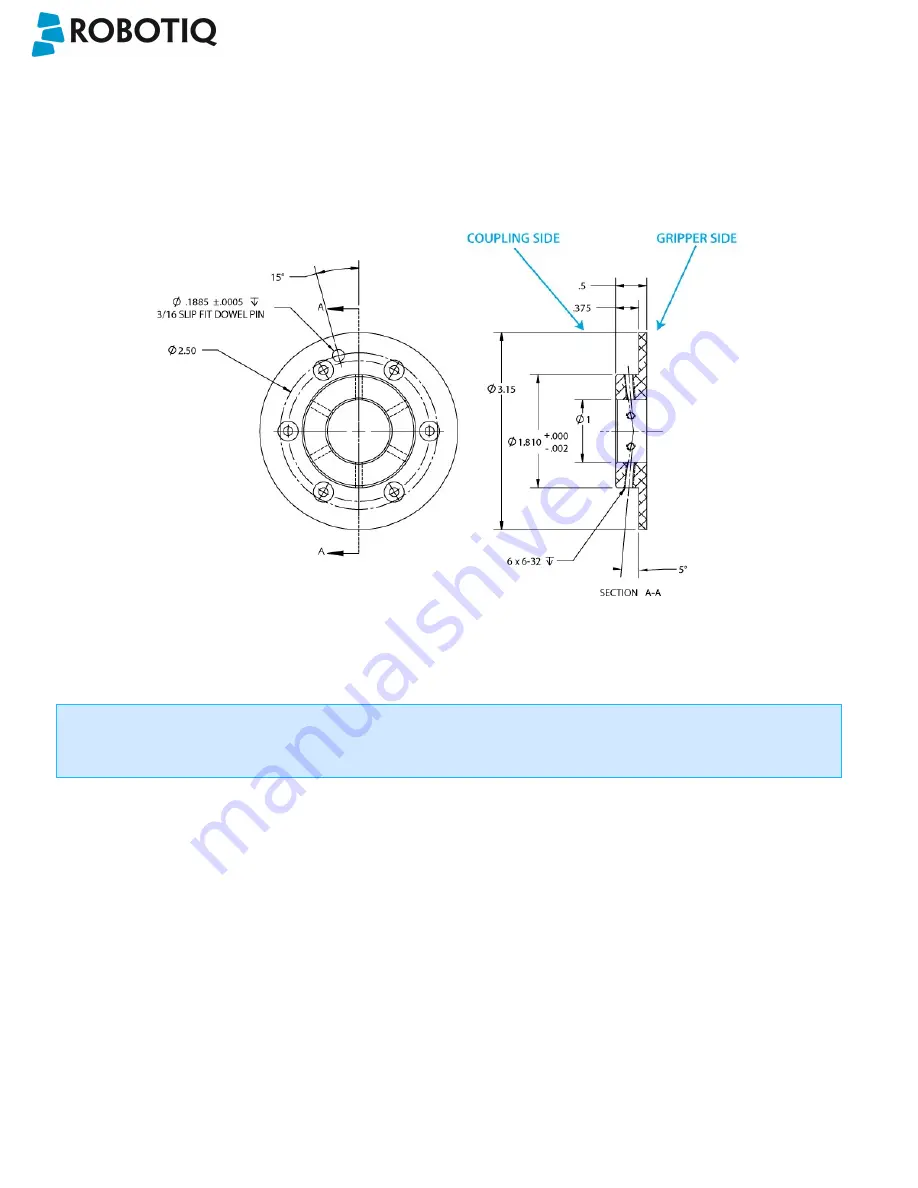
3-Finger Adaptive Robot Gripper Instruction Manual
6.6.3 Dimensions for custom coupling
Figure 6.6.3.1 shown below describes the standard wrist present on all 3-Finger Adaptive Robot Grippers. Your custom coupling must be designed for
fixation on the provided wrist.
Figure 6.6.3.1 : 3-Finger Adaptive Robot Gripper dimensions for custom coupling.
Info
The Gripper must be secured with all six (6) of the # 6-32 UNC screws. Use the 3/16 Dowel pin for indexing, pin must be press fit in the custom
coupling, it is slip fit on the Gripper Universal Wrist side.
©Robotiq inc. 2008-2018
82