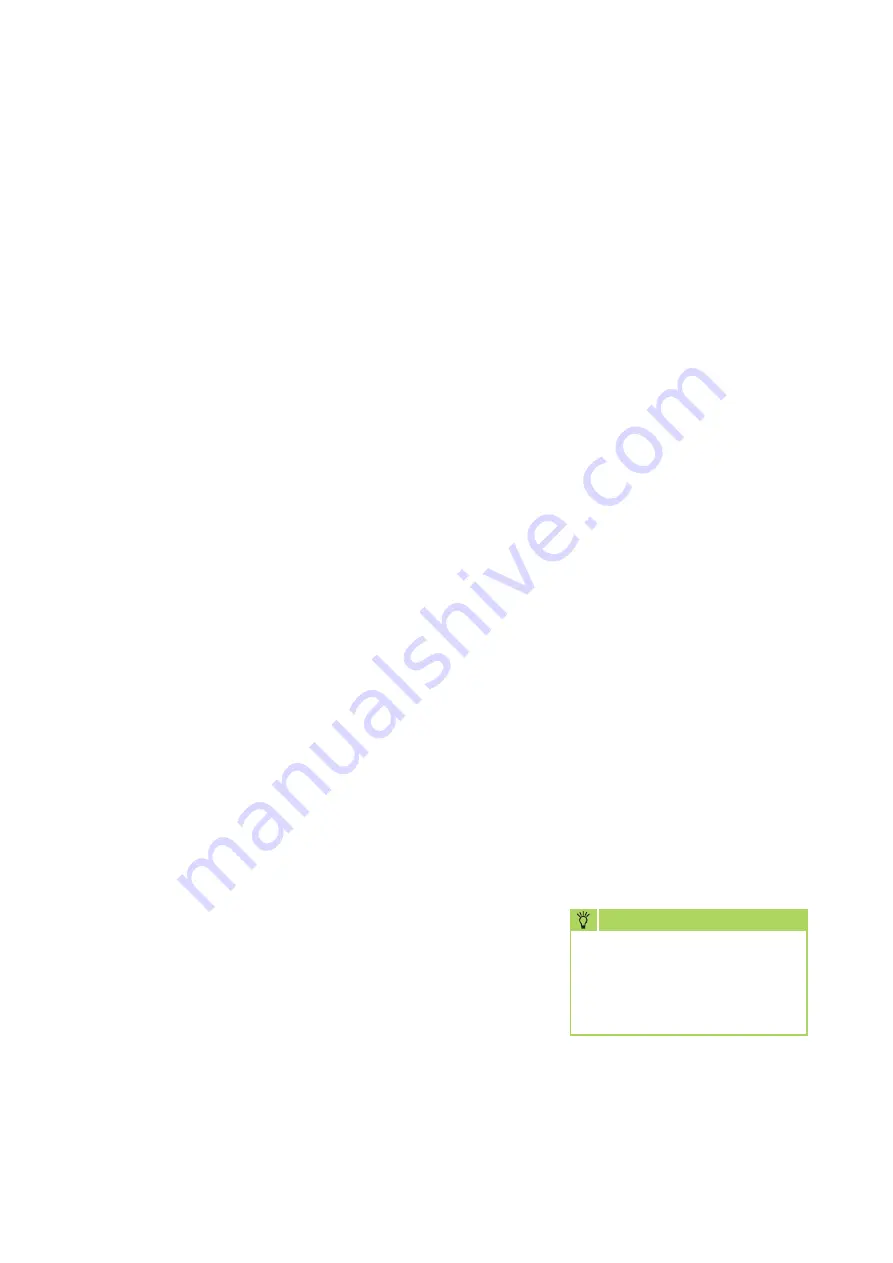
Commissioning
■
Commissioning should only be
performed and documented by
specially trained personnel.
■
Observe the manuals for the
unit and all other components
when commissioning the entire
system.
Function test for cooling operating
mode
1. Switch the power supply on
and if necessary open all shut-
off valves.
2. Switch on the chiller, the heat
pump and the corresponding
circulation pump. The outlet
temperature must be between
+4 and +18°C.
3. Use the controller to switch on
the unit and select the cooling
mode, maximum fan speed and
lowest target temperature.
4. Measure and record all
the required values in the
commissioning report and
check the safety functions.
5. Check the unit control system
using the functions described in
the Chapter "Operation".
6. Check that the condensate
drainage line is functioning
correctly by pouring distilled
water into the condensate tray.
Function test of heating operating
mode
1. Switch the power supply
on and if necessary open all
shut-off valves.
2. Switch on the chiller, the heat
pump and the corresponding
circulation pump. The outlet
temperature must be between
+35 and +70°C.
3. Use the controller to switch on
the unit and select the heating
mode, maximum fan speed and
highest target temperature.
4. Measure and record all
the required values in the
commissioning report and
check the safety functions.
5. Check the unit control system
using the functions described in
the Chapter "Operation".
Final tasks
■
Reassemble all disassembled
parts.
■
Familiarise the operator with
the system.
Before commissioning
Anti-freeze protection for the
medium
If a water-glycol mixture is used,
it is to be pre-mixed before being
put in the system. The desired
concentration must then be
checked.
Bleeding the system
■
Air may still be in the pipe
lines after the leak test. This
is carried to the automatic
bleeding valves or the
consumer by the operation of
the circulation pump. In this
case it is necessary to bleed the
system again.
■
The non-circulating pressure
must then be adjusted to the
required system pressure.
During manual bleeding, any
glycol mixtures which escape
must be disposed of separately.
Do not feed them into the
condensate tray!
NOTE
MAG
■
The preliminary pressure for the
diaphragm expansion vessel
must be adjusted individually to
the system layout, the volume
of the medium and the
installation site.
Valves for hydronic balancing
■
The calculated excess pressure
in the pipe network layout
at the individual cold water
consumers must be adjusted at
the hydronic balancing valves.
Safety valve
■
The safety valves and their
correct function must be
checked.
■
The drain line for the valves is
to be checked for function and
leak tightness.
REMKO KWK -4R
16
Содержание KWK 100-4R
Страница 2: ......