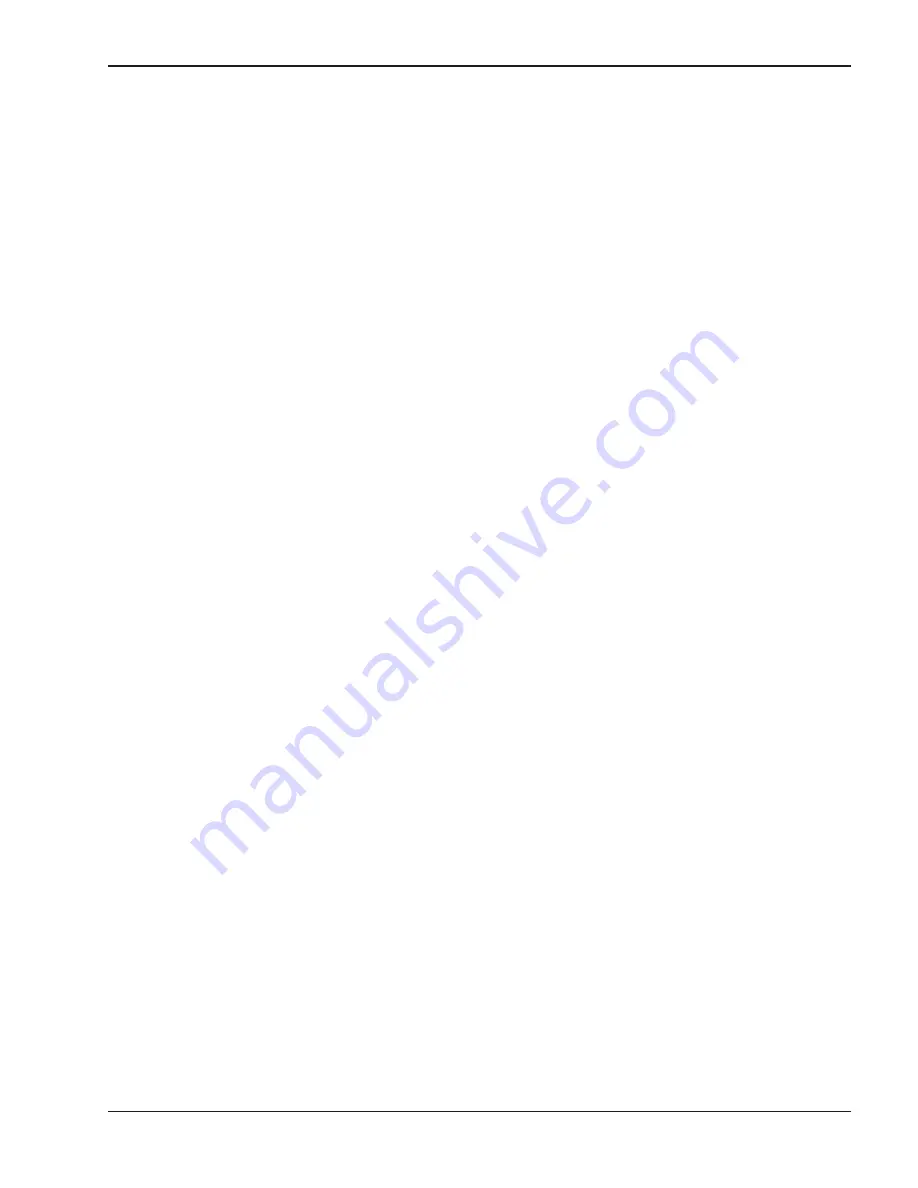
Safety Inspection
1.
Check all thermostats and high limit settings.
2.
During the following safety checks leave manome-
ters hooked up, check and record.
3.
If other gas-fired appliances in the room are on the
same gas main, check all pressures on the Delta
Limited with all other equipment running.
4.
Check thermostats for ON-OFF operation.
5.
Check high limits for ON-OFF operation.
6.
While in operation, check flow switch operation.
7.
Check the low gas pressure switch. (For proper
adjustment, use the attached manometers, if
available, to set pressure. The scales on the
switch are approximate only.) Low gas pressure
switch must be set at 5.0 in. WC for natural gas
and 10.0 in. WC for propane gas.
8.
Make sure that the high gas pressure switch (op-
tional) is set to 1.0 in. WC above manifold
pressure.
Follow-Up
Safety checks must be recorded as performed.
Turn heater on. After main burner ignition:
1.
Check manometer for proper reading.
2.
Cycle heater several times and re-check readings.
3.
Remove all manometers and replace caps and
screws.
4.
Replace all gas pressure caps.
5.
Check for gas leaks one more time.
Pilot Turn-Down Test
The Delta Limited heaters, depending on their size,
have two to five burner sections. Each burner section
is supplied gas by two gas valves incorporated into a
single valve body. A maximum of three burner sections
may be controlled by a single hot surface ignition sys-
tem. The middle of the three burner sections is ignited
directly with a hot surface ignition system.
The burner section that is ignited directly by the hot
surface ignition system serves as a supervised pilot to
light the burner sections on either side of it. The burn-
er sections on either side of the supervised section
(pilot) are electrically interlocked with the supervised
ignition system so as they are not energized unless
flame is proven on the center section which is acting
as a pilot to light the right and left-hand sections.
The pilot turn-down test is conducted as follows:
1.
Turn off manual valves on non-supervised burner
sections.
2.
Turn on electrical power and adjust thermostat to
call for heat.
3.
Wait for completion of ignition sequence to light
burner section being utilized as a pilot for those
turned off in step 1 above.
4.
Gradually reduce manifold pressure (flame) on
supervised burner section by slowly closing man-
ual gas valve. Watch for shut-down due to loss of
supervised flame signal as pressure is being re-
duced. Flame signal should be lost before
manifold pressure goes below 2.0 in. WC for nat-
ural gas and 6.0 in. WC for propane gas.
Leak Test Procedure: Dual-Seat Gas
Valves
Proper leak testing requires three pressure test points
in the gas train.
Test point A is upstream of the automatic gas valve. On
the first automatic valve, this is a bleedle valve. On the
other valves, this is a plugged port. The bleedle valve
on the first valve may be used for all the other valves
as well.
Test point B is a bleedle valve located between the two
automatic gas valve seats.
Test point C is located downstream of both automatic
gas valve seats and upstream of the manual valve. On
the manual valve, this is a bleedle valve. Identical
readings will be found at the plugged port labeled as
Alternate C.
Refer to Fig. 36. The numbers on the diagram refer to
the steps below:
These tests are to be conducted with the electrical
power to the heater turned off.
43
Содержание 399B-2339B
Страница 23: ...23 Fig 20 2 Stage Wiring Connections Fig 21 3 Stage Wiring Connections Fig 22 4 Stage Wiring Connection...
Страница 39: ...Wiring Diagram Models 399B 1259B 39...
Страница 40: ...Wiring Diagram Models 1529B 2339B 40...
Страница 52: ...www raypak com Raypak Inc 2151 Eastman Avenue Oxnard CA 93030 805 278 5300 Fax 805 278 5468 Litho in U S A...