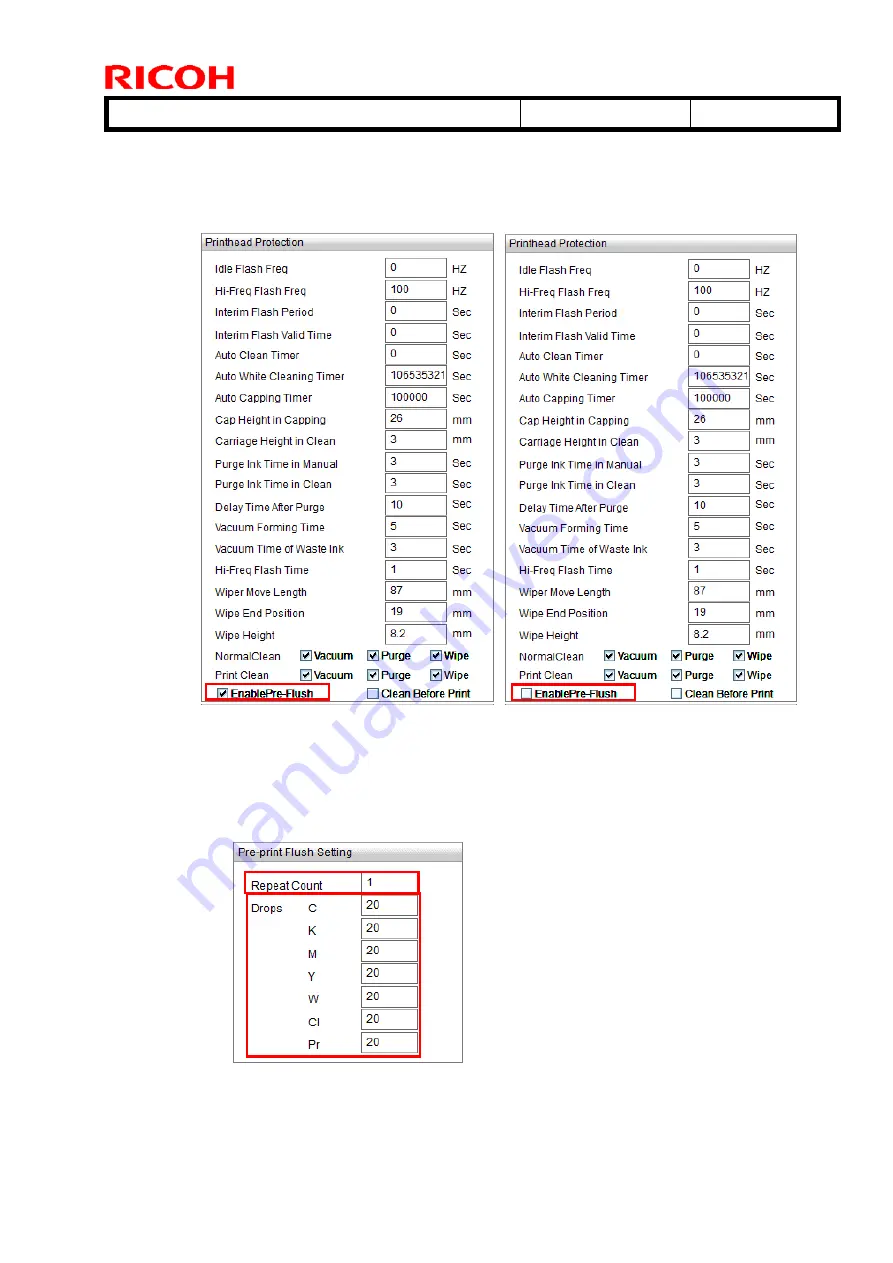
T
echnical
B
ulletin
PAGE: 2/3
Model: Shepherd-Lt
Date: 21-Aug-19
No.: RM0D4007
4.
Print Option->Printhead Protection
Enable Pre-Flush
:ON (For using GP120 ink or DG130 ink)
:OFF (For using T7210 ink)
<GP120 ink, DG130 ink> <T7210 ink>
5.
Maintenance->Motion->Pre-print Flush Setting
<GP120 ink, or DG130 ink>
Repeat Count
:1
Drops
:All 20