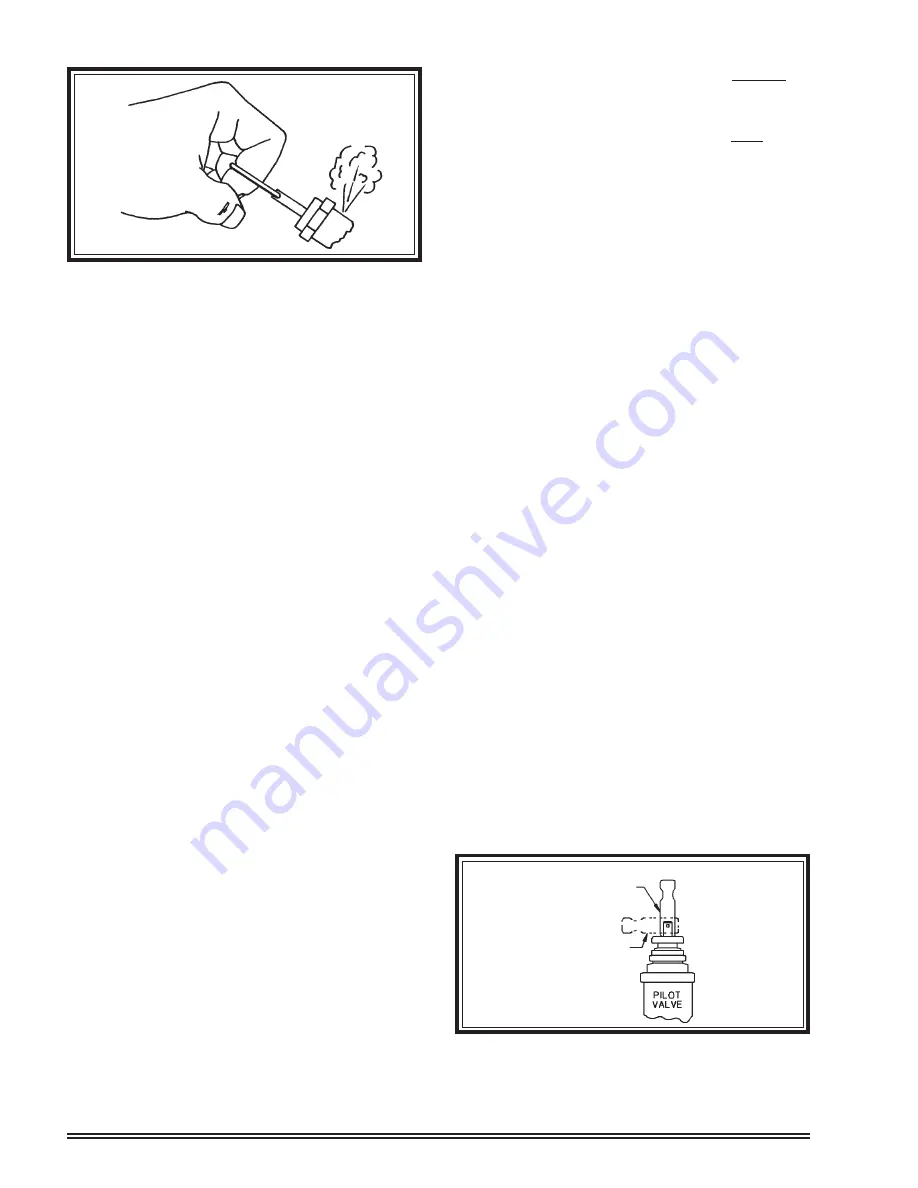
Industrial Series
Quincy Compressor
50263-106, October 2004
11
3501 Wisman Lane, Quincy IL - 62305-3116
Manually Draining An Air Tank:
Tank(s) subjected to freezing temperatures may con-
tain ice. Store the compressor in a heated area before
attempting to drain moisture from the tank(s).
Step 1)
Disconnect and lockout the compressor from
the power source (electric models) or discon-
nect the spark plug wire from the spark plug
(gas engine models).
Step 2)
Reduce the air pressure in the tank to 30
PSIG by pulling the pressure relief valve ring
(see Fig. 11).
Step 3)
Position yourself so that the moisture and air
to be expelled can not cause you harm.
Step 4)
Open the drain valve and allow the moisture
and air mixture to drain from the tank.
Step 5)
Once the moisture has been completely
drained, close the drain valve.
PRE-STARTING
CHECKLIST
WARNING !
Failure to perform the PRE-STARTING CHECKLIST
may result in mechanical failure, property damage,
serious injury or even death.
Steps 1 through 5 should be performed prior to
operating the unit. If any condition of the checklist is
not satisfied, make the necessary adjustments or
corrections before starting the compressor.
For gas engine start-up procedures, refer to the
gas engine owner’s manual.
WARNING !
Never assume a compressor is safe to work on just
because it is not operating. It could restart at any
time. Follow all safety precautions outlined in MAIN-
TENANCE.
Step 1)
Basic compressors are shipped without lu-
bricant in the crankcase. Add lubricant per
specifications.
(Refer to Lubrication).
Tank mounted units are shipped with break-
in lubricant in the crankcase. Check for proper
lubricant level.
(Refer to Lubrication.)
Step 2)
Make sure all pressure relief valves are cor-
rectly installed.
(Refer to SYSTEM COMPO-
NENTS)
Step 3)
Be sure all guards are in place and securely
mounted.
(Refer to SYSTEM COMPO-
NENTS)
Step 4)
On electric motor driven units, check fuses,
circuit breakers, and overload relays for
proper sizes.
Step 5)
Open the tank drain valve in the bottom of
the tank.
STARTING & STOPPING
THE COMPRESSOR
Constant Run Models
Step 1)
Flip the toggle on the pilot valve to the
“MANUAL UNLOAD” position
(see Fig. 12)
.
Step 2)
Start the compressor by plugging the power
cord into a properly grounded and rated
power source (electric models) or by starting
the gas engine (refer to gas engine owner’s
manual for start-up procedures).
Step 3)
Allow the compressor to run for a few min-
utes.
Step 4)
Flip the toggle on the pilot valve to the “RUN”
position. The compressor will start to deliver
compressed air to the tank.
Step 5)
Watch and listen for excessive vibration and
unusal noises. If either exist, stop the com-
pressor and refer to
TROUBLESHOOT-
ING.
Fig. 11 Checking Pressure Relief Valves
& Relieving System Pressure
Pix 1160
Fig. 12 Constant Run Starting
Toggle in
"MANUAL UNLOAD"
Position
Toggle in
"RUN"
Position
Содержание QTS Series
Страница 25: ......