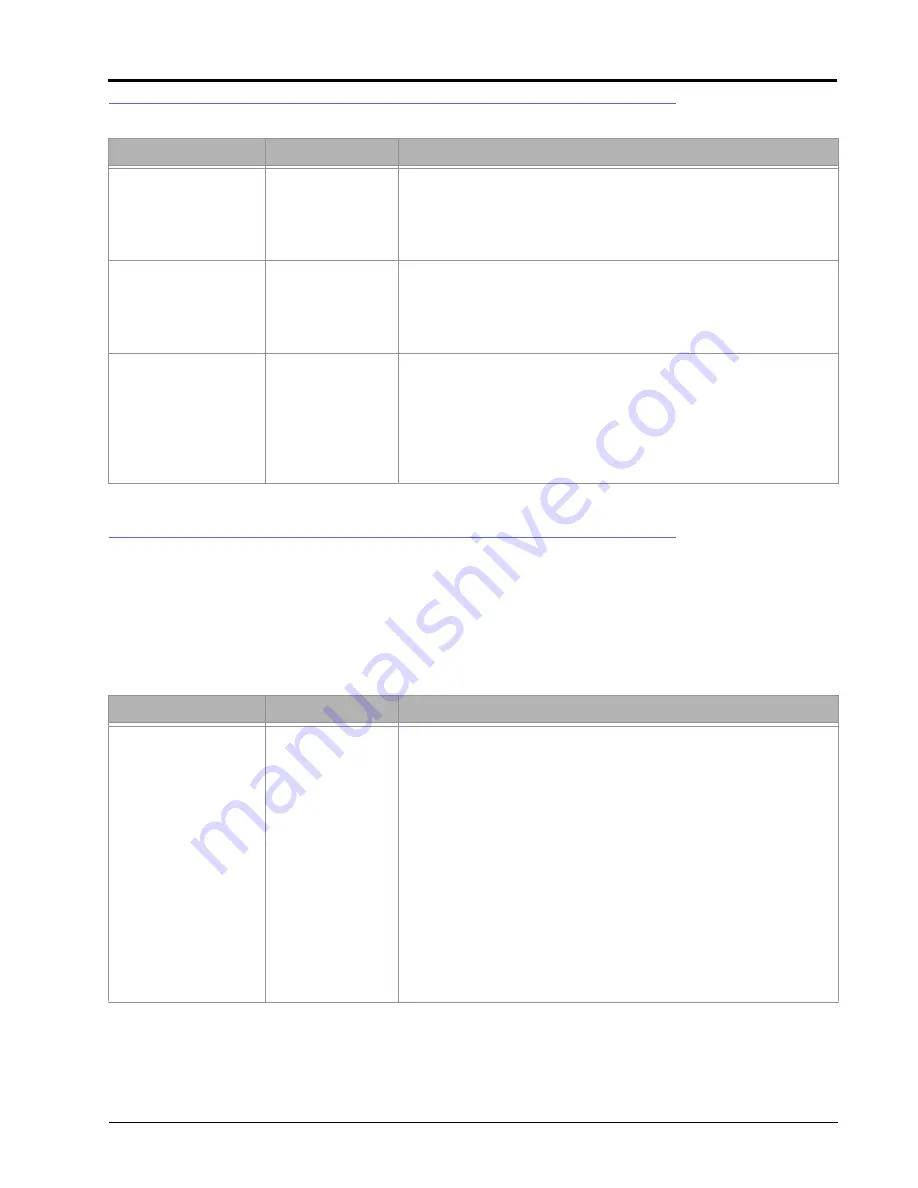
:
23
COVERAGE MAP ISSUES
CAN TROUBLESHOOTING
Although the control algorithm is located within the CAN node, all of the same troubleshooting techniques used
in a traditional hard-wired system still apply to a CAN system. CAN allows for modularization of the control
system, but the behavior of the system remains the same. Flow and speed sensors, as well as the control valve and
boom valves, are used in the same manner.
The following issues are some common causes for communication failures:
Issue
Possible Cause
Solution
Gaps displayed in
coverage map
Section widths not
configured correctly Check boom widths and boom center values
Guidance and
section widths not
the same
Set the guidance width and overall section widths to the same value.
Product coverage
displayed in zero rate
zones.
Vibration chatter in
encoder.
Make sure that the encoder is firmly mounted. Increase value in
“Zero Rate Tolerance.”
Valve or motor is
not set to close
completely
Adjust valve or motor to close or stop completely with no rate
applied.
Cannot achieve target
rate
Driving too fast for
vehicle
Speed may exceed capabilities of vehicle to deliver product. Slow
the vehicle down during application or configure product control
hardware to supply a higher amount of product.
Calibration
numbers incorrect
Check and adjust meter calibration, density, and other calibration
values.
Speed calibration
incorrect
Check and adjust speed calibration setting.
Issue
Possible Cause
Solution
Console or CANbus
cannot read the Switch
Pro nodes
Switch Pro is not
properly connected
Check Switch Pro auxiliary power connection.
Check the CANbus connection to the Switch Pro and re-initialize the
console to read the Switch Pro nodes.
No Power to Switch
Pro
Ensure console is powered on.
Check console power and ground lead connections. Refer to the
console’s Installation & Operation Manual for further console power
troubleshooting.
Weak or dirty
power to the CAN
nodes
Verify at least +10V DC is present on the auxiliary power output
connector.
Corrosion in CAN
connections
Disconnect and clean the CAN connections.
Check the CAN terminators.
CANbus not
terminated properly
Make sure that both ends of the CANbus systems are properly
terminated.
Содержание Switch Pro
Страница 17: ...13 FIGURE 2 Viper Pro with Switch Pro for SCS 440 450 Cabled Systems...
Страница 19: ...15 FIGURE 4 Viper Pro with Switch Pro for SCS 4400 Cabled Systems...
Страница 21: ...17 FIGURE 6 Viper Pro with Switch Pro Combo Cable for SCS 440 450 Cabled Systems...
Страница 23: ...19 FIGURE 8 Viper Pro with Switch Pro Combo Cable for SCS 4400 Cabled Systems...
Страница 24: ...APPENDIX B 20 Raven Switch Pro Installation Reference Manual...
Страница 28: ...APPENDIX C 24 Raven Switch Pro Installation Reference Manual...
Страница 30: ...Index 22 Raven Switch Pro Installation Reference Manual...