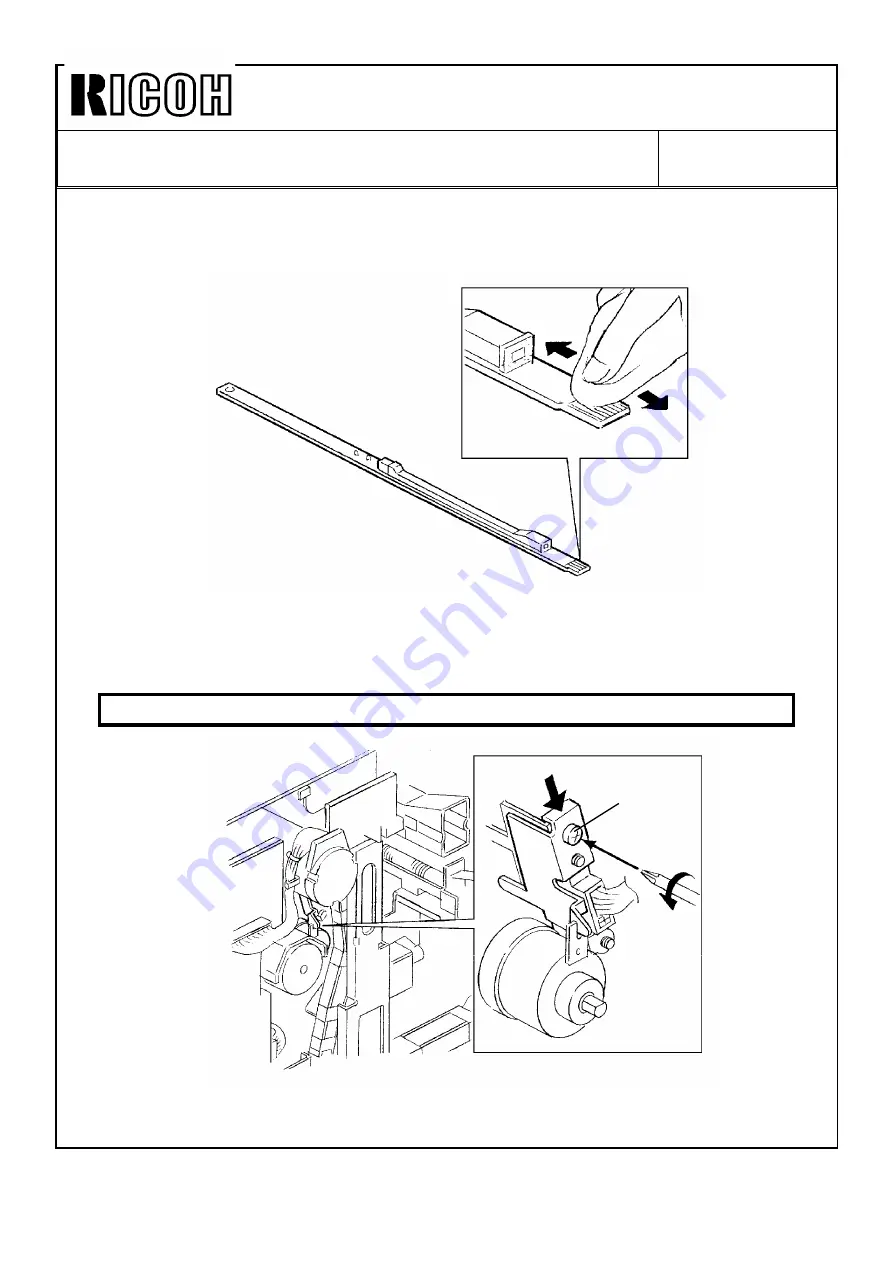
Technical Bulletin
No. RTB-015
SUBJECT: Blinking Wrench Mark
DATE: Feb. 15, ’92
PAGE: 2 of 2
2. (1) Remove the ID sensor board.
(2) Clean the connector of the ID sensor board (both faces) using a soft cloth with
alcohol.
(3) Reassemble the ID sensor board.
(4) Remove the upper rear cover.
(5) Loosen the screw of the ID sensor connector bracket [A] then tighten the screw
while pushing down the bracket.
CAUTION: Make sure that you do not turn the bracket when tightening the screw.
(6) Check the value of Vsg and Vsp using SP55 (the value of Vsg should be around 4.0
V)
[A]