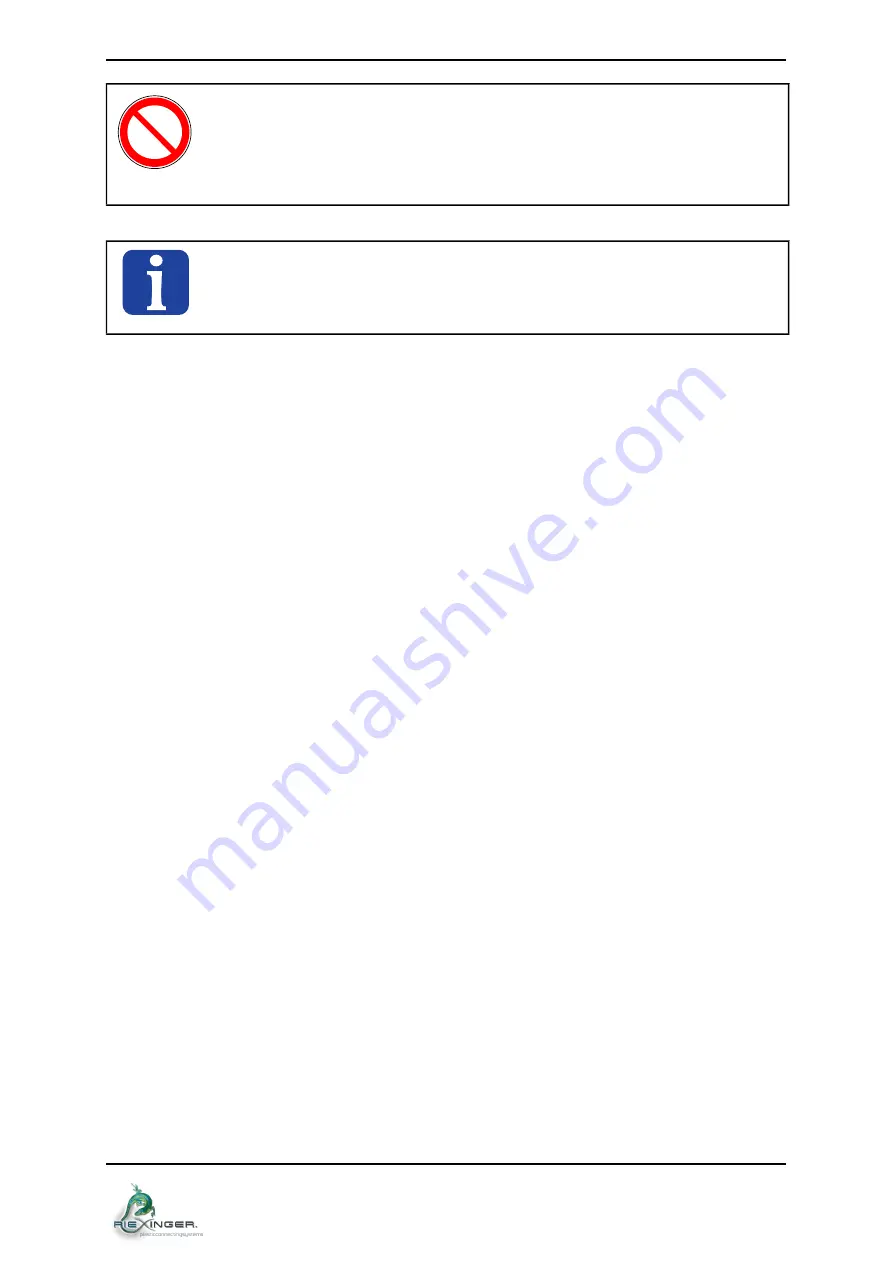
6
1. Important basic information
Attention!
This symbol gives important information for properly handling the machine.
Disregarding such notices may result in malfunctions or material damage
of the
machine or cause damage to the environment
.
Information
This symbol provides
instructions
and particularly useful information. Such infor-
mation helps you use all functions of your machine optimally.
1.4 Used notation styles
This operating manual uses the following notation styles:
l
Words or sentences with emphasised meaning are written in
italics
.
l
Control elements
on the control panel are written in blue font.
l
The instructions, which the operator follows to perform specific functions, always begin
with a number or a letter. Activities or notifications, which the machine uses as a response
to executed instructions, are marked with a preceding full stop, e.g.:
1. Instruction
a. Instruction
l
Response or notification from machine
1.5 Used abbreviations
IndSafReg
Industry Safety Regulations (German implementation of Guideline 2009/104/EG)
DGUV
Roule 3
German Social Accident Insurance (electrical facilities and manufacturing equip-
ment) of the Professional Association for Health and Social Welfare
BSM
Band saw machine
GFP
Glass fibre-reinforced plastic
PE
Polyethylene (thermo-plastic synthetics)
PP
Polypropylene (partial crystalline thermo-plastic synthetics)
PVDF
Polyvinylidene fluoride (opaque, partial crystalline thermo-plastic fluorine syn-
thetics)
APR
Accident Prevention Regulations
BSM 631 / BSM 800 / BSM 1000
Содержание BSM 1000
Страница 2: ...Status April 2016 Eugen Riexinger GmbH Co KG...
Страница 6: ...4 BSM 631 BSM 800 BSM 1000...
Страница 22: ......
Страница 26: ......
Страница 54: ......
Страница 69: ...9 Maintenance 67 Date Activity Next maintenance Name BSM 631 BSM 800 BSM 1000...
Страница 70: ......
Страница 74: ...72 11 Annex BSM 631 BSM 800 BSM 1000...
Страница 76: ...74 11 Annex BSM 631 BSM 800 BSM 1000...
Страница 77: ...11 Annex 75 11 3 Dimenson sheets 11 3 1 Dimension sheet BSM 631 BSM 631 BSM 800 BSM 1000...
Страница 78: ...76 11 Annex BSM 631 BSM 800 BSM 1000...
Страница 79: ...11 Annex 77 11 3 2 Dimension sheet BSM 800 BSM 631 BSM 800 BSM 1000...
Страница 80: ...78 11 Annex BSM 631 BSM 800 BSM 1000...
Страница 81: ...11 Annex 79 11 3 3 Dimension sheet BSM 1000 BSM 631 BSM 800 BSM 1000...
Страница 82: ...80 11 Annex BSM 631 BSM 800 BSM 1000...
Страница 84: ...82 11 Annex 11 5 Pneumatic diagram optional BSM 631 BSM 800 BSM 1000...
Страница 86: ......