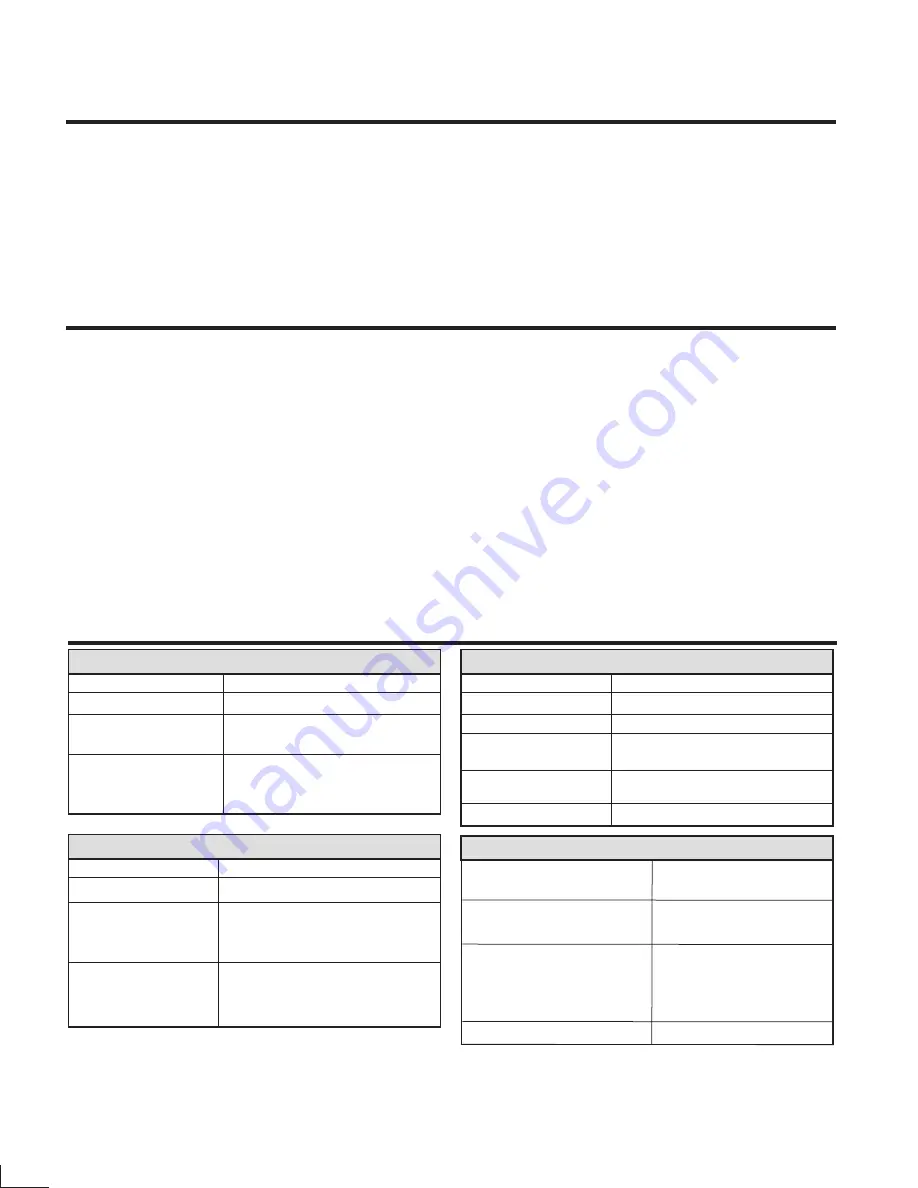
MAINTENANCE AND FOLLOW-UP DETAILS
11
MAINTENANCE SAFETY PRECAUTIONS
BEFORE PERFORMING MAINTENANCE
While performing maintenance do not wear loose clothing. Immediately
report any hazardous conditions--sharp edges, pinch (or nip) points or other
conditions that may result when several manufacturers supply machinery
which may create operating hazards.
When using mechanical aids such as hoists, cables, or cranes exercise
extreme caution to prevent damage to conveyors or other integrated machin-
ery which may create a working hazard when maintenance is completed and
units are in operation.
Clean up any spilled lubricants or other materials used in the main-
tenance process or those which may be deposited during unit operation.
Eliminating poor housekeeping practices increases unit efficiency while creat-
ing safer personnel working conditions.
After maintenance, conduct visual inspection to ensure that all safety
devices and guards have been replaced. Confirm that all units are clear
of tools, debris or other items. Before starting conveyor, check condition of
conveyor warning labels (see “WARNING LABELS” at front of handbook). If
labels have been destroyed or are not clearly legible, call 870.483.7631 to
receive replacement labels. Placement of warning labels is critical to avoid
unauthorized unit operation which may result in hazardous working condi-
tions for all related personnel coming in contact with conveyor.
Warn personnel that conveyor is being prepared for start-up and to stay
clear of unit. Do not start conveyor until all personnel are clear. When main-
tenance is completed, only authorized personnel shall be permitted to start
conveyor following maintenance or other emergency shut-off.
One of the most important guidelines for maximizing conveyor operation
and personnel safety is to implement a regular maintenance schedule and
train personnel on the appropriate needs of the specific unit.
Only trained personnel shall perform maintenance functions.
Before maintenance operations are performed, conveyor must
be shut “OFF” and disconnects locked in the “OFF” position to prevent
unit from unauthorized start-up during maintenance. All personnel
should be informed of the safety procedures associated with unit main-
tenance and performance.
Do not perform any work on conveyors or conveyor system while in
operation unless it is impossible to otherwise conduct adjustment, lubrication
or other maintenance function.
Only experienced, trained personnel possessing advanced hazards-train-
ing should attempt such critical operations.
MAINTENANCE PERIODIC MAINTENANCE SCHEDULE AND LUBRICATION
**NOTE: Temperatures listed indicate the nominal operational temperature for the specific lubricant listed. This does not imply that the bearing housing, seals or any other conveyor unit
component is rated to operate in this specific temperature range or environment. 250°F is the maximum operating temperature for standard bearing lubricants and bearing components.
Although various lubricants may enhance bearing operation, special-order bearings may be required to achieve optimal bearing performance. For additional information, consult factory.
WEEKLY RECOMMENDED MAINTENANCE SCHEDULE*
COMPONENT
BELTING
PILLOW BLOCK /
FLANGE BEARINGS
UNIT
SAFETY
CHECK
DETAIL OF MAINTENANCE
Inspect belt tracking
Lubricate in dirty, dusty, or
moist/wet conditions
Confirm placement of all guards, pop-out
rollers, warning labels & check for loose
bolts, nip points & other hazards
MONTHLY RECOMMENDED MAINTENANCE SCHEDULE*
COMPONENT
GEAR REDUCER
BELTING
PILLOW BLOCK /
FLANGE BEARINGS
DRIVE CHAIN
DRIVE SPROCKETS
DETAIL OF MAINTENANCE
Check for leaks
Inspect belt tracking
Lubricate in dirty, dusty, or
moist/wet conditions
Check for proper operating tension &
overall wear & lubricate
Check for overall wear & re-tighten set screws
PERIODIC RECOMMENDED MAINTENANCE SCHEDULE*
COMPONENT
GEAR REDUCER
DRIVE CHAIN
MOTOR
DETAIL OF MAINTENANCE
Check for leaks
Clean (brush in solvent) & re-lubricate by ap-
plying lubricant to inside of chain with brush
or spout can at 2000 hour intervals
Check & clear motor ventilation openings
at 500 hour intervals. Check miscellaneous
operating conditions (normal heat & noise)
MISC. LUBRICANTS**
General Purpose Grease
(For -30°F to 300°F operation)*
For Extreme Temperature Operation
(-90°F to 350°F operation)*
Washdown Application*
(-30°F to 225°F operation)
(May require special consideration
consult factory)
General Purpose Oil
Shell Dolium R (Shell Oil Co.)
(or suitable equivalent)
Mobiltemp SHC-32 (Mobil Oil Corp.)
(or suitable equivalent)
Shell Alvania No. 3 (Shell Oil Co.)
(or suitable equivalent)
SAE 10; SAE 20 OR SAE 30
*All charts are for guidelines in normal operating or ‘as noted’ conditions. Severe applications warrant additional maintenance.
**
Содержание 450BOS
Страница 1: ...Installing and Maintaining Your Roach Conveyor...
Страница 17: ...MODEL 725TB END DRIVE END side mount DRIVE center drive drawings 17...
Страница 26: ...MODEL 796RB END DRIVE END side mount DRIVE center drive drawings 26...
Страница 29: ...MODEL 751RB END DRIVE END side mount DRIVE center drive drawings 29...