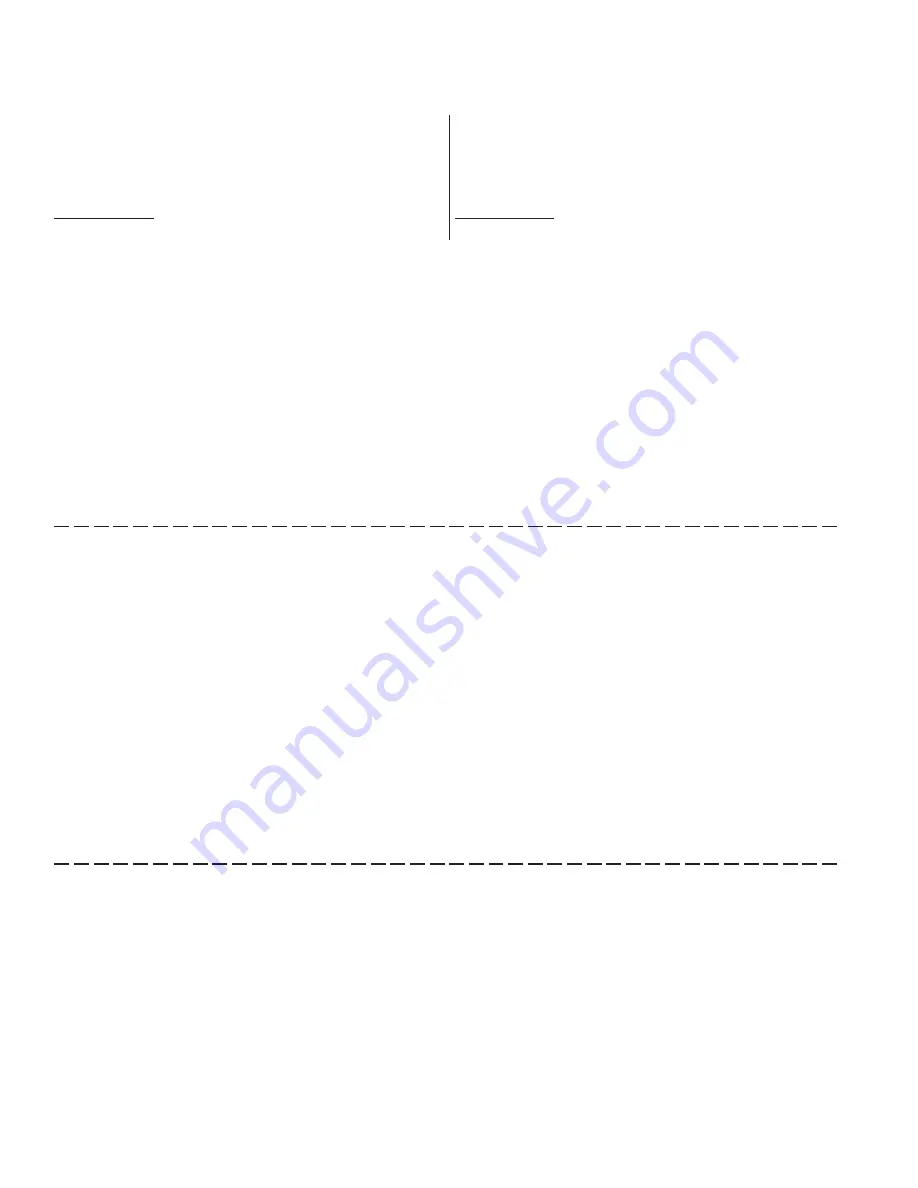
Page 22
13. Check-Test Start (cont'd)
Startup (cont'd)
o
Turn on the disconnect switch and re-check the slope gauge. If air
pressure differential is within the limits of -.25" to -.75" w.c., no further
adjustment is required. If the air pressure differential is not within those
limits, re-adjust the blower speed.
o
When the differential air pressure is within the limits, check the motor
amp draw with an ammeter to be sure that the motor is not overloaded.
Amps are shown on the motor nameplate.
o
If an inlet or outlet duct system is attached to the heater, run the blower to
purge the volume of air from the duct system with at least four air
changes.
o
Turn the blower switch to OFF and damper test switch to RUN. Turn the
disconnect switch OFF. Disconnect the manometer and the slope gauge.
Replace the tubing caps.
ring will result in .233" change in pitch diameter. To increase
blower speed, decrease diameter. CAUTION: Do not adjust
sheaves in either direction to the point where moveable and
stationary flanges are in contact.
(d) Re-tighten the locking screws.
All Motor Sizes - Replace the belts and check belt tension. Be
sure that belts are aligned in the pulley grooves and are not
angled from pulley to pulley.
ring will result in .233" change in pitch diameter. To
decrease blower speed, increase diameter. CAUTION: Do
not adjust sheaves in either direction to the point where
moveable and stationary flanges are in contact.
(d) Re-tighten the locking screws.
All Motor Sizes - Replace the belts and check belt tension. Be
sure that belts are aligned in the pulley grooves and are not
angled from pulley to pulley.
DETERMINE the type of gas control system from the Model or Serial No. Suffix on the unit rating plate:
Suffix ..... Where ............ Option ................ Gas Control System
None ...... N/A ................. AG1 ..................... Single Stage with Air Controller
-2 ........... Model No. ...... AG3 ..................... Two Stage with Two-Stage Ductstat
-MV-7 .... Serial No. ....... AG30 or AG31 ..... Maxitrol Series #14 Outside Air Only (Amplifier A1014)
-MV-8 .... Serial No. ....... AG32 ................... Maxitrol Series #14A Outside Air Only (Amplifier A1014)
-MV-9 .... Serial No. ....... AG33 ................... Maxitrol Series #44 Outside Air Only (Amplifier A1044)
-MV-B ... Serial No. ....... AG36 ................... Paint Spray Booth System (Maxitrol 94)
-MV-C ... Serial No. ....... AG37 ................... Maxitrol Series #DDC for Outside Air Only (Signal Conditioner A200)
-MV-D ... Serial No. ....... AG47 ................... Maxitrol Series #14 Outside Air and Recirculation (Amplifier ADFM14)
-MV-E .... Serial No. ....... AG48 ................... Maxitrol Series #44 Outside Air and Recirculation (Amplifier ADFM44)
-M .......... Model No. ...... AG49 ................... Mechanical Modulation, 40-160°F
-M .......... Model No. ...... AG50 ................... Mechanical Modulation, 40-120°F
-MV-F .... Serial No. ....... AG51 ................... Maxitrol Series DDC for Outside Air and Recirculation
For units with Maxitrol Series 14 or 14A, remove and individually tape wires from Terminals #4 and #8 on the amplifier
For units with Maxitrol Series 44, remove and individually tape wires from Terminals #2, #4 and #8 on the amplifier
For units with Maxitrol Series DDC, the customer provided input signal must be 4-20 milliamps (conditioner
dip switch "on") or 0-10 volt DC (conditioner dip switch "off").
3. Check pilot and burner ignition and pilot operation (hot surface ignition)
o
Turn the disconnect switch ON. Turn blower service switch and burner
service switch to TEST position.
o
Observe for ignition through the viewport.
Check for lights - Lights listed in prior Steps should be energized. After
15-20 seconds, the "Pilot Valve" light will light to signal the pilot igni-
tion, followed by the "Main Valve" light signaling main burner operation.
o
With both the burner and blower operating, measure the gas pressure at
the burner. Gas pressure should match the required manifold pressure
listed on the rating plate. (If pressure does not match the required pres-
sure, further testing is required in Step 5.) Remove the manometer.
o
Leak test all connections in the pilot and main burner supply lines.
WARNING: DO NOT TEST WITH OPEN FLAME.