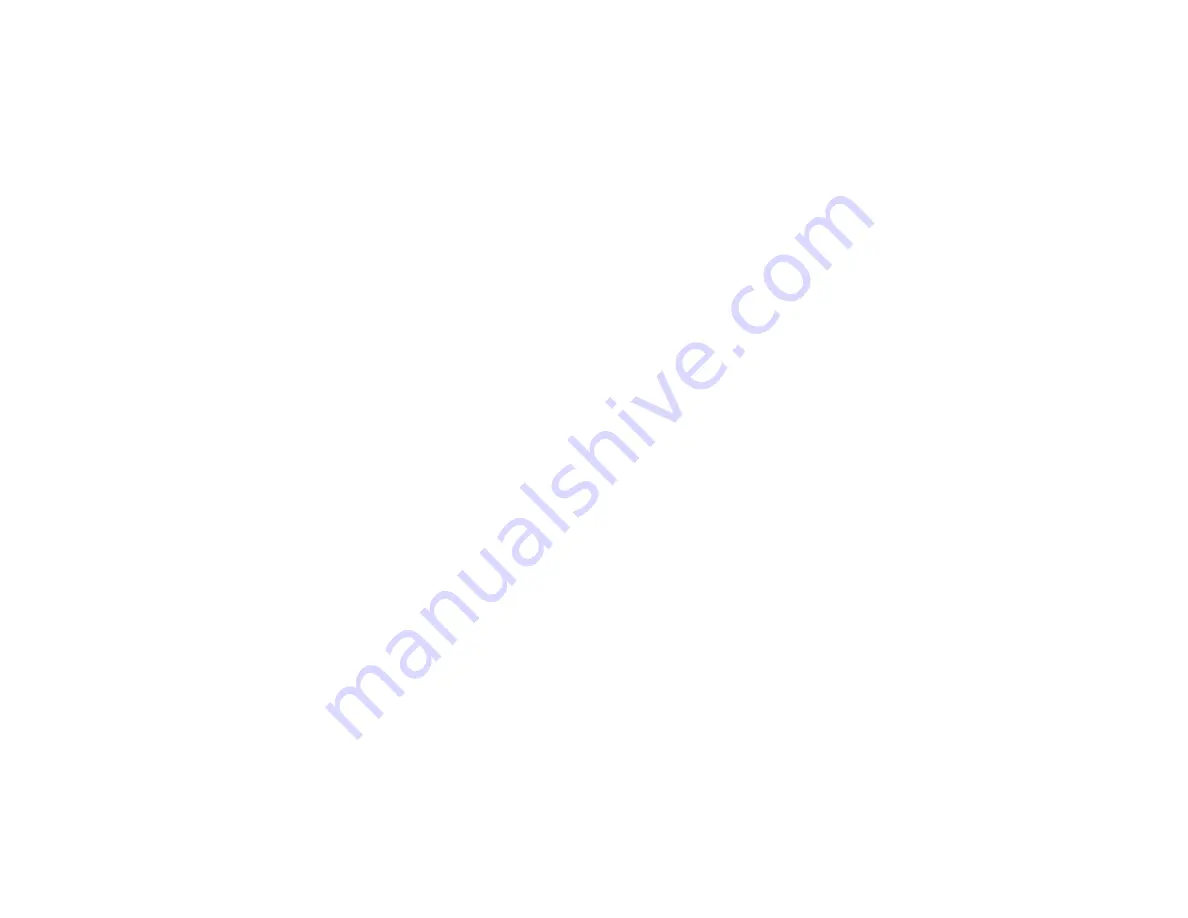
Appendix D - Condition Inspection Checklist
Rev 3 (Mar/12/99)
This checklist is written as a “semi-comprehensive” of things to look for. Many inspection points critical to safety are
implicit to the skill level required for this type of inspection process. Expect to spend at least 12 hours with this procedure,
more if complications arise. Refer to Rotax Owner’s Manual for complete engine maintenance procedures at 100 hour,
annual and other intervals. FAR Title 14 Chapter 43 Appendix D should add additional scope and understanding to all
checklist procedures below.
REVIEW OF THE PROCESS
Inspection must be carried out or closely supervised by the designated repairman or an A&P mechanic with
Authorization Inspection authority (AI). The flight test should preferably be conducted by a qualified pilot
who is very familiar with the S-12 but who has not been the airplane for the majority of its pre-inspection
flight hours. A pilot can spend months in a plane with problems that slowly get worse and worse and this
pilot will never perceive the problem because of the graduality with which it occurs. Also, a pilot who is a
third party to the aircraft will provide an objective and unbiased review of the performance of the airplane.
TTAE:
Date:
Completed By:
CHECK SMALL BOXES WHEN COMPLETED, INITIAL LARGE BOXES
o
Cleaning of aircraft:
o
wash the fabric and metal surfaces of the aircraft with soap and water,
o
use an air
blower to quickly remove moisture from all metal components,
o
clean the lexan using an appropriate plastic
cleaner and polish (Maguire’s or equivalent).
o
Paperwork review:
o
identify previously unresolved issues in the airframe and engine logbooks,
o
review
the status of life limited components and recurring airworthiness directives,
o
research any new or previously
skipped airworthiness directives for the airframe, powerplant or propellor,
o
include a copy of any and all
background information research papers with a copy of the condition inspection checklist.
o
Propellor system integrity:
o
torque prop hub bolts to proper specification,
o
inspect blades for nicks,
cracks and cleanliness,
o
hub for proper seating and cracks or signs of dammage,
o
gear backlash and axial
backlash,
o
check blade pitch settings and blade track.
o
Exhaust system integrity:
o
header and muffler for cracks,
o
remove and inspect springs and hoops for
wear,
o
inspect condition of silicone bead,
o
tighten header nuts to prevent harmonic vibration of header tubes,
o
rewire springs and apply anti-seize to ball-joints.
o
Ignition system integrity:
o
clean spark plugs,
o
spark plugs torqued properly and in good condition,
o
spark plug wires tight,
o
ignition ground wires,
o
stator area free of debris,
o
other ignition wiring compo-
nents,
o
lines routed without interference and free of chafing.
o
Fuel system integrity:
o
all lines for cracks especially cracks in black line where hose clamps are used,
o
all connections for tightness,
o
all lines for chafing and routing interference,
o
operation of sump drain,
o
cleanliness and age of fuel filter,
o
appearance of fuel tank interior (debris, discoloration etc.),
o
discolor-
ation of blue lines or oxidation of black lines,
o
chafing protection on blue lines,
o
fuel cap gasket and vent
tube clear and secure, suppleness of lines,
o
routing of sump drain line.
o
Coolant system integrity:
o
coolant level and mixture to -34F,
o
lines routed without interference and
free of chaffing,
o
connections for tightness,
o
hoses for cracks or signs of aging,
o
suppleness of lines,
o
radiator free of debris and dammage,
o
radiator mount secure and free of cracks or dammage,
o
cap gasket
quality,
o
routing of coolant overflow line,
o
coolant overflow tank for secure mounting,
o
temp/pressure
lines secure.
o
Carburetion System:
o
clean and re-oil air filters,
o
air filters properly safety wired,
o
return springs on
throttle and choke for wear and condition,
o
fuel overflow and vent lines routed properly,
o
carburetor structure
free of damage,
o
rubber boot quality and 7mm gap.
o
Oil system integrity:
o
oil coloration and age (50 hrs.),
o
oil quantity,
o
lines routed without interference
and free of chaffing,
o
oil overflow line routing and condition,
o
connections for tightness,
o
oil tank secure,
o
hoses for cracks or signs of aging,
o
suppleness of lines,
o
fittings tight,
o
oil cap gasket quality.
o
Other engine electrical systems integrity:
o
oil pressure switch,
o
CHT sensor,
o
oil pressure sensor,
o
lines routed free of interference and chafing,
o
connections secure,
o
routing of all lines to the electronic
components mounted to the keel,
o
routing of electrical lines to control panel,
o
miscellaneous motor struc-
tures, casing for cracks, etc.
o
Battery system integrity:
o
battery box secure,
o
free of dammage and signs of wear,
o
connections
tight (ground, starter, engine ground,
o
battery terminals, starter relay),
o
cables routed free of interference
and chafing,
o
crimped ends secure to cables.
o
Lubrication of moving components:
o
all moving control surface hinges,
o
rudder pedal system includ-
ing pushrod ball joints,
o
toe brake system,
o
control stick bushings for elevator and one for aileron,
o
flap
actuator lever,
o
elevator trim tab hinges and control screw,
o
cable ends to rudder horns,
o
engine control
cable ends,
o
door opening mechanism if necessary,
o
throttle lever and red block all with light machine oil,
o
elevator push-pull rod and brake cylinders with anti-seize (do not any lubricate rod-ends).
o
Engine control system integrity:
o
throttle friction rod clean,
o
friction block adjusted,
o
verify idle
and full throttle advance of throttle cables,
o
micro-adjust throttle cables using dual vacuum gauges,
o
idle
settings correct,
o
engine tachometer reading correctly,
o
bolts and pins secure in throttle control system,
o
throttle cable housing free to move,
o
throttle and choke cables free of fraying and wear,
o
cable ends,
o
choke actuation satisfactory,
o
chokes close completly and open in synchronization,
o
friction of choke pull
is managable.
o
Brake system integrity:
o
fluid level ok,
o
fluid resevoir secure and cap tight,
o
all tubing for signs of
aging or embrittlement,
o
connections tight,
o
cylinder seals connections and lines for leaks,
o
brake cylinders
for leaks,
o
rotor and pads for wear,
o
routing of lines free of chaffing and interference,
o
parking brake valve
operates properly,
o
rotor bolts safetied properly,
o
brake cylinder free to float,
o
bleed fitting caps,
o
bleed
fiting tight,
o
cylinder and brake specific pedal components for mechanical integrity.
o
Landing gear system integrity:
o
tires inflated to 15psi,
o
tire for wear and aging,
o
wheel hubs and axles
for signs of cracking or dammage,
o
main gear leg and nose wheel strut for structural integrity and cracks,
o
nose wheel strut for excessive wear or dammage,
o
nose wheel strut for cleanliness of greased area,
o
maing
gear leg and nose wheel strut fuselage attach points for cracks or bending,
o
bolts and cotter pins for security.
o
ELT system integrity:
o
antenna for condition,
o
cables and routing for connection and chaffing,
o
condi-
tion of mounting system,
o
signs of wear or dammage to the support system,
o
operation of the ELT unit itself
for transmitter power and activation (during annual only),
o
age of system batteries and remote panel battery
including total duration of operation limitations,
o
lanyard and portable antenna onboard the aircraft.
o
Flap actuation system integrity:
o
console flap lever mechanism for cracks loose connections or dam-
mage,
o
end effectors for tightness and wear,
o
operational check of flaps throughout movement range,
o
flap
frame mechanically sound,
o
flap control hinges and bolt for wear and cotter pin,
o
flap fabric for dammage
and condition,
o
flap control horn for mechanical integrity and dammage,
o
actuation cables for routing and
safety wiring,
o
spring return system for wear and operation and dammage,
o
flap control rod exit fairings for
wear and integrity.
o
Elevator trim system integrity:
o
for proper friction free operation,
o
tightness and security of cable rout-
ing for chafing and interference,
o
trim tab for mechanical condition,
o
trim tab hinges for wear and tightness
of hing screws,
o
trim tab console mechanism for mechanical condition and wear.
PAGE 19
Содержание S-12
Страница 33: ...PAGE 33...
Страница 34: ...PAGE 34...