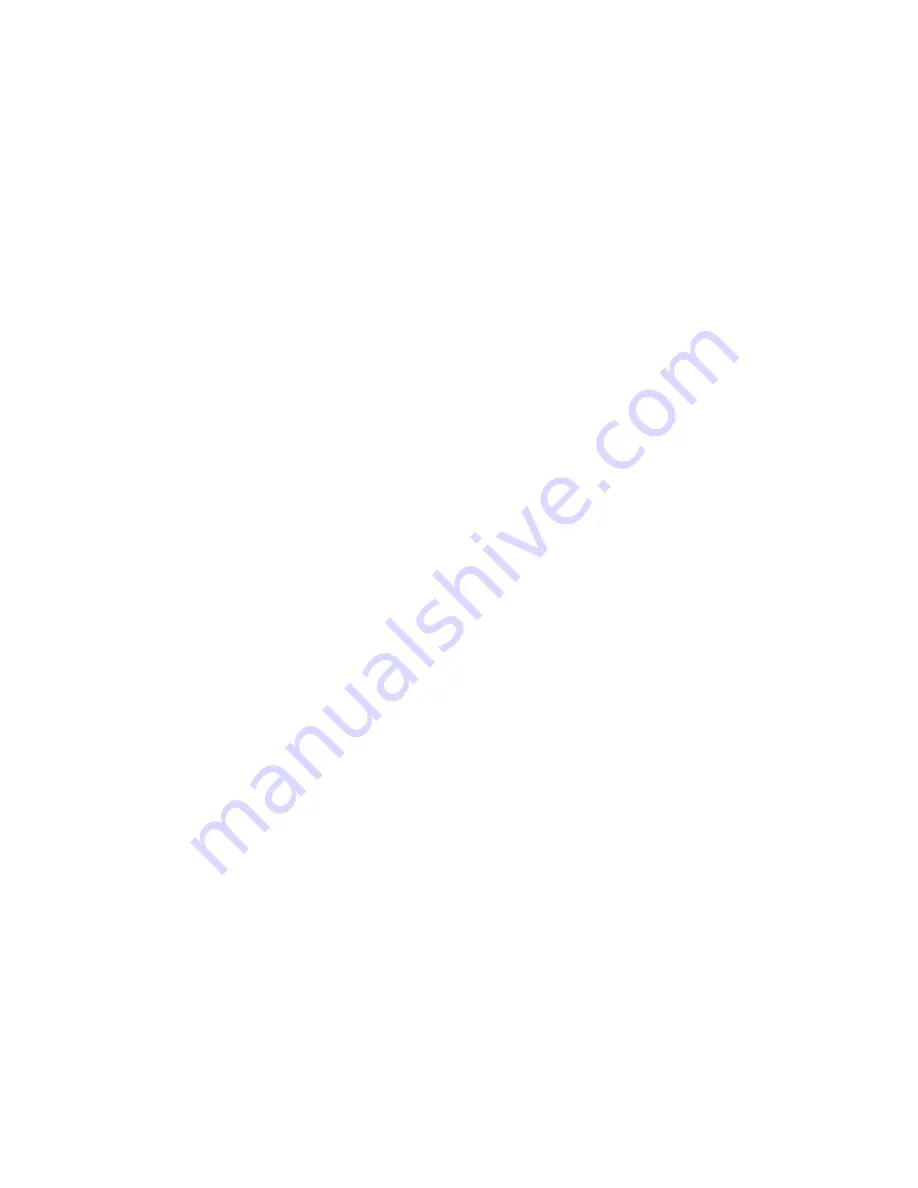
14
13. LED Display
The LED meter is used to display the main amperage when welding, it will also show
current parameter value when using selector buttons to scroll through additional settings I.E
Pre-flow gas, start amps, up-slope, peak amps, slope down, end amps, post flow gas etc.
14. TIG starting control
HF - Mode: The arc will automatically start when trigger pressed without touching tungsten
electrode to workpiece
Lift - Mode: The arc will start by touching the tungsten electrode to work piece, when the
tungsten is then lifted of the work piece the arc will start. Used for when welding on vehicles
with sensitive electronics.
15. Pre-flow gas
This sets the amount of time gas flow will happen before arc is started, for most jobs 0.1 -
0.5 seconds if fine, when welding stainless steel etc. where a longer gas purge time may
be required adjust accordingly. Range is 0 to 10 seconds.
16. Start Amps
When in TIG mode with 2T/4T operation set, this will adjust the start amperage
This allows you to set the initial start current from 5A DC. In 4T mode when trigger is
pressed and held you will remain at start amps, when you let go, the machine will then
go to main set amps.
Do not set the start amperage too low for tungsten size otherwise you may experience
sluggish / non arc starting. I.E a 3.2mm tungsten is for high range 160+ amps welding, so
you would not need to set start amps at 5. The thicker the tungsten used, the higher the
start amperage should be. We recommend setting below to achieve fast arc starting: -
1.0mm Tungsten - 5 Amps minimum
1.6mm Tungsten - 15 Amps minimum
2.4mm Tungsten - 30 Amps minimum
3.2mm Tungsten - 50 Amps minimum
17. End Amps
When in TIG mode with 4T operation set, this will adjust the end (final) amperage
18. Memory store
You can program up to 9 jobs into memory - very helpful when doing process welding.
Press button to select required memory and options will be set as pre-programmed into job.
To program, select job number required, enter parameters I.E amps / upslope / downslope /
gas post flow etc., then press and hold program button for 3 seconds, this will save current
settings.
19. Select function
Press to scroll through available parameters, once required parameter LED is lit, you can adjust by
turning selector knob (21) and then press knob in to store.