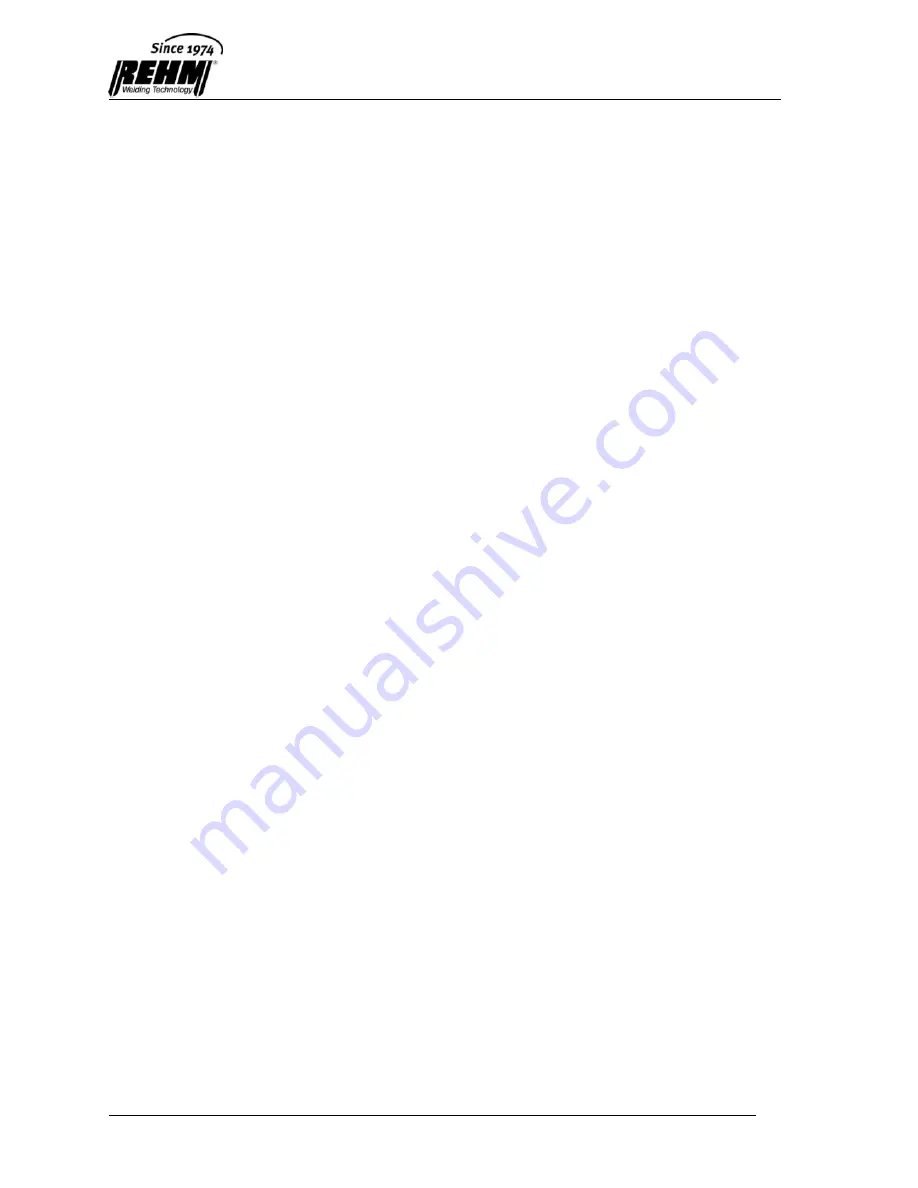
Introduction
8
1.2.1
Performance features of BARRACUDA cutting
equipment
Housing in REHM design
Improved ergonomics thanks to systematic and continuing enhancement of
the REHM design. The protected and well thought-out design means that
protection class IP23 is achieved. The equipment can therefore be used for
cutting outdoors.
REHM high-performance transformers
High-performance transformer with double enamelled wire, insulation class H
(180°C).
High-quality enamelled copper wire is used for all transformers.
All transformer windings are wound in layers, with inter-layer insulation.
REHM thermal protection
All REHM equipment is protected against overheating by thermal sensors.
REHM transistor heavy-duty circuit breaker
The patented REHM transistor heavy-duty circuit breaker, proved in tens of
thousands of instances, permits fine control of the cutting current, which is
continuously adjustable. Precise control with voltage compensation means
that cutting current can be held constant for maximum cut quality. The high
duty cycle values of 60% (10 mins.) are achieved safely through use of only
high-grade service components.
REHM safety system
With the monitoring of torches and wearing parts, with active early warning
and automatic safety shutdown aimed at damage prevention, the logic control
system offers the maximum safety for man and equipment.
REHM cost-effectiveness
Because the controlled pilot current is switched off during cutting and a soft
start function is standard, service life is longer and wear and tear is reduced.
Dependable ignition using REHM Zetronik is possible both for contact and
distant cutting. The quick start function permits immediate ignition, even
during the post-purge gas flow time. The post-purge gas flow time is demand-
oriented. Changing a torch on the central connector is simple and quick.
Material-oriented regulation of high-speed pilot and cutting current allows
uninterrupted cutting of perforated sheets.
1.2.2
Principle of plasma arc cutting
In plasma arc cutting operations, the material is melted using a high-energy arc.
In the plasma torch, air or gas is heated to such high temperatures that an
electrically conductive plasma is produced. The plasma issues from a nozzle as a
concentrated jet at high speed and thus forms the contact between electrode and
workpiece. The high energy density of the jet melts the material to be cut and
simultaneously blows it out of the kerf.
Содержание BARRACUDA RTC 100
Страница 1: ...BARRACUDA RTC 60 100 150 OPERATING INSTRUCTIONS Plasma arc cutting GB...
Страница 7: ...Introduction 7 1 2 General Description Fig 1 BARRACUDA...
Страница 40: ...Circuit Diagrams 40 9 Circuit diagrams...
Страница 41: ...Circuit Diagrams 41...
Страница 42: ...Circuit Diagrams 42...
Страница 45: ...List of Components 45 1 2 3 6 7 4 8 9 10 11 12 13 14 15 42 16 39 17 20 22 5...
Страница 46: ...List of Components 46 38 23 24 25 26 27 60 28 29 30 31 34 E Box 33 35 36 37 32 40 F3 F5...
Страница 47: ...List of Components 47 54 57 55 F1 F2 56 53 59 58 44 47 45 46 52 51 50 48 49 Compressed air unit E Box...
Страница 50: ...Mechanised Interlocks 50 11 4 Connection schematic for A pole mechanised cutting interface...
Страница 55: ...by REHM Printed in Germany No 730 1200 06 2013 GB...