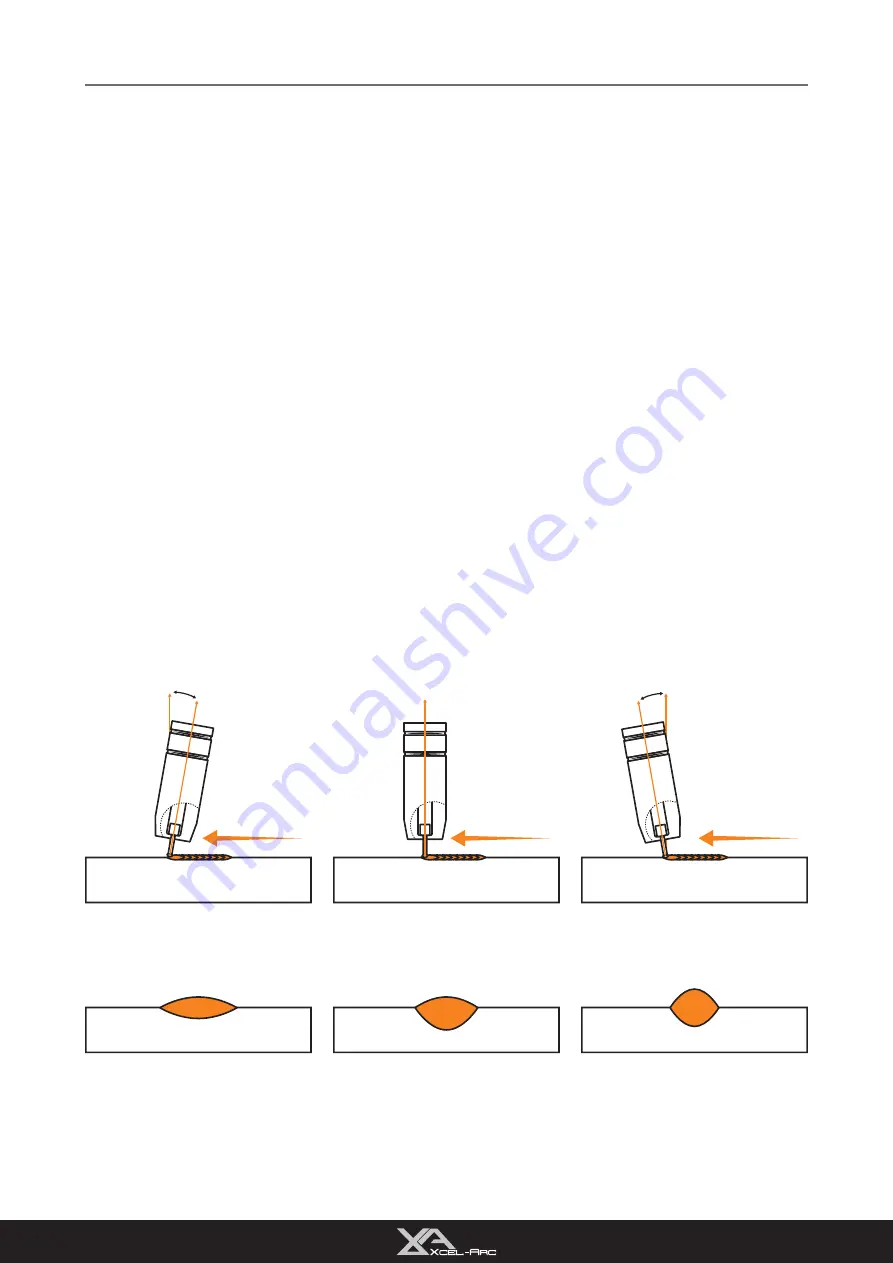
10°
Travel Direction
0°
Travel Direction
10°
Travel Direction
Side View
Side View
Side View
Push Technique
Flat, even weld profile, light penetration.
Narrower weld profile, even penetration.
Narrower and higher weld profile, more
penetration.
Perpendicular Technique
Drag Technique
Basic MIG Welding
Good weld quality and weld profile depend on gun angle, the direction of travel, electrode extension (stick
out), travel speed, the thickness of base metal, wire feed speed (amperage) and arc voltage. To follow are
some basic guides to assist with your setup.
Gun Position - Travel Direction & Work Angle
Gun position or technique usually refers to how the wire is directed at the base metal, the angle and travel
direction chosen. Travel speed and work angle will determine the characteristic of the weld bead profile and
degree of weld penetration.
Push Technique
The wire is located at the leading edge of the weld pool and pushed towards the un-melted work surface. This
technique offers a better view of the weld joint and direction of the wire into the weld joint. Push technique
directs the heat away from the weld puddle, allowing faster travel speeds providing a flatter weld profile with
light penetration - useful for welding thin materials. The welds are wider and flatter, allowing for minimal clean
up / grinding time.
Perpendicular Technique
The wire is fed directly into the weld. This technique is used primarily for automated situations or when
conditions make it necessary. The weld profile is generally higher, and deeper penetration is achieved.
Pull/Drag Technique
The gun and wire are dragged away from the weld bead. The arc and heat are concentrated on the weld pool.
The base metal receives more heat, deeper melting, more penetration and the weld profile is higher with more
buildup.
MIG WELDING GUIDE
32
Содержание Xcel-Arc MULTI 230 AC/DC
Страница 2: ...2 ...
Страница 71: ...NOTES 71 ...