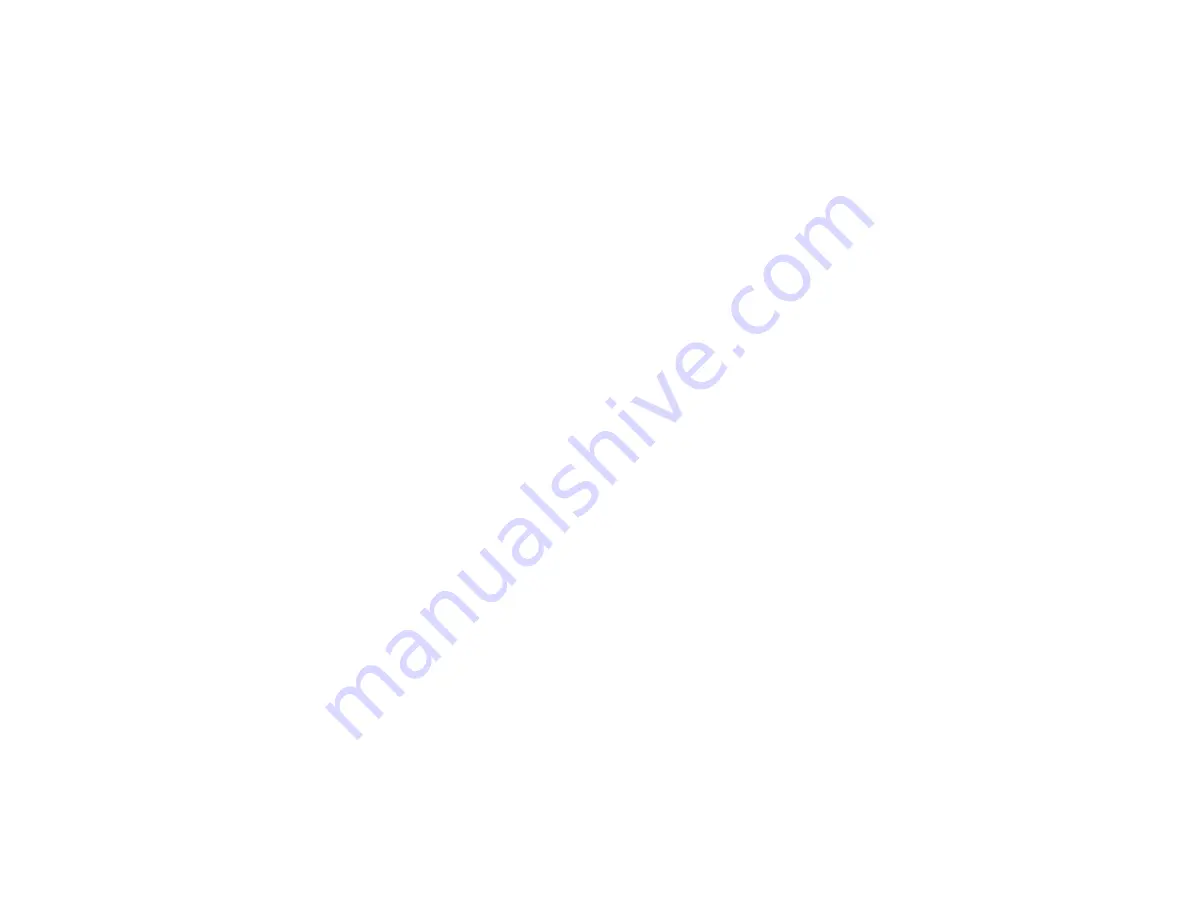
o
Elevator system integrity:
o
push pull tube for mechanical integrity,
o
push pull tube end effectors for
bolt dammage and tightness and for wear or dammage,
o
control stops for wear and rivet integrity,
o
push-pull
rod for binding and lubrication and wear,
o
elevator frames for dammage or wear,
o
elevator hinges and bolt
for wear and cotter pins,
o
elevator control horns for mechanical integrity,
o
elevator split push-pull tube end
effector for cracks and bolt safety rings,
o
control stick for tightness to fuselage cage,
o
control stick mecha-
nism for cracks or other signs of dammage or wear.
o
Aileron system integrity:
o
cables for tension,
o
cables for fraying or wear,
o
cable thimbles for wear,
o
pulleys and pulley cages for wear and mechanical condition,
o
control tee for signs of dammage or wear,
o
turnbuckles for safety wire and tightness,
o
turnbuckle attach points (cables and tee side) for wear,
o
aile-
ron push-pull tubes for end effector condition or cracks and condition of main bolt and safety ring,
o
aileron
servo horns for signs of dammage or wear,
o
aileron rods for wear and end effector condition,
o
aileron frame
for mechanical condition,
o
aileron fabric for condition,
o
aileron control horn for dammage or wear,
o
ball
joint end effectors for binding,
o
aileron hinges and bolt for wear and cotter pins,
o
freedom of movement
throughout operational range of control stick,
o
limit of control movement,
o
aileron rod exit fairings for wear
and integrity,
o
control stops for proper operation,
o
control stick safety wire “bushing” for proper operation,
o
dual controls stick connector for wear.
o
Rudder system integrity:
o
cables for tension,
o
cables for fraying or wear,
o
cable thimbles for wear,
o
pulleys and pulley cages for wear and mechanical condition,
o
plastic cable bushings for wear and operation,
o
rudder pedals for wear or dammage,
o
pedal mounting system for mechanical dammage or wear or binding,
o
pedal bolts for tightness,
o
cockpit floor for signs of dammage from excessive brake system application,
o
pushrod connections to nose gear for tightness and wear and mechanical integrity,
o
control stops for proper
funciton,
o
freedom of movement throughout envelope of rudder movement,
o
binding of rudder with elevator,
o
rudder frame for mechanical condition dammage and wear,
o
rudder hinges and bolts for wear and cotter
pins,
o
rudder horns for dammage or wear,
o
rudder lacing cap for secure fit,
o
rudder fabric for condition,
o
cable end effectors for tightness and cotter pins,
o
rudder trim tube secure.
o
Empennage structure integrity:
o
horizontal stabilizer frames for mechanical condition,
o
vertical stabi-
lizer frame for mechanical condition,
o
fabric for condition,
o
fabric lacing for condition and tension,
o
v.stab
and h.stab attachment hinges and bolts for condition and cotter pins,
o
vertical stab mount for cracks and other
signs of fatigue,
o
vertical stab mount rivets for condition,
o
tail boom extension for cracks or dammage,
o
boom extension hardware for condition and wear,
o
guy cables for fraying and tension,
o
guy cable ends for
secure attachment and thimble condition,
o
guy cable attachment points for lock rings.
o
Tail boom structure integrity:
o
tail boom tube for cracks or any other sign of deformation,
o
tail boom
tube for fatigue at any point where it is attached to the frame or something is mounted to it,
o
sight down inside
of tail boom with a light at the lower end for back lighting,
o
systems inside boom for interference or signs of
dammage,
o
tail boom collar and collar bolts for cracks or deformation,
o
tail boom attach points to fuselage
cage for signs of dammage and mechanical condition,
o
flow fence structure for clues indicating tail boom
flexure (i.e. popped rivets).
o
Cockpit systems integrity:
o
pre-flight and standard procedures checklists onboard,
o
fire extinguisher
mount secure,
o
fire extinguisher ready for use,
o
intercom system wiring for routing conflicts or chaffing,
o
intercom secure to fuselage keel,
o
intercom jack box mount for mechanical condition,
o
airworthiness and
registration and pilots operating handbook with current weight and balance is on board the aircraft,
o
instru-
ment panel for structural integrity,
o
pitot and static tubes for cleanliness and line routing conflicts or chafing,
o
pitot and static system operating correctly (annual inspection only),
o
compass mount for structural integrity,
o
seats for mechanical condition and condition of fabric and tension straps,
o
hour meter operational,
o
fuel
quantity/spins/experimental instrument arcs and other placards properly installed and in good visual condition,
o
intercom operational,
o
seat belt mounting structures and belts,
o
floor board for cracks or dammage and
floorboard wear plate for condition.
o
Cockpit cage integrity:
o
for cracks or deformation of any weld or part of the structure,
o
for elongation of
bolt holes,
o
for flecked paint indicative of cracks,
o
for overall “squareness” and indications of dammage that
is only visible in the big picture,
o
for loose fasteners,
o
for dammaged tabs or mounts welded to the cage.
o
Fuselage cabanes and keel integrity:
o
for dents or deep scars that would affect the structural strength
of these components,
o
for flecked paint or other signs of deformation,
o
for elongated fastener holes,
o
for
components loosely mounted to the keel,
o
for loose fasteners.
o
Motor mount integrity:
o
torque the motor mount bolts (into the engine block),
o
check the tightness of
the engine bolts thru the barry mounts,
o
inspect each component of the barry mount system for any sign of
dammage such as cracks or deformation,
o
lateral stabilizer supports secure and in good condition.
o
Wing mount system integrity:
o
hinge blocks and keel standoff and all hardware for cracks or loose fas-
teners or signs of fatigue or dammage,
o
keel mount point free of elongation,
o
struts for nicks or deformation
especially cracking along the length of the extrusion and near the end,
o
strut blocks for signs of overstress such
as cracks or deformation,
o
strut fairing for security,
o
jury struts for signs of vibrational wear,
o
jury strut pin
safety wire and cotter pins,
o
jury strut pins and sockets for wear,
o
lower strut attachment point to fuselage
for cracks or deformation,
o
lower strut pin for lock ring and wear,
o
threaded strut blocks and threaded rod
ends for signs of thread dammage.
o
Wing structure integrity:
o
internal wing structure for any sign of dammage,
o
for loose fasteners,
o
for
signs of vibration wear or fatigue or over stress,
o
fuel tank mount system for loose rivets or other dammage,
o
wing fabric for condition,
o
fabric ribs for secure ends,
o
wing structure for signs of buckling with applied
load (push up and down rather hard on the wing).
o
Fuselage superstructure integrity:
o
lexan and sheetmetal for missing or loose rivets,
o
lexan for exces-
sive scratching,
o
lexan and sheetmetal for buckling which would indicate other problems with the airframe,
o
door mechanisms for operation,
o
door hardware for function,
o
center cover sheetmetal and mount system
for mechanical integrity,
o
door seals and other seals for signs of aging,
o
lexan for signs of aging.
o
Aircraft ground operations and flight test: obtain a pilot for the ground and flight test who has not been in
the aircraft for the majority of its last 100 hours of service. This pilot will provide an objective and non-emo-
tional evaluation of the aircraft including a
o
basic pre-flight inspection,
o
ground run-up of the engine (check
throttle synchronization and tachometer calibration,
o
verify operation of charging system,
o
in-flight perfor-
mance checks,
o
and any other basic check of flight maneuverability,
o
trailing position of controls in flight.
o
Airframe and Engine logbook entries: Upon completion of the inspection, make the appropriate entries in
the airframe and engine logbooks to reflect the results of the inspection. This must include the endorsement
of the designated repairman or an A&P mechanic as required by the Phase II Operating Limitations Part 10 as
issued by the FAA for 6167U. Information such as what corrective action was taken or needs to be taken,
suggestions to new maintenance intervals and records of the performance of the engine and airframe in flight
should all be included in the entries.
End of Condition Inspection Checklist
PAGE 20
Содержание S-12
Страница 33: ...PAGE 33...
Страница 34: ...PAGE 34...