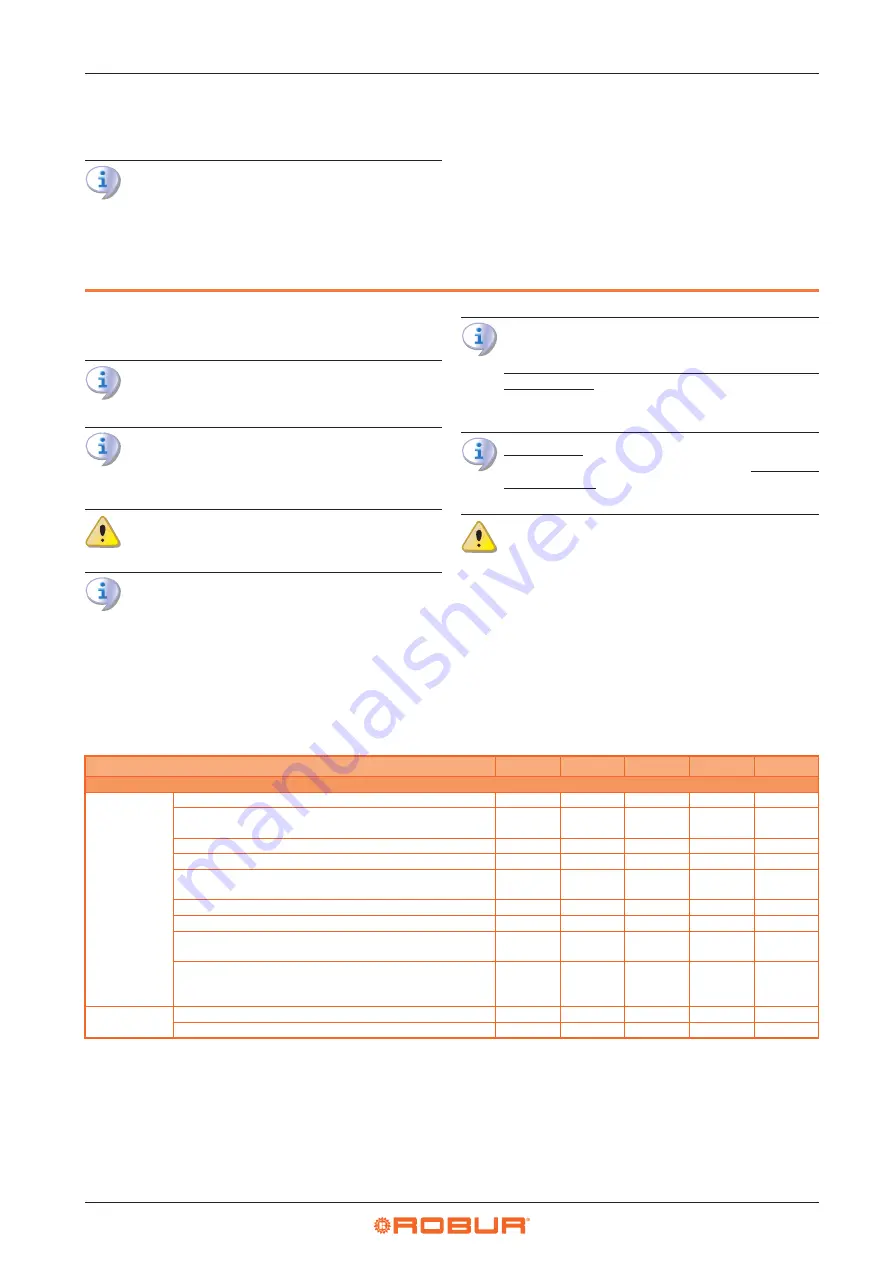
Maintenance
32
7
If the appliance is connected to the DDC or to the CCP/
CCI control, refer to the relevant manual to modify
settings.
Do not modify complex settings
Specific technical and system knowledge is required for
complex settings. Contact a TAC.
6.4
EFFICIENCY
For increased appliance efficiency:
▶
Keep the finned coil clean.
▶
Set water temperature to the actual system requirement.
▶
Reduce repeated switch-ons to the minimum (low loads).
▶
Program appliance activation for actual periods of use.
▶
Keep water and air filters on plumbing and ventilation sys-
tems clean.
7
MAINTENANCE
7.1
WARNINGS
Correct maintenance prevents problems, assures effi-
ciency and keeps running costs low.
Maintenance operations described herein may exclu-
sively be performed by the TAC or skilled maintenance
technician.
Any operation on internal components may exclusively
be performed by the TAC.
Before performing any operation, switch off the appli-
ance by means of the control device and wait for the end
of the shutdown cycle, then disconnect power and gas
supply, by acting on the electrical disconnector and gas
valve.
The efficiency checks and every other "check and mainte-
nance operation" (see Tables 7.1
must be performed with a frequency according to cur-
rent regulations or, if more restrictive, according to the
provisions set forth by the manufacturer, installer or TAC.
Responsibility for efficiency checks, to be carried out for
the aims of restricting energy consumption, lies with the
system manager.
Environmental or operational heavy conditions
In environmental or operational conditions particularly
heavy (for example: heavy-duty use of the appliance,
salty environment, etc.), maintenance and cleaning op-
erations must be more frequent.
7.2
PRE-EMPTIVE MAINTENANCE
For pre-emptive maintenance, comply with the recommendations in Table 7.1
Table 7.1
GAHP A
GAHP GS/WS
AY00-120
GA ACF
GAHP-AR
Guidelines for the preventive maintenance operations
Check of the unit
visually check of the general condition of the unit and of its finned coil
√ (1)
-
-
√ (1)
√ (1)
check the correct operation of the device used for monitoring the water
flow
√
√
√
√
√
check the % value of CO
2
√
√
√
-
-
check gas pressure to the burners
-
-
-
√
√
check that the condensate discharge is clean (If necessary, frequency of
the maintenace operation must be increased)
√
√
√
-
-
replace the belts after 6 years or 12000 hours of operation
√
√
-
√
√
check/restore the pressure of the primary hydronic circuit
-
-
√
-
-
check/restore the air pressure inside of the expansion vessel of the
primary hydronic circuit
-
-
√
-
-
replace the oil pump motor condenser every 3 years or every 10000
operating hours or whenever the condenser capacity is less than 95% of
the nominal value
√
√
-
√
√
Check for every
DDC or CCI
check that the plant is able to achieve the setpoint temperature
√
√
√
√
√
download the event history
√
√
√
√
√
(1) It is suggested to clean the finned coil once every 4 years (optimal frequency of the cleaning operation is in any case strongly affected by the installation site). Avoid excessively aggressive
cleaning of the finned coil (e.g. high-pressure washer).
7.3
SCHEDULED ROUTINE MAINTENANCE
For scheduled routine maintenance, perform the operations in Table 7.2
p. 33, at least once every 2 years.
Содержание GAHP A indoor
Страница 39: ......