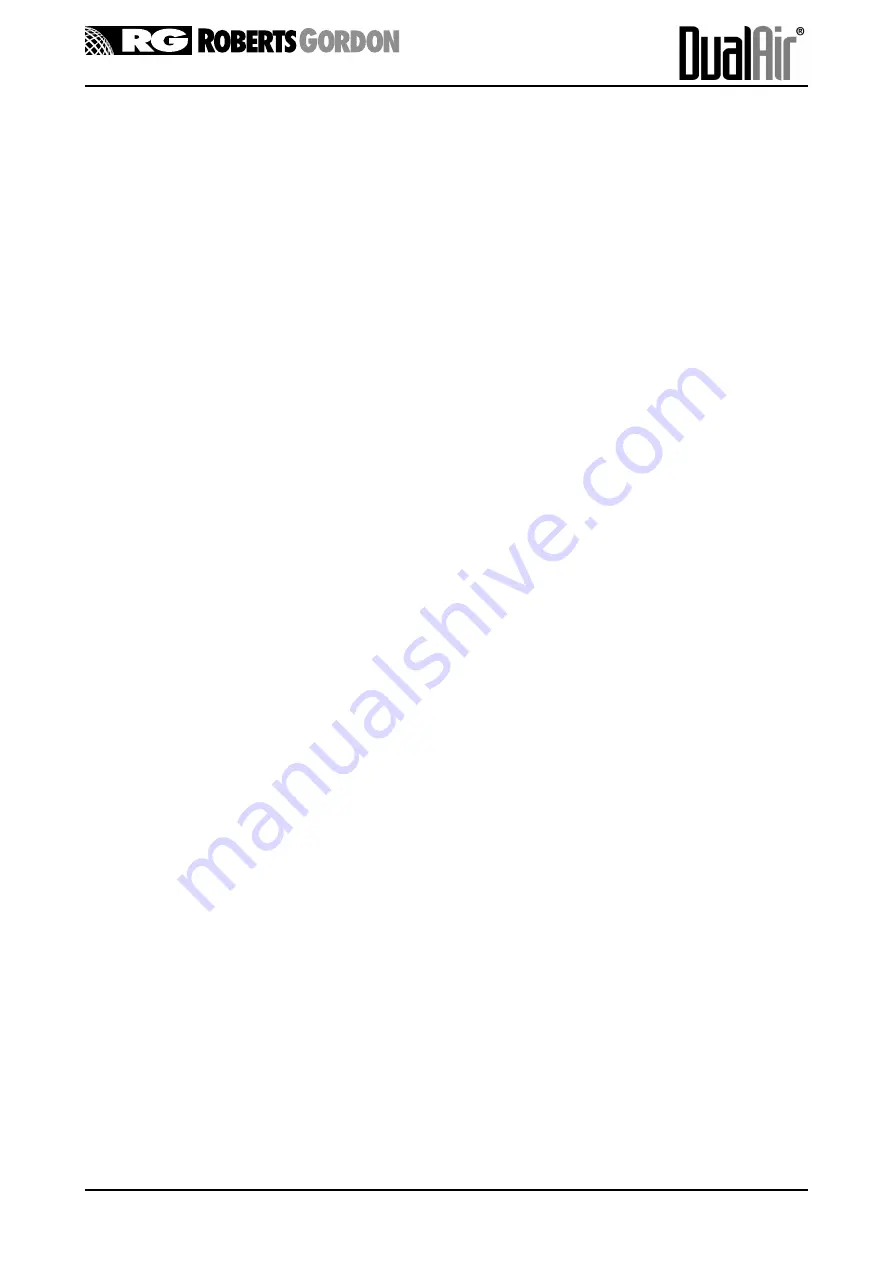
Page 29
4.6
Burner Commissioning Tests
With the main burner operating for at least 15 minutes carry out a spillage test on the draught diverter
in accordance with BS 5440 Part 1 ensuring that all doors and windows in the area are closed and
that any extract fans are turned ON.
One method is to hold a lighted taper or smoke match just inside of the draught diverter and observe
that the smoke or flame is not drawn away from the heater.
Should it be indicated that the products of combustion are continuously entering the building from the
draught diverter then corrective action MUST be taken before leaving the heater to operate normally.
4.7
Combustion Testing
Although there is no adjustment available to alter the combustion performance of the heater, other
than burner pressure, it is advisable to take combustion readings to determine the proper operation
of the heater.
To do this the flue gas is sampled at the test point on the flue, within 1 metre of the heater and tested
for contents of CO
2
(carbon dioxide), CO (carbon monoxide) and temperature rise. The values of CO
2
should be between 5.5% and 6.5% . CO should be no more than 0.0015% ( 15 PPM) and the
temperature rise of the flue gasses above ambient should be approximately 160°C to 180°C when
running at full rate.
Combustion testing must be carried out with all covers etc. fully fitted as designed.
4.8
Turning Off the Heater - All Heater Types
To turn off the heater operate the external controls to the off position and the main burner will stop.
Allow the fans to run on until they are stopped automatically by the fan thermostat. The heater will
then be at rest until the controls call for heat once more. For long term closing down for summer etc.
then when the fans have stopped automatically, turn off the gas and electrical supplies at the isolators.
4.9
External Controls
Operate the External Controls as installed which may include time switch, room thermostat and manual
switch to ensure that they function correctly. Set the time switch (if fitted) and room thermostat to the
users requirements.
See Sections 2 and 9.
Содержание Dualair DA260G Series
Страница 2: ...Details of condense drain for cooling coil ...
Страница 8: ...Page 6 Fig 2 1 DualAir 300 Module Dimensions Section 2 Technical Data FRONT VIEW REAR VIEW SIDE VIEW ...
Страница 9: ...Page 7 Fig 2 2 DualAir 380 Module Dimensions FRONT VIEW REAR VIEW SIDE VIEW ...
Страница 33: ...Page 31 Fig 5 1 Wiring for DualAir Units On Off Burner 230v Controls Section 5 Wiring Diagrams ...
Страница 34: ...Page 32 Fig 5 2 Wiring for DualAir Units On Off Burner 24v Controls ...
Страница 35: ...Page 33 Fig 5 3 Wiring for DualAir Units Hi Low Burner 230v Controls ...
Страница 36: ...Page 34 Fig 5 4 Wiring for DualAir Units Hi Low Burner 24v Controls ...
Страница 37: ...Page 35 Fig 5 6 Wiring for DualAir Units BMS Burner Modulation 230v Controls ...
Страница 38: ...Page 36 Fig 5 7 Wiring for DualAir Units BMS Burner Modulation 24v Controls ...
Страница 39: ...Page 37 Fig 5 7 Wiring for DualAir Units Full Burner Modulation 230v Controls ...
Страница 40: ...Page 38 Fig 5 8 Wiring for DualAir Units Full Burner Modulation 24v Controls ...
Страница 41: ......
Страница 42: ......
Страница 43: ......
Страница 44: ......
Страница 45: ......
Страница 46: ......
Страница 47: ......
Страница 48: ......
Страница 49: ......
Страница 50: ......