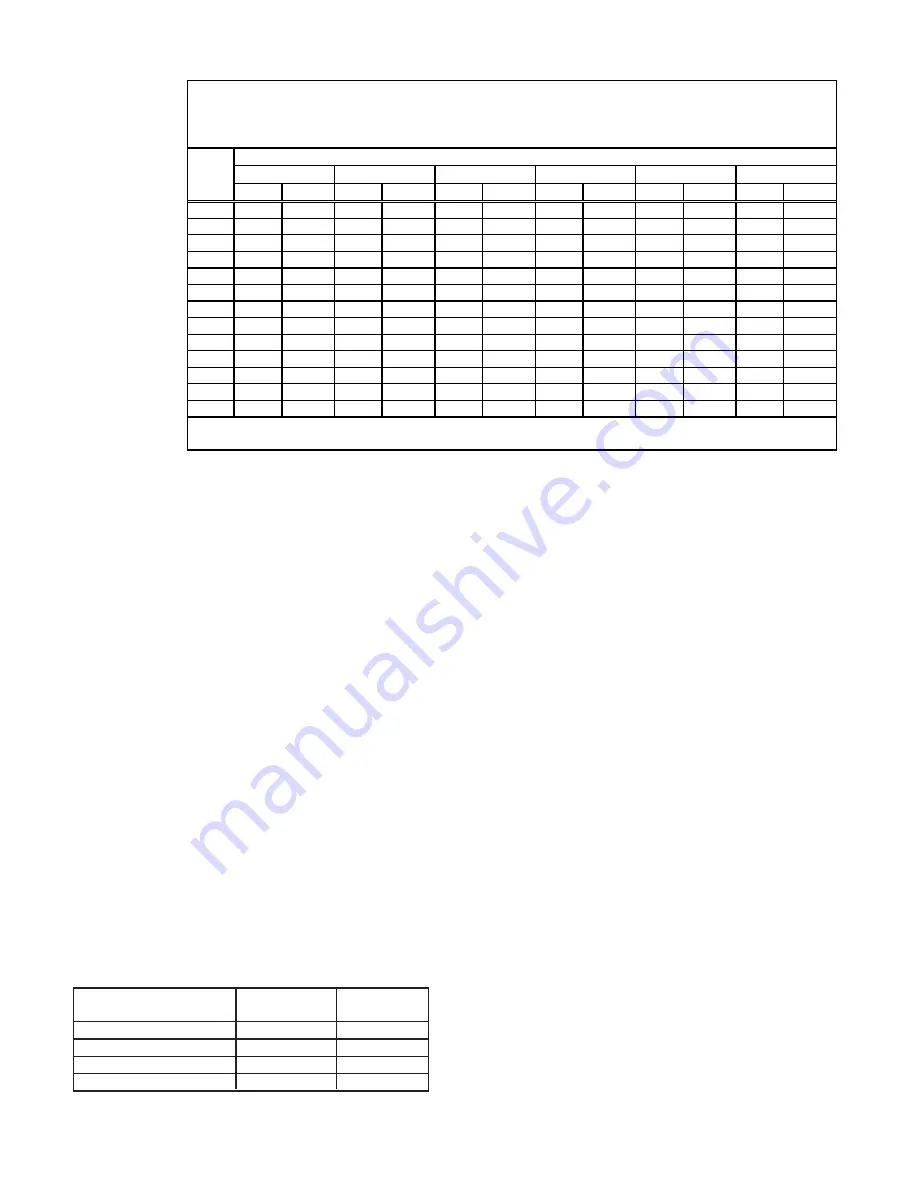
Form 433-CV/LN, Page 12
is in operation and on standby. Incorrect inlet pressure could cause
excessive manifold gas pressure immediately or at some future time. If
natural gas supply pressure is too high, install a regulator in the supply
line before it reaches the heater. If natural gas supply pressure is too
low, contact your gas supplier.
Instructions on How to Check Manifold Pressure
(can only be done after heater is installed):
1) With the manual valve positioned to prevent flow to the main burn-
ers, connect a manometer to the 1/8" pipe outlet pressure tap in the
valve. NOTE: A manometer (fluid-filled gauge) is recommended rather
than a spring type gauge due to the difficulty of maintaining calibra-
tion of a spring type gauge.
2) Open the valve and operate the heater. Measure the gas pressure to
the manifold. Normally adjustments should not be necessary to the
factory preset regulator.
If adjustment is necessary, set pressure to correct settings by turning
the regulator screw IN (clockwise) to increase pressure. Turn regulator
screw OUT (counterclockwise) to decrease pressure.
Derating by Manifold Pressure Adjustment for
High Altitude Operation
If the heater is being installed between 2000 and 5000 ft (610 to 1525M)
and it was determined in Paragraph 4 that derating by manifold pres-
sure adjustment is permissible, follow the instructions below.
Instructions for Derating a Heater by Adjusting Manifold
Pressure
1. Determine the required manifold pressure for the elevation where
the heater will be operating. If unsure of the elevation, contact the
local gas supplier.
Manifold Pressure Settings by Elevation
Altitude
Natural Gas
Propane Gas
Feet
Meters
(inches W.C.)
(inches W.C.)
0- 2000
1-610
3.5
10.0
2001-3000
911-915
2.8
7.7
3001-4000
916-1220
2.5
7.1
4001-5000
1221-1525
2.3
6.4
2. With the manual valve positioned to prevent flow to the main burn-
ers, connect a manometer to the 1/8” pipe outlet pressure tap in the
Sizing a Gas
Supply Line
Capacity of Piping
Cubic Feet per Hour based on 0.3" w.c. Pressure Drop
Specific Gravity for Natural Gas -- 0.6 (Natural Gas -- 1000 BTU/Cubic Ft)
Specific Gravity for Prop ane Gas -- 1.6 (Propane Gas -- 2550 BTU/Cubic Ft)
Length
Diameter of Pipe
of 1/2"
3/4"
1"
1-1/4"
1-1/2"
2"
Pipe
Natural Propane Natural Propane Natural Propane Natural Propane Natural Propane Natural Propane
20'
92
56
190
116
350
214
730
445
1100
671
2100
1281
30'
73
45
152
93
285
174
590
360
890
543
1650
1007
40'
63
38
130
79
245
149
500
305
760
464
1450
885
50'
56
34
115
70
215
131
440
268
670
409
1270
775
60'
50
31
105
64
195
119
400
244
610
372
1105
674
70'
46
28
96
59
180
110
370
226
560
342
1050
641
80'
43
26
90
55
170
104
350
214
530
323
990
604
90'
40
24
84
51
160
98
320
195
490
299
930
567
100'
38
23
79
48
150
92
305
186
460
281
870
531
125'
34
21
72
44
130
79
275
168
410
250
780
476
150'
31
19
64
39
120
73
250
153
380
232
710
433
175'
28
17
59
36
110
67
225
137
350
214
650
397
200'
26
16
55
34
100
61
210
128
320
195
610
372
Note: When sizing supply lines, consider possibilities of future expansion and increased requirements.
Refer to National Fuel Gas Code for additional information on line sizing.
valve. Use a fluid-filled manometer that is readable to the nearest
tenth of an inch w.c.
3. Remove the cap from the pressure adjusting screw and adjust the
manifold pressure to the pressure setting selected from the table.
Cycle the main burners once or twice to properly seat the adjust-
ment spring in the valve.
Re-check the pressure. If necessary, re-adjust the pressure. When
the pressure is correct, remove the manometer and replace the cap.
Check for leaks at the pressure tap fitting.
4. With the heater operating, determine that the inlet pressure to the
heater for natural gas is between 5 and 14 inches w.c. and for pro-
pane between 10 and 14 inches w.c. Take this reading as close as
possible to the heater. (Most heaters are now equipped with gas
valves that have an inlet pressure tap.) If the inlet pressure is not
within the specified range, the inlet pressure must be corrected
and Steps 3 and 4 repeated.
5. Find the Manifold Pressure Adjustment label in the plastic bag that
contained these instructions. Using a permanent marker, fill-in the
pressure setting. Adhere the label on the heater near the gas valve
so that it is conspicuous to someone servicing the valve and/or heater.
13. Electrical Supply and
Connections
All electrical wiring and connections, including electrical grounding
MUST be made in accordance with the National Electric Code ANSI/
NFPA No. 70 (latest edition) or, in Canada, the Canadian Electrical
Code, Part I-C.S.A. Standard C22.1. In addition, the installer should
be aware of any local ordinances or gas company requirements that
might apply.
Check the rating plate on the heater for the supply voltage and current
requirements. A dedicated line voltage supply with fused disconnect
switch should be run directly from the main electrical panel to the heater.
All external wiring must be within approved conduit and have a mini-
mum temperature rise of 60°C
.
Conduit from the disconnect switch
must be run so as not to interfere with the service panels of the heater.
The electrical supply and control wiring enter at the rear of the heater
and connect to the integrated circuit board. The 115 volt supply wiring
connects to pigtails on the lower portion of the circuit board. The ter-
minal strip for 24 volt thermostat connections is located on the upper
portion of the circuit board. See Figure 7.
12. Gas Piping and Pressures (cont'd)
Manifold or Orifice Pressure Settings (cont'd)