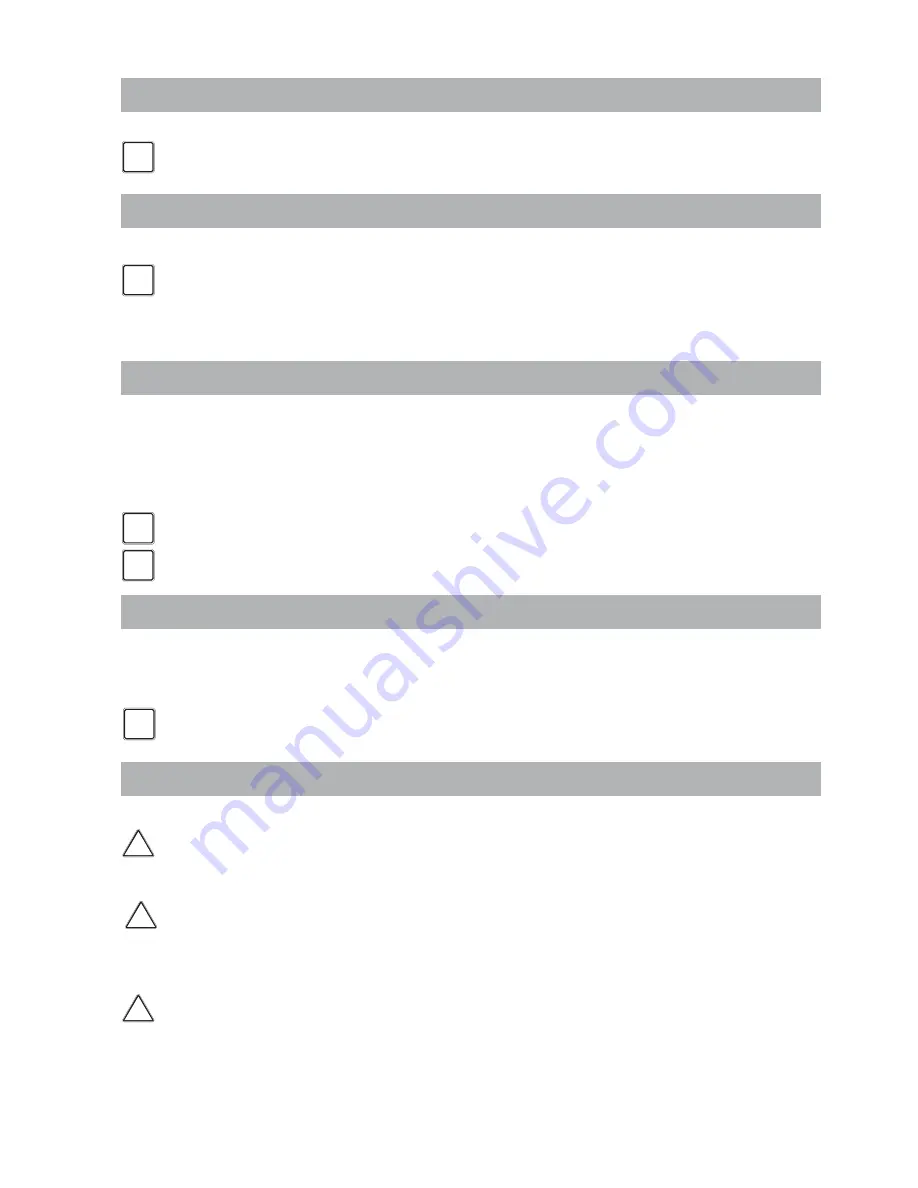
Installation & Servicing Instructions Rinnai E-Series
20
NOTICE
i
NOTICE
i
6.1.1
Safety valve
An ASME 30 psi pressure relief valve is included with the boiler and must be
fi tted before any shut off valve in the system.
6.1.2
Low water cut off
The Rinnai E boiler has a factory installed pressure sensor type Low Water Cut
Off (LWCO). Check your local codes to see if a Low Water Cut Off is required
(LWCO) and if this device conforms to local code.
The boiler's internal low water cut off is not serviceable or adjustable .
6.2
Boiler expansion tank
Choose an expansion tank volume, of which is geared to the installation’s water
capacity. The pre-charge pressure depends on the installation height above the
expansion tank. Fit the expansion tank into the return pipe as close as possible to
the boiler return connection. The expansion tank should be sourced locally. Please
refer to the expansion tank manufacturer for further information.
Fill the expansion tank to a minimum of 14.5 psi.
The boiler cannot be used with an open type expansion tank.
6.3
Underfl oor heating system (plastic pipes)
When using oxygen-permeable tubing, e. g. for underfl oor heating systems, the
system must be separated using plate heat exchangers.
No recourse can be made to the terms of the limited warranty in the event of
failure to observe the regulations pertaining to plastic underfl oor heating pipes.
6.4
Gas supply connection
Only work on gas lines if you are licensed for such work.
If these instructions are not followed exactly, a fi re or explosion may result
causing property damage, personal injury or death.
Rinnai wall mounted E boilers are built to run on their specifi ed gas type either
Natural Gas or Liquid Propane (not for E50CRN). The gas type the boiler is
suitable for is indicated on the packaging and on the boiler by a blue label with
Natural Gas and on the identifi cation plate on the boiler.
First check the identifi cation plate on the boiler for the suitable gas type.
Do not use the boiler for another type of gas than indicated on the identifi cation
plate of the boiler. This will cause improper functioning and can damage the
boiler.
NOTICE
i
!
DANGER
!
DANGER
!
WARNING
NOTICE
i
NOTICE
i