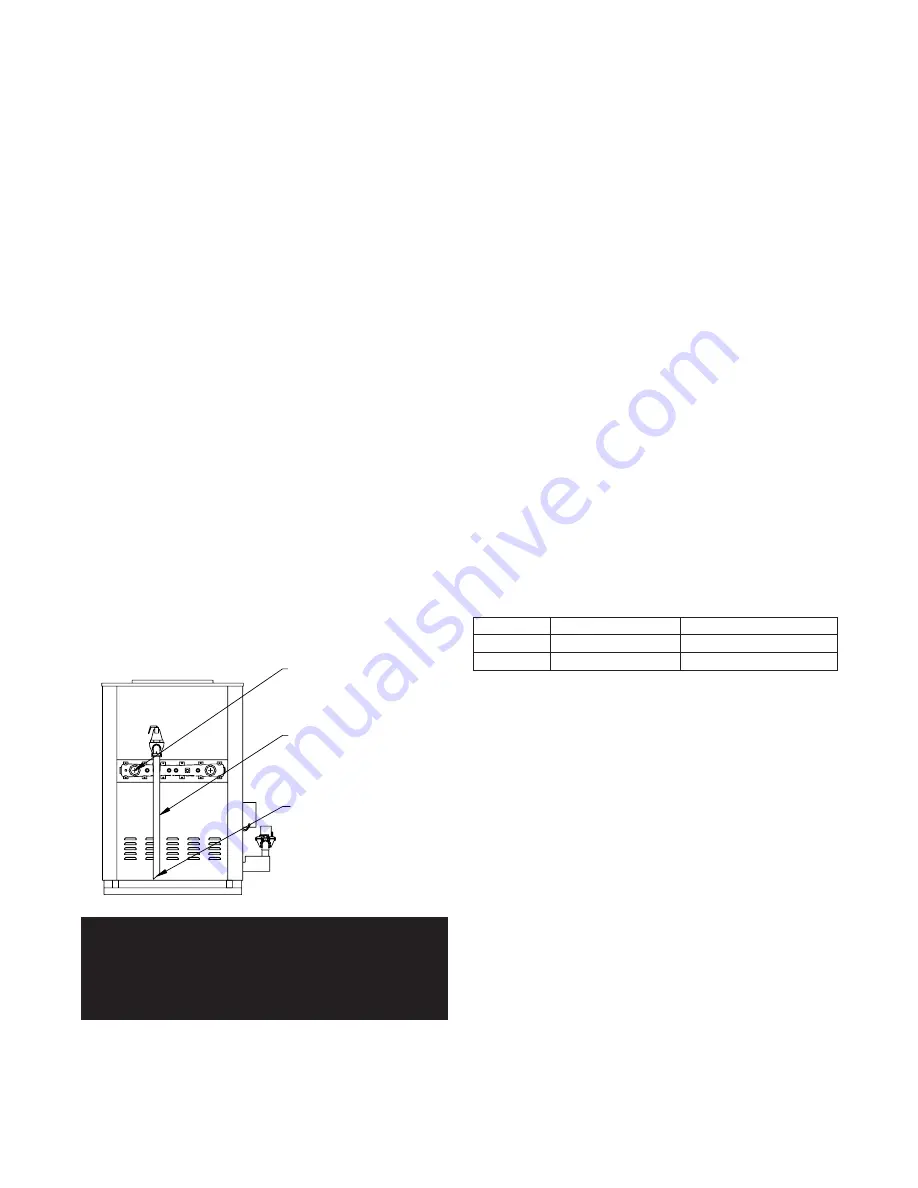
SERIES 8800 & 8900 INSTALLATION AND OPERATING INSTRUCTIONS
Page 10
RIOM-46
OUTLET
INLET
DISCHARGE PIPE SIZE TO
EQUAL VALVE OUTLET
.
DO NOT RESTRICT FLOW.
DISCHARGE SO AS TO AVOID
EXPOSURE OF PERSONS TO
HOT LIQUID OR VAPOR AND
ALLOW COMPLETE DRAINAGE
0F RELIEF VA LVE AND PIPING.
1" (25mm) CLEARANCE MUST
BE MAINTAINED BETWEEN HOT
WATER PIPING AND COMBUSTIBLE
CONSTRUCTION
.
GENERAL PIPING REQUIREMENTS
CAUTION: Improper piping of this boiler/water heater
will void the manufacturer’s warranty and can cause
boiler failure resulting in flooding and extensive
property damage! Excessive water hardness causing
lime build-up in the copper heat exchanger tubes is
NOT
covered under the manufacturer’s warranty.
Excessive pitting and erosion of the internal surface
of the copper heat exchanger tubes is
NOT
covered
under the manufacturer’s warranty if the result
of high water flow rates, see Table 6A and 6B. Return
water temperatures below 110
°
F,
43
°
C
will result
in heat exchanger damage from excessive
condensation voiding the manufacturer’s warranty,
see Primary/Secondary Piping Figure 7.
NOTE: Shut off valves and unions should be
installed at the inlet and outlet connections of the
boiler/hot water heater to provide for isolation of the
unit should servicing be necessary.
Relief Valve
Pipe the discharge of the pressure relief valve to prevent
scalding in the event of a discharge, see Figure 6. The
discharge piping must be sized the same as the
pressure relief valve outlet and installed to allow
complete drainage of both the relief valve and the
discharge piping.
Figure 6
WARNING: Never install any type of valve
between the boiler/water heater and the relief
valve or an explosion causing extensive
property damage, severe personal injury or
death may occur!
Flow Switch
The flow switch supplied with the boiler/water heater
must be wired to the terminal strip in the junction box
to prevent the boiler from firing unless there’s adequate
water flow through the unit. The flow switch must be
installed in the supply piping adjacent to the boiler outlet
connection.
CAUTION: Failure to properly install the flow switch
may result in damage to the boiler/water heater heat
exchanger voiding the warranty!
HEATING SYSTEM PIPING
General Piping Requirements
All heating system piping must be installed by a qualified
technician in accordance with the latest revision of the
ANSI/ASME Boiler and Pressure Vessel Code, Section
IV, and ANSI/ASME CSD-1, Standard for Controls and
Safety Devices for Automatically Fired Boilers. All
applicable local codes and ordinances must also be
followed. A minimum clearance of
1 in
,
25 mm must be
maintained between heating system pipes and all
combustible construction. All heating system piping must
be supported by suitable hangers not the boiler.
The ther mal expansion of the system must be
considered when supporting the system. A minimum
system pressure of
12 psig
,
82.7 kPa must be
maintained.
Heating Boiler Piping Connections
The supply and return connections should be sized to
suit the system, see Table 5.
Table 5 - Supply & Return Pipe Sizing
Model
Supply
Return
8900
2
1
/
2
" NPT
2
1
/
2
" NPT
8800
3" Victaulic
3" Victaulic
*Models 420-950 may have 2
1
/
2
" x 2" reducing fitting
installed.
Pump Requirements
This low mass boiler requires a continuous minimum
water flow for proper operation. The system pump must
be sized to overcome the head loss of the boiler and
the heating system in order to achieve the required
temperature rise. Table 6A and 6B provides the heat
exchanger pressure drop and temperature rise figures.
The temperature rise across the boiler must never
exceed
35
°
F
,
19.4
°
C. The pump delay turns the pump
on each time the burners fire and runs the pump for up
to 10 minutes after the call for heat is satisfied.
CAUTION: A temperature rise outside of the range
listed in Table 6A and 6B indicates that the flow rate
through the heat exchanger is incorrect which will
damage the heat exchanger voiding the warranty!
The maximum allowable flow rate through an 8900
boiler with copper heat exchanger is 92 GPM,
5.8 L/s
and 185 GPM,
11.7 L/s
on single pass.
The maximum allowable flow rate through an 8800
boiler with copper heat exchanger is 185 GPM,
11.7 L/s
and 370 GPM,
23.3 L/s
on single pass.