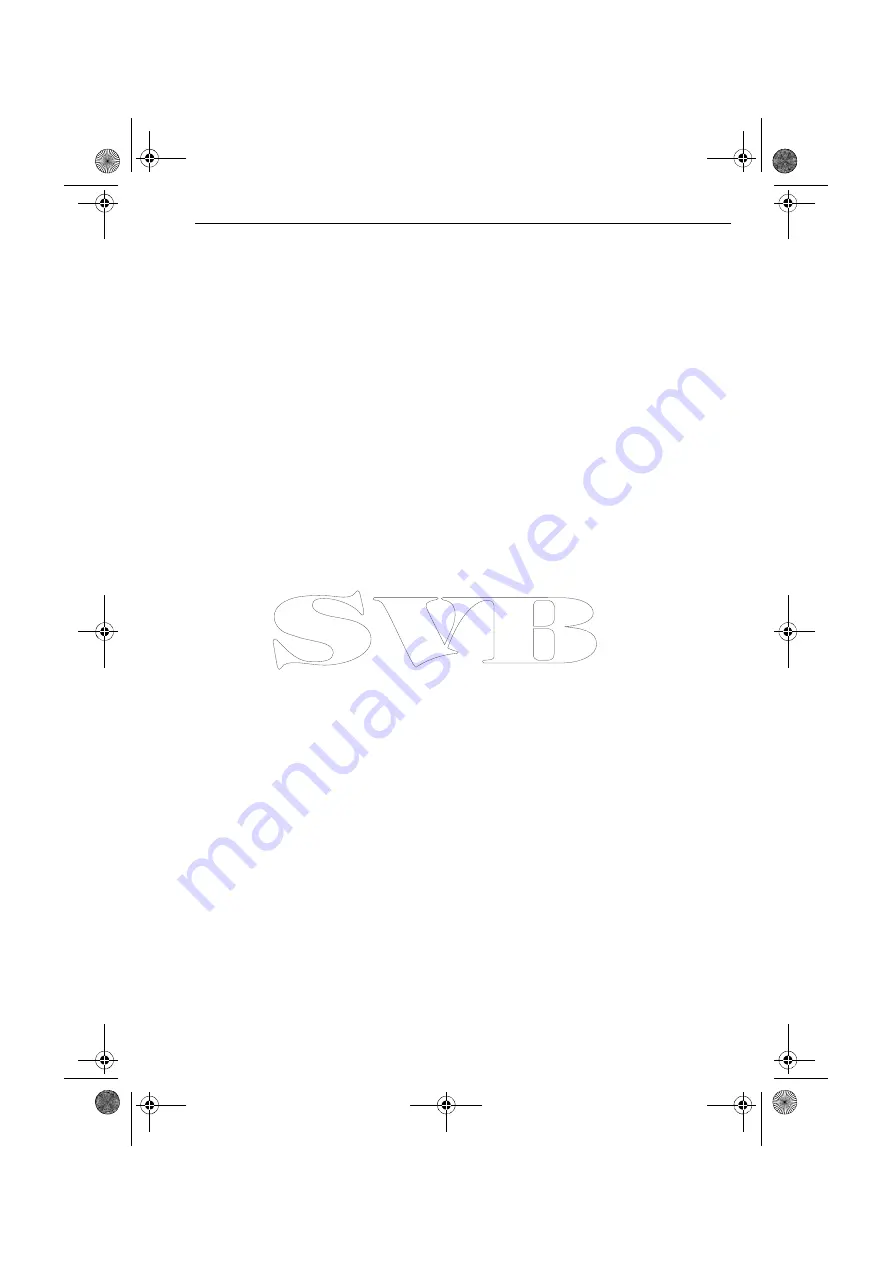
31
Chapter 3: Commissioning & setup
This chapter describes the commissioning and setup procedures for your Raymarine
SPX-5 Wheel system.
Requirement
The commissioning procedures are mandatory and must be carried out after
installation, before the SPX-5 Wheel system is used to steer the boat.
Additional setup procedures are also provided for you to fine tune your SPX-5 Wheel
system for optimum performance with your boat. They are not mandatory and you
may find that you do not need to use them if the SPX-5 Wheel system operates to your
satisfaction after commissioning.
When commissioning and setting up the SPX-5 Wheel system, use the supplied
ST6002 controller (Pilot Controller):
•
standby
&
auto
select the required operating mode.
•
+1, -1, +10 & -10
initiate course changes.
•
disp
&
track
provide access to extended functions.
Note:
The system is also compatible with ST7002, ST8002 and ST70 Pilot Controllers
3.1 Commissioning
The commissioning process comprises:
•
Dockside checks & setup.
•
Seatrial calibration.
Dockside checks & setup
The dockside checks comprise:
1. Switching on.
2. Checking SeaTalk and NMEA 0183 connections.
3. Checking autopilot steering sense.
4. Setting vessel type and drive type
5. Setting rudder limits, if rudder reference option fitted.
With the boat safely tied up, carry out the dockside checks and setup procedures
before any trials at sea or other setup procedures.
Switching on
1. Observing the Wheel drive unit, switch on the main power breaker. If the Wheel
drive moves, switch off the power immediately, then ensure the system wiring is
correct.
2. When the Pilot Controller and Course Computer are powered up, the controller
will beep and show the controller type for a few seconds, before showing the
STANDBY screen.
A CALIBRATE REQUIRED message may be displayed. This indicates that the
autopilot commissioning is not yet complete.
3. Check that the STANDBY screen displays a live compass heading.
87074_2.book Page 31 Wednesday, November 21, 2007 3:55 PM
Содержание SPX-5
Страница 14: ...6 SmartPilot X 5 Wheel Installation Setup Guide 87074_2 book Page 6 Wednesday November 21 2007 3 55 PM...
Страница 66: ...58 SmartPilot X 5 Wheel Installation Setup Guide 87074_2 book Page 58 Wednesday November 21 2007 3 55 PM...
Страница 68: ...60 SmartPilot X 5 Wheel Installation Setup Guide 87074_2 book Page 60 Wednesday November 21 2007 3 55 PM...
Страница 72: ...64 SmartPilot X 5 Wheel Installation Setup Guide 87074_2 book Page 64 Wednesday November 21 2007 3 55 PM...
Страница 76: ...87074_2 book Page 68 Wednesday November 21 2007 3 55 PM...