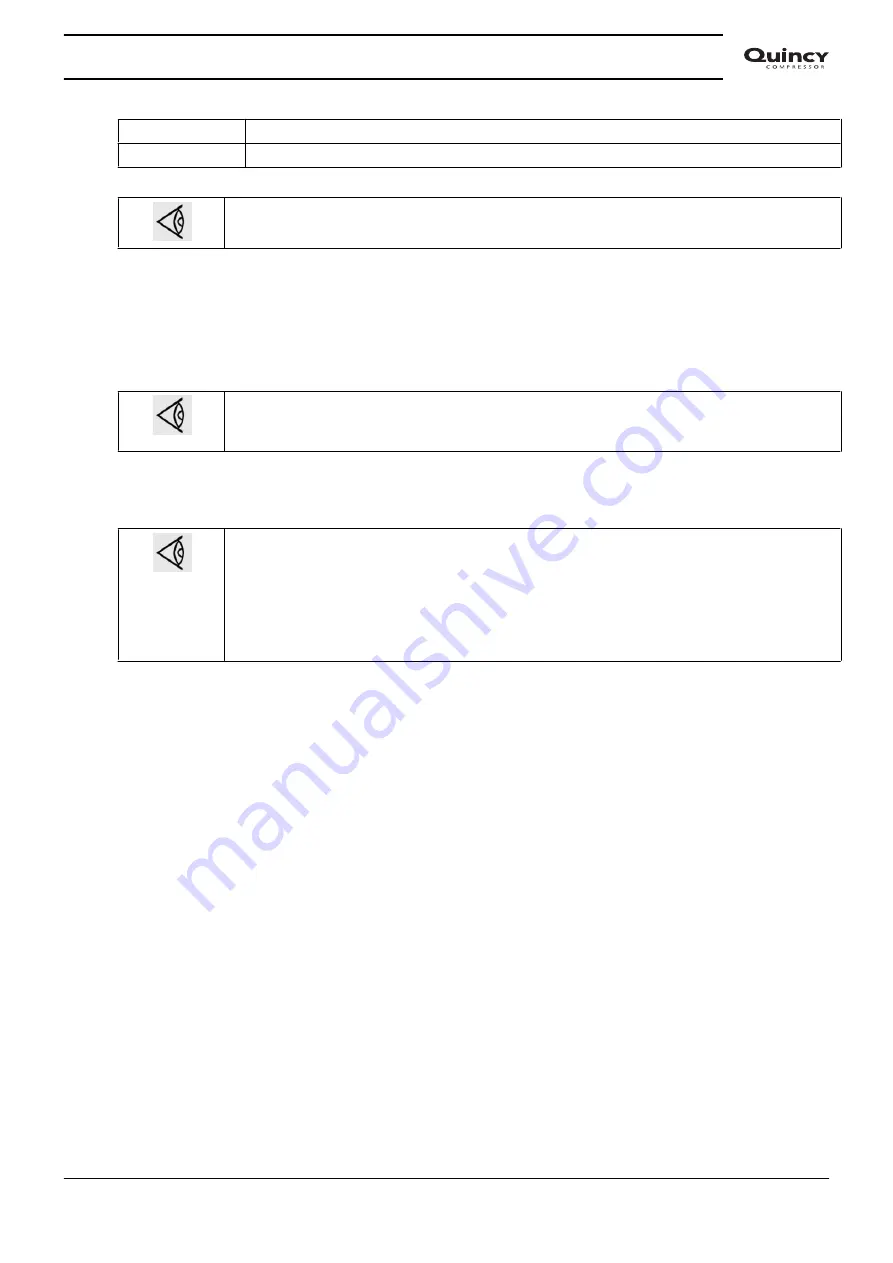
Reference
Designation
6
Doors fully open
For the dimensions A, L, B and H , contact your supplier.
4.2
Installation proposal
Outdoor/altitude operation
The compressor is not designed for installation outdoors.
Also, if the ambient temperature can fall down below 0 ˚C (32 ˚F), and if operating above 1000
m (3300 ft) precautions must be taken. In this case, , consult your supplier.
Moving/lifting
The compressor can be moved by a lift truck using the slots in the frame. Take care not to
damage the bodywork during lifting or transport. Make sure that the forks protrude from the
other side of the frame. The compressor can also be lifted after inserting beams in the slots.
Make sure that the beams cannot slide and that they protrude from the frame equally. The
chains must be held parallel to the bodywork by chain spreaders in order not to damage the
compressor. The lifting equipment must be placed in such a way that the compressor is lifted
perpendicularly. Lift gently and avoid twisting.
Instruction book
2920 7101 21
59
Содержание QGS 40
Страница 1: ...QGS 40 QGS 50 QGS 60 QGS 75 QGS 100 Instruction book Oil flooded rotary screw compressors...
Страница 2: ......
Страница 100: ......
Страница 101: ......