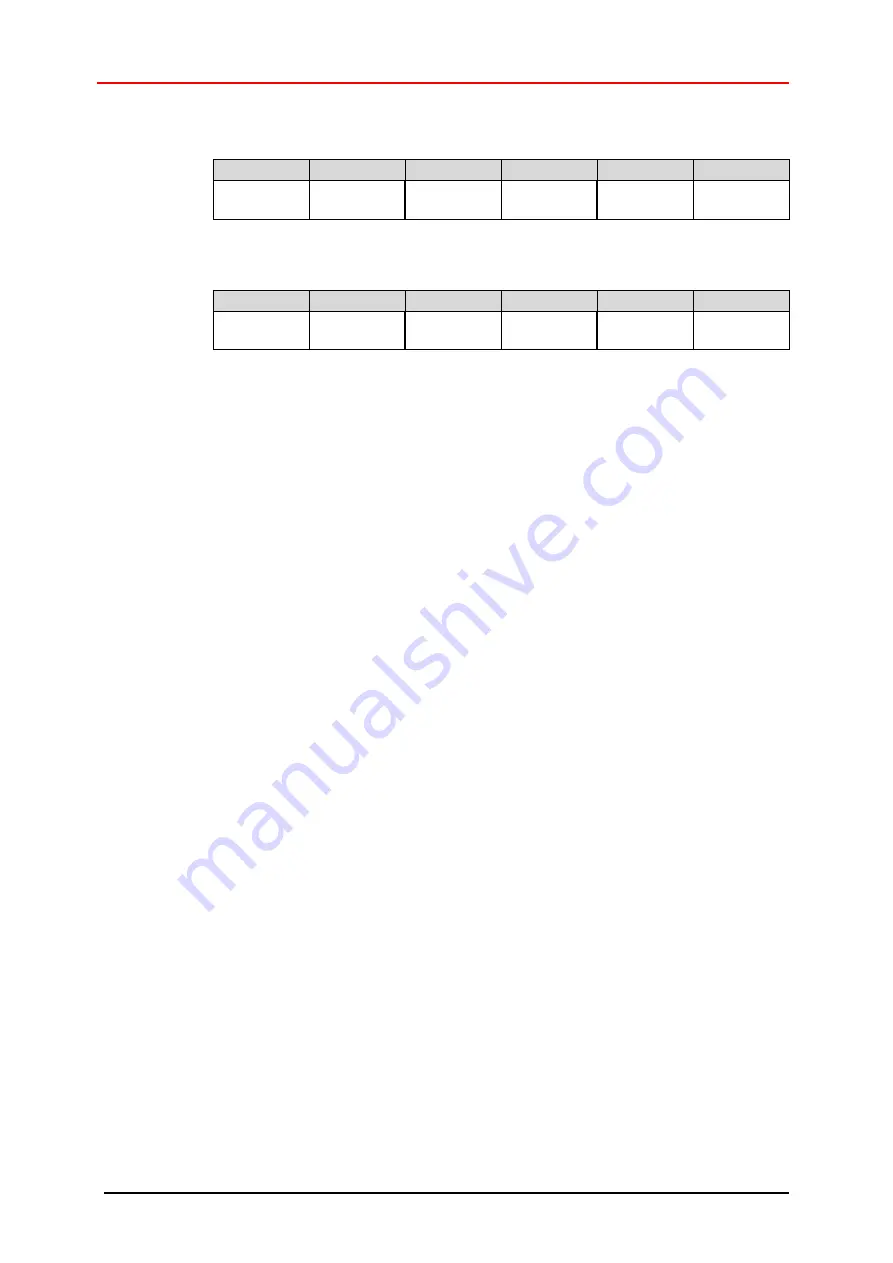
Parameterization
TR-Electronic GmbH 2013, All Rights Reserved
Printed in the Federal Republic of Germany
Page 144 of 175
TR - ECE - BA - DGB - 0102 - 09
01/17/2019
Connection path Attr.-ID 102,
Packed EPATH
with 8 bit class
0x20
0x23
0x24
0x01
0x30
0x66
Logical Type
= Class
Class #23
Logical Type
= Instance
Instance #1
Logical Type
=Attr.-ID
Attr.-ID #102
Connection path Attr.-ID 103,
Packed EPATH
with 8 bit class
0x20
0x23
0x24
0x01
0x30
0x67
Logical Type
= Class
Class #23
Logical Type
= Instance
Instance #1
Logical Type
=Attr.-ID
Attr.-ID #103
This attribute only takes effect after executing service code 0x16
save
or attribute 112
Accept Parameter
.
If it is not possible to enter parameter data in the permitted ranges of numerator and
denominator, the attempt must be made to reduce these accordingly. If this is not
possible, it may only be possible to represent the decimal number affected
approximately. The resulting minor inaccuracy accumulates for real round axis
applications (infinite applications with motion in one direction).
A solution is e.g. to perform adjustment after each revolution or to adapt the
mechanics or gearbox accordingly.
The parameter
"Steps per revolution"
may also be decimal number, however the
"Total measuring range"
may not. The result of the above formula must be rounded
up or down. The resulting error is distributed over the total number of revolutions
programmed and is therefore negligible.
Preferably for linear axes (forward and backward motions):
The parameter
"Revolutions denominator"
can be programmed as a fixed value of
"1". The parameter
"Revolutions numerator"
is programmed slightly higher than the
required number of revolutions. This ensures that the measuring system does not
generate a jump in the actual value (zero transition) if the distance travelled is
exceeded. To simplify matters the complete revolution range of the measuring system
can also be programmed.