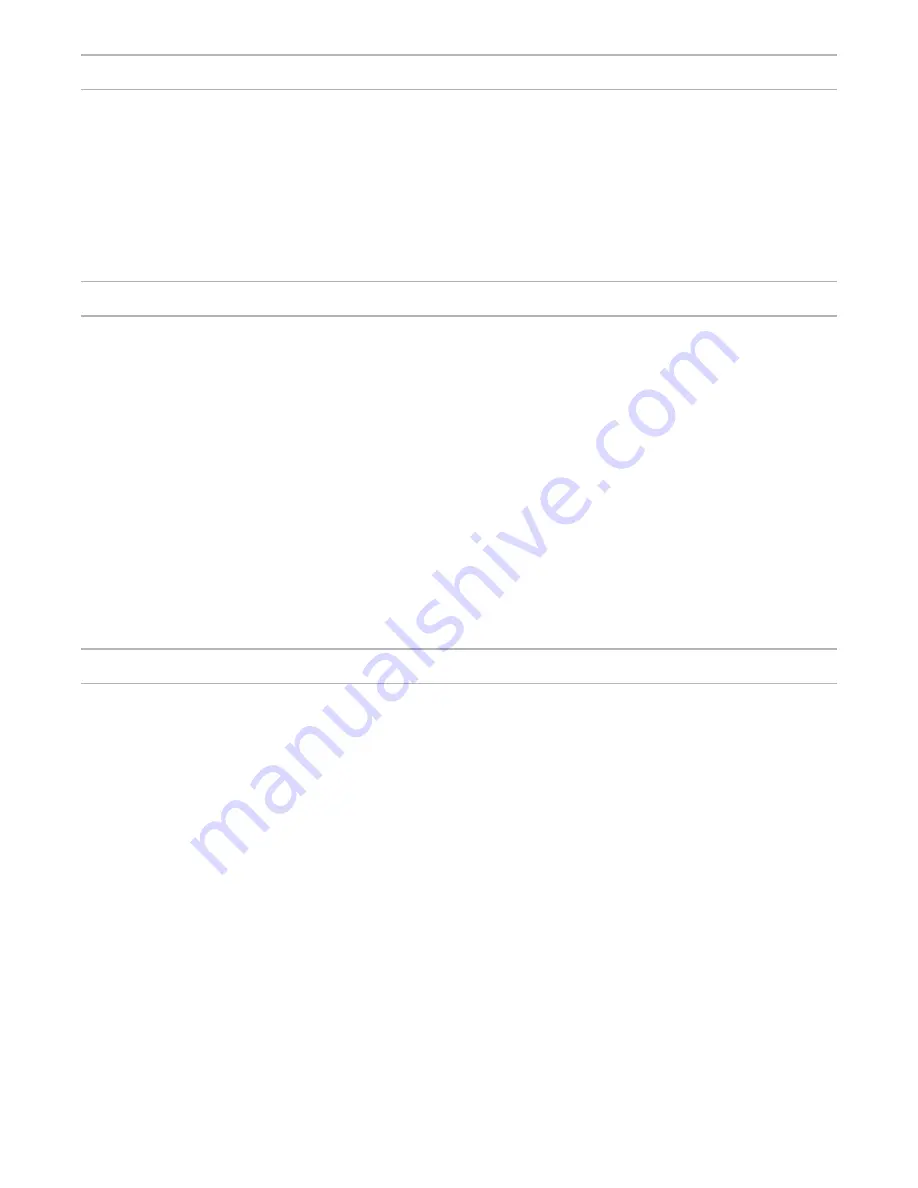
9
Pipe Sizing - continued
For better efficiency and less restriction, use as few fittings (elbows, tees, valves, etc.) as possible.
Suction line diameter must be equal or be greater than the discharge line diameter.
Suction and discharge lines should be independently supported at a point near the pump to avoid strains
being placed on the pump.
NOTE: If more than ten (10) suction fittings are needed, the pipe size must be increased.
Bonding and Grounding
WARNING
:
Ground and bond the pump before connecting to electrical power supply. Failure to ground
and bond the pump can cause serious or fatal electrical shock hazard.
DO NOT
ground to a gas supply
line. To avoid dangerous or fatal electrical shock, turn OFF power to the pump before working on electrical
connections.
1. The motor frame must be grounded to a reliable grounding point using a solid copper conductor, No. 8
AWG or larger. In Canada, No. 6 AWG or larger must be used. If the pump is installed within five (5) feet
of the inside walls of the swimming pool, spa, or hot tub, the motor frame must be bonded to all metal
parts of the swimming pool, spa, or hot tub structure and to all electrical equipment, metal conduit, and
metal piping within five (5) feet of the inside walls of the swimming pool, spa, or hot tub.
2. Bond the motor using the provided external lug.
WARNING:
In order to avoid the risk of property damage, severe personal injury, and/or death, make
sure that the control switch, time clock, or control system is installed in an accessible location, so that in
the event of an equipment failure or loose plumbing fitting, the equipment can be easily turned off.
CAUTION:
The pump must be permanently connected to a dedicated electrical circuit. No other equipment,
lights, appliances, or outlets may be connected to the pump circuit, with the exception of devices that may
be required to operate simultaneously with the pump, such as a chlorinating device or heater.
Plumbing Installation
When installing the pump, care should be taken to see the suction line is below water level to a point
immediately beneath and in front of the pump to ensure quick priming via a flooded suction line. The
height between the pump and water level should not be more than five (5) feet.
If the pump is located below water level, isolation valves must be installed on both sides of the pump to
prevent the back flow of pool water during any routine or required servicing. The PS165VSP - Variable
Speed comes equipped with unions on both the suction and discharge ports. This feature simplifies
installation and service and eliminates the possibility of leaks at the threaded adaptors.
Before starting the pump for the first time, remove the see-through lid. (Turn lid ring counter clockwise
to remove.) Fill strainer tank with water until it is level with the suction inlet. Replace lid, making sure the
o-ring is in place and not damaged. Screw down, hand tight.
Every new installation must be pressure tested according to local codes.
See the Pressure Testing
Section on page 11.