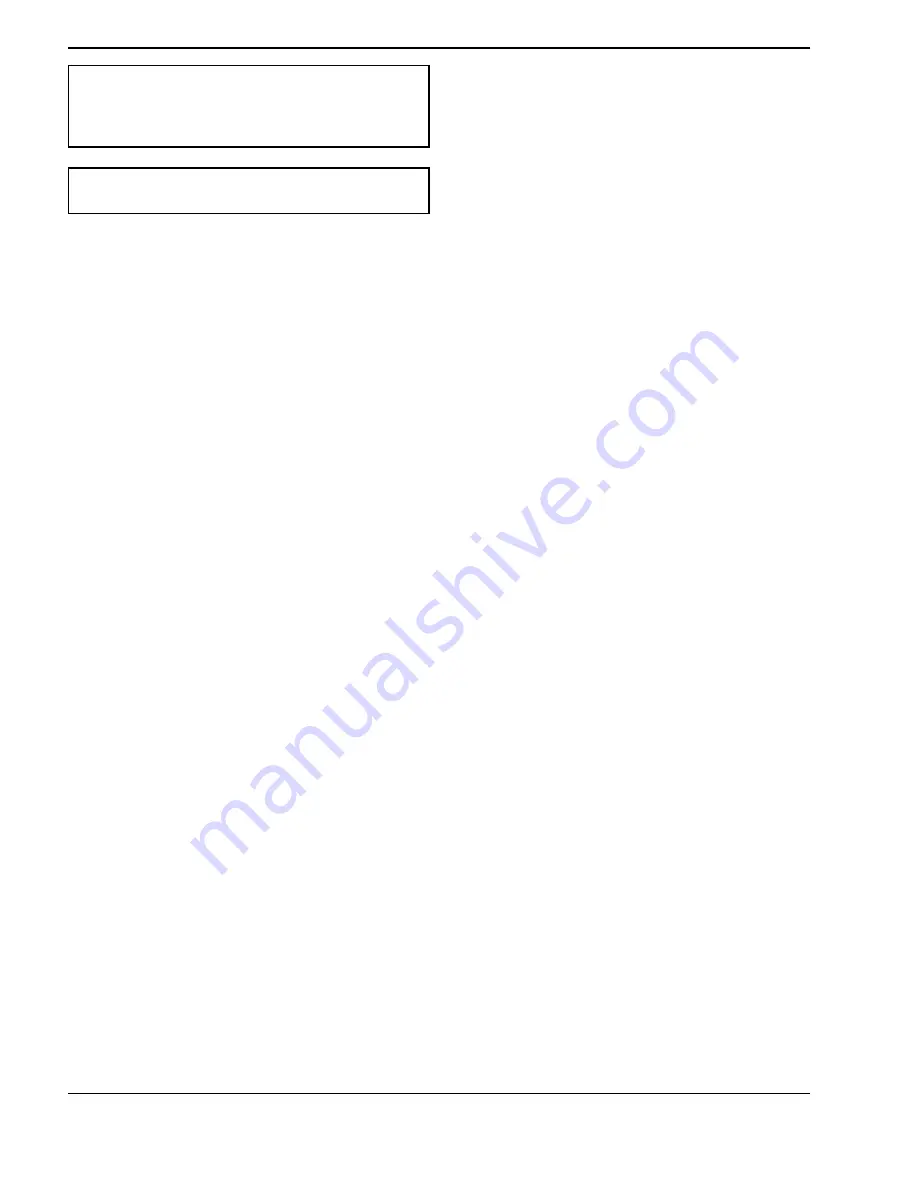
50
Main Burner Adjustment
1. Turn on the unit; about 45 seconds later, the pilot
should light. If the pilot fails to light, repeat pilot
adjustment.
2. Turn the top manual valve on, Location (2). The
inner burner will fire.
3. Make sure that the supply gas manometer reads
between 7 – 14 in. WC (dynamic pressure).
4. Check manifold pressure, Location (2); this should
read to within ± 0.1 in. WC of the values shown in
tables U and V.
5. If adjustment is required, remove screw cap off the
top gas pressure regulator, and adjust regulator.
6. Slowly turn the bottom manual valve on, Location
(3). The outer burner will fire.
7. Make sure that the supply gas manometer reads
between 7 – 14 in. WC (dynamic pressure).
8. Check manifold pressure, Location (3); this should
read to within ± 0.1 in. WC of the values shown in
tables U and V.
9. If adjustment is required, remove screw cap off the
bottom gas pressure regulator, and adjust regula-
tor.
10. The blower pressure should increase about 3/10
in. (0.3 in.) WC equaling the “Firing” value in tables
U and V.
11. Lock the blower shutter by tightening the shutter
nut while holding the black knob fixed.
12. Allow minimum 5 minutes of run time; then attach
flue analyzer, check emission and compare the
CO2 reading to that of table U and V.
13. If CO2 is high, reduce bottom manifold gas pres-
sure.
14. If CO2 is low, increase the bottom manifold gas
pressure.
15. All pressure readings especially manifold pres-
sures should be within ±0.1 in. of listed values.
16. Replace the screw caps back on the gas regula-
tors.
Your ADB is tuned in!
Safety Inspection
·
Check thermostat and high limit settings.
·
Attach thermometers to IN/OUT piping and take
temperature measurement, see Table E and G for
correct flow balance.
·
During the following safety checks leave manome-
ters, and analyzer hooked up, check and record.
·
If other gas fired equipment in the room and on
same gas main, check gas pressures on ADB with
them running.
Remember, supply gas should always be
between 7 in. and 14 in. WC.
·
Check thermostat control for ON/OFF operation;
·
Check safety Hi Limits for ON/OFF operation;
·
While in operation inspect flow switch;
·
Check the low gas pressure switch, it is factory set
at 6 in. WC for natural gas;
·
High gas pressure switch (optional) at 1 in. WC
above manifold pressure;
·
Insert ignition control lockout test as safety check
Follow-up
•
Safety checks must be recorded as performed;
•
Turn unit on;
•
After main burner ignition. Check Manometers for
proper readings;
•
Verify that the blower shutter is locked;
•
Cycle unit several times and recheck readings;
• Re-analyze with unit running record or print
results;
•
Turn unit off, remove all Manometers and replace
blower switch hose, replace all gas pressure caps
and plugs;
•
Check for gas leak one more time;
•
Check around unit for debris and remove com-
bustible and flammable products, i.e. paper,
gasoline etc.
POST START-UP CHECK
Check off steps as completed:
1. Boiler and heat distribution units or storage tank
filled with water?
2. Automatic air vent, if used, open two full turns dur-
ing venting procedure?
3. Air purged from system?
4. Air purged from gas piping? Piping checked for
leaks?
5. Followed start-up procedure for proper start-up?
6. Is burner flame visible?
7. Test safety controls: If boiler is equipped with a low
water cutoff or additional safety controls, test for
operation as outlined by manufacturer. Burner
should be operating and should go off when con-
trols are tested. When safety devices are restored,
NOTE:
Emissions will vary with different
applications (hydronic, water heater, or pool),
venting (including direct vent), ambient conditions (T,
P, and humidity), and the condition of the boiler.
NOTE:
For high altitude (above 5000 ft), call the
factory for proper pressure settings.
Содержание 751
Страница 2: ...2...
Страница 6: ...6 Component Locations Fig 1 Component Locations...
Страница 14: ...14 Fig 4 Single Boiler Primary Secondary Piping Fig 5 Single Boiler Primary Secondary Piping with CHX...
Страница 15: ...15 Fig 6 Dual Boiler Piping Fig 7 Dual Boiler Piping with CHX...
Страница 20: ...20 Fig 13 Single Boiler Pool Application Fig 14 Single Boiler Pool Application with CHX...
Страница 44: ...44 Figure L 2 WIRING DIAGRAM WIRING DIAGRAM...