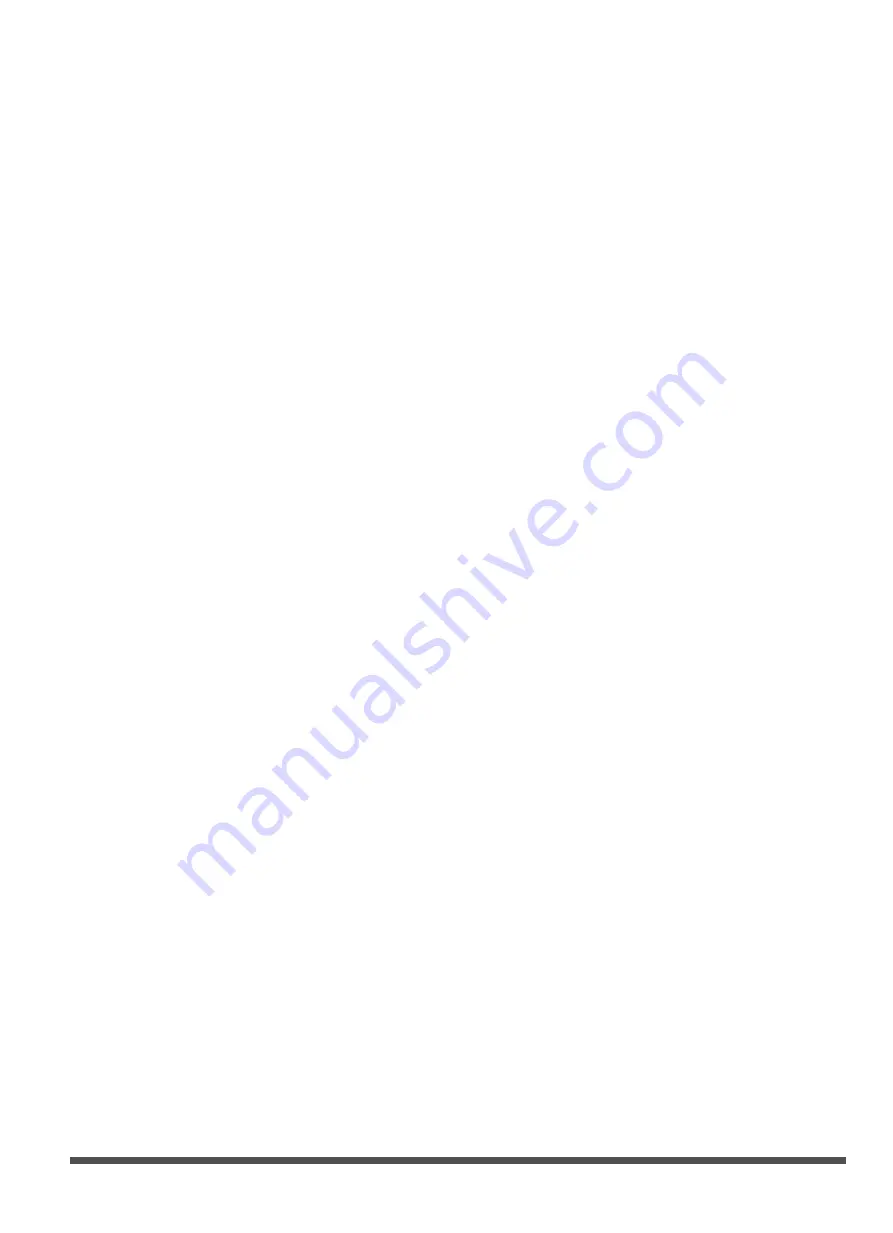
Safety
cylinders. (No more than 80 % volume liquid charge). i) Do not exceed the maximum working
pressure of thecylinder, even temporarily. j) When the cylinders have been filled correctly and the
process completed, make sure that the cylinders and the equipment are removed from site promptly
and all isolation valves on the equipment are closed off. k) Recovered refrigerant shall not be charged
into another refrigeration system unless it has been cleaned and checked.
15.Labelling
Equipment shall be labelled stating that it has been de-commissioned and emptied of refrigerant. The
label shall be dated and signed. Ensure that there are labels on the equipment stating the equipment
contains flammable refrigerant.
16.Recovery
When removing refrigerant from a system, either for servicing or decommissioning, it is recommended
good practice that all refrigerants are removed safely. When transferring refrigerant into cylinders,
ensure that only appropriate refrigerant recovery cylinders are employed. Ensure that the correct
number of cylinders for holding the total system charge is available. All cylinders to be used are
designated for the recovered refrigerant and labelled for that refrigerant (i.e. special cylinders for the
recovery of refrigerant). Cylinders shall be complete with pressure relief valve and associated shut-off
valves in good working order. Empty recovery cylinders are evacuated and, if possible, cooled before
recovery occurs. The recovery equipment shall be in good working order with a set of instructions
concerning the equipment that is at hand and shall be suitable for the recovery of flammable refrigerants.
In addition, a set of calibrated weighing scales shall be available and in good working order. Hoses shall
be complete with leak-free disconnect couplings and in good condition. Before using the recovery
machine, check that it is in satisfactory working order, has been properly maintained and that any
associated electrical components are sealed to prevent ignition in the event of a refrigerant release.
Consult manufacturer if in doubt. The recovered refrigerant shall be returned to the refrigerant supplier
in the correct recovery cylinder, and the relevant Waste Transfer Note arranged. Do not mix refrigerants
in recovery units and especially not in cylinders. If compressors or compressor oils are to be removed,
ensure that they have been evacuated to an acceptable level to make certain that flammable refrigerant
does not remain within the lubricant. The evacuation process shall be carried out prior to returning the
compressor to the suppliers. Only electric heating to the compressor body shall be employed to
accelerate this process. When oil is drained from a system, it shall be carried out safely.
Before carrying out this procedure, it is essential that the technician is completely familiar with the
equipment and all its detail. It is recommended good practice that all refrigerants are recovered safely.
Prior to the task being carried out, an oil and refrigerant sample shall be taken in case analysis is
required prior to re-use of reclaimed refrigerant. It is essential that electrical power is available before
the task is commenced.
14.Decommissioning
a) Become familiar with the equipment and its operation. b) Isolate system electrically. c) Before
attempting the procedure ensure that: Mechanical handling equipment is available, if required, for
handling refrigerant cylinders;All personal protective equipment is available and being used correctly;
The recovery process is supervised at all times by a competent person; Recovery equipment and
cylinders conform to the appropriate standards. d) Pump down refrigerant system, if possible. e) If a
vacuum is not possible, make a manifold so that refrigerant can be removed from various parts of the
system. f) Make sure that cylinder is situated on the scales before recovery takes place. g) Start the
recovery machine and operate in accordance with manufacturer's instructions. h) Do not overfill
23