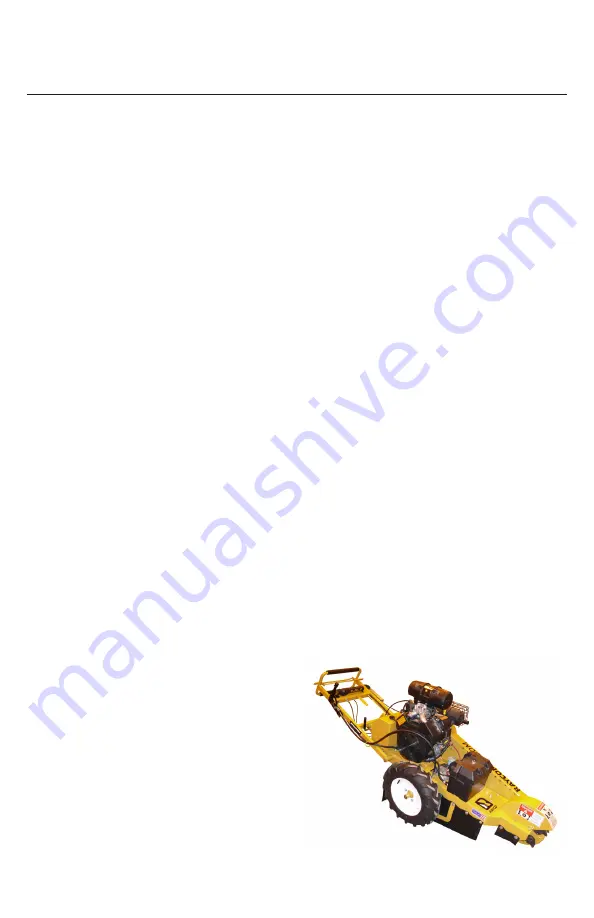
RG25DH Operation • Service • Maintenance • Parts Manual
800.392.2686
5
Foreword
Certified Engine Maintenance
Proper maintenance and repair is essential to keep the engine
and machine systems operating correctly. As the heavy duty
off-road engine owner, you are responsible for the required
maintenance listed in the Engine Owner Manual & Machine
Operator, Maintenance & Service Manual.
Attach a “Do Not Operate” warning tag or a similar warning
tag to the start switch or to the controls before you service
the equipment or before you repair the equipment.
Know the width of your equipment in order to maintain proper
clearance with you operate the equipment near fences or
near boundary obstacles.
Be aware of high voltage power lines and power cables
that are buried. If the machine comes in contact with these
hazards, serious injury or death may occur from electrocution.
Wear a hard hat, protective glasses, and other protective
equipment, as required.
Do not wear loose clothing or jewelry that can snag on
controls or on other parts of the equipment.
Make sure that all protective guards and all covers are secured
in place on the equipment.
Keep the equipment free from foreign material. Remove
debris, oil, tools, and other items from the deck, from walkways,
and from steps.
Secure all loose items such as lunch boxes, tools, and other
items that are not a part of the equipment.
Know the appropriate work site hand signals and the personnel
that are authorized to give the hand signals. Accept hand
signals from one person only.
Do not smoke when you service an air conditioner if equipped.
Also, do not smoke if refrigerant gas may be present. Inhaling
the fumes that are released from a flame that contact air
conditioner refrigerant can cause bodily harm or death.
Inhaling gas from air conditioner refrigerant through a lighted
cigarette can cause bodily harm or death.
Never put maintenance fluids into glass containers. Drain
all liquids into a suitable container.
Obey all local regulations for the disposal of liquids.
Use all cleaning solutions with care. Report all necessary
repairs.
Do not allow unauthorized personnel on the equipment.
Unless you are instructed otherwise, perform maintenance
with the equipment in the servicing position. Refer to
Operation and Maintenance Manual for the procedure for
placing the equipment in the servicing position.
If machine requires maintenance above ground level, use
appropriate devices such as ladders or man lift machines.
If equipped, use the machine anchorage points and use
approved fall arrest harnesses and lanyards.
Machine Description
Design
The RG 25HD STUMP CUTTER is designed for your
maximum benefit per dollar spent. The machine is constructed
for durability and easy maneuvering, for those hard to reach
tree stumps and roots. Its 14” diameter x 3/8” thick cutting
wheel with 12 replaceable carbide-tipped teeth is powerfully
driven by a Kohler 25 horsepower engine. The operator
benefits from a steel cutting wheel guard and full protection
from heavy rubber curtains below the chassis.
Other special features of the RG 25HD STUMP CUTTER
include: self propelled drive via a hydrostatic transmission,
an operator’s presence system, adjustable handlebar
positioning, steel guards surrounding moving parts, and
convenient access for tightening the V - belt.
How it works
The machine removes tree stumps by the repeated gradual
sweeping of a multi-toothed high-speed rotating cutting
wheel. The cutting wheel has teeth on its side, in a strategic
pattern. The rotating cutting wheel takes a sweep from one
side of the stump to the other, each tooth rapidly tearing and
stripping away small pieces of stump. After each sweep of 1
to 2 inches of depth, the cutting wheel is advanced deeper
into the stump, and the procedure is continuously repeated,
under the precise control of the operator, until the stump is
satisfactorily removed.
Содержание RG25HD
Страница 48: ...RG25DH Operation Service Maintenance Parts Manual 48 Troubleshooting ...
Страница 49: ...RG25DH Operation Service Maintenance Parts Manual 800 392 2686 49 Troubleshooting ...
Страница 50: ...RG25DH Operation Service Maintenance Parts Manual 50 Troubleshooting ...
Страница 51: ...RG25DH Operation Service Maintenance Parts Manual 800 392 2686 51 Troubleshooting ...
Страница 52: ...RG25DH Operation Service Maintenance Parts Manual 52 Troubleshooting ...
Страница 53: ...RG25DH Operation Service Maintenance Parts Manual 800 392 2686 53 Troubleshooting ...
Страница 54: ...RG25DH Operation Service Maintenance Parts Manual 54 Troubleshooting ...
Страница 55: ...RG25DH Operation Service Maintenance Parts Manual 800 392 2686 55 Troubleshooting ...
Страница 56: ...RG25DH Operation Service Maintenance Parts Manual 56 Troubleshooting ...
Страница 57: ...RG25DH Operation Service Maintenance Parts Manual 800 392 2686 57 Troubleshooting ...
Страница 59: ...RG25DH Operation Service Maintenance Parts Manual 800 392 2686 59 RG25HD Full Assembly Rev 3 8 ...
Страница 66: ...RG25DH Operation Service Maintenance Parts Manual 66 Hydraulic Drive Assembly ...