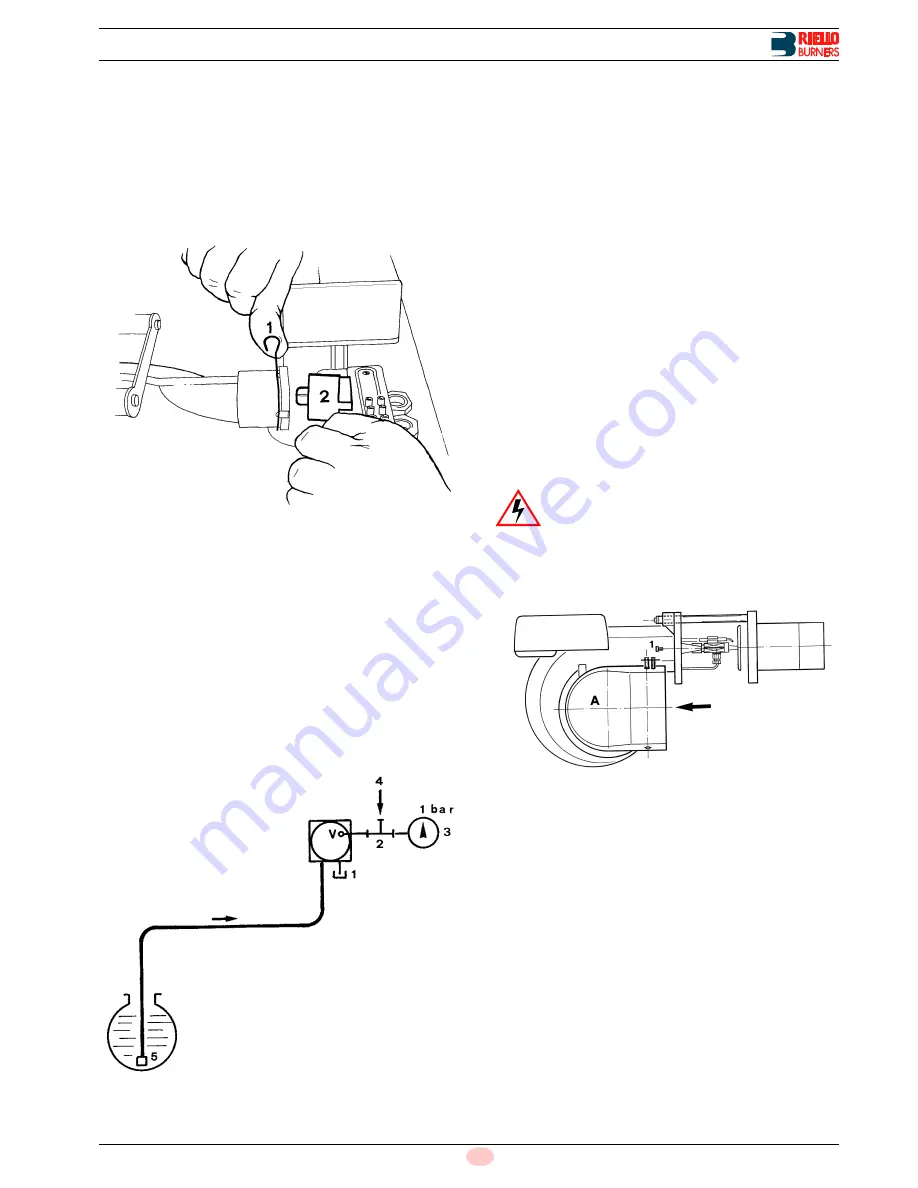
31
20033090
GB
Maintenance
Nozzles
Do not clean the nozzle opening; do not even open it. The nozzle
filter however may be cleaned or replaced as required. Replace
the nozzle every 2-3 years or whenever necessary. After chang-
ing the nozzle, the combustion must be checked.
Photocell (Fig. 33)
Clean the glass cover from any dust that may have accumulated.
In order to extract the photocell 2) from its seat, raise the spring
1).
Hoses
Check to make sure that the hoses are still in good condition and
that they are not crushed or otherwise deformed. Check periodi-
cally the flexible pipes conditions. Using kerosene, they have to
be replaced at least every 2 years.
Gas oil fuel supply line (Fig. 34)
If the previous checks have suggested that air may be entering
the circuit somewhere, pressurize the circuit piping. Plug the
pump's return line connector 1)(Fig. 34) after removing the hose.
Install a union T 2)(Fig. 34) on the vacuum meter attachment. On
one branch of the T install the pressure gauge 3) and on the other
branch 4) inject air at a pressure of 1 bar. After the injection of air
has stopped, the gauge reading should remain stable. The suc-
tion piping must be equipped with a foot valve 5).
Fuel tank
Approximately every 5 years, or whenever necessary, suck any
water or other impurities present on the bottom of the tank using
a separate pump.
Boiler
Clean the boiler as indicated in its accompanying instructions in
order to maintain all the original combustion characteristics in-
tact, especially the flue gas temperature and combustion cham-
ber pressure. Lastly, check the condition of the flue gas stack.
Close the burner and apply power.
If the combustion characteristics measured at the beginning of
the control operation do not match the values listed in the previ-
ous inspection's technical report sheet or fail to provide satisfac-
tory combustion, the burner must be re-calibrated.Write the new
values down on the data sheet illustrated on page 33 or a similar
document. These values will be useful for comparison during fu-
ture checks. Lastly, check to make sure that the fan air gate valve
is in good condition and that the screws are tightly locked. The
tightness of the screws that fasten the cables to the burner termi-
nal block must also be checked. Clean the outside surfaces of the
burner and spray all parts that show signs of rusting with silicon
rust-preventer.
8.2.3
Opening the burner
Unscrew the screws 1)
Pull back part A while keeping it slightly lifted.
Other control measurements
Check the parameters listed in the data sheet on page 33.
Significant differences with respect to the previous measure-
ments indicate the points where more care should be exercised
during maintenance.
Once these controls and measurements have been performed,
stop the burner, disconnect the power supply, and close the man-
ual valves on the fuel lines and open the burner.
Fig. 33
D2561
Fig. 34
D387
DANGER
Disconnect the electrical supply from the
burner.
D421
Fig. 35
Содержание PRESS GBV
Страница 2: ......
Страница 38: ......
Страница 39: ......
Страница 40: ...Subject to modifications RIELLO S p A I 37045 Legnago VR Tel 39 0442 630111 http www rielloburners com...