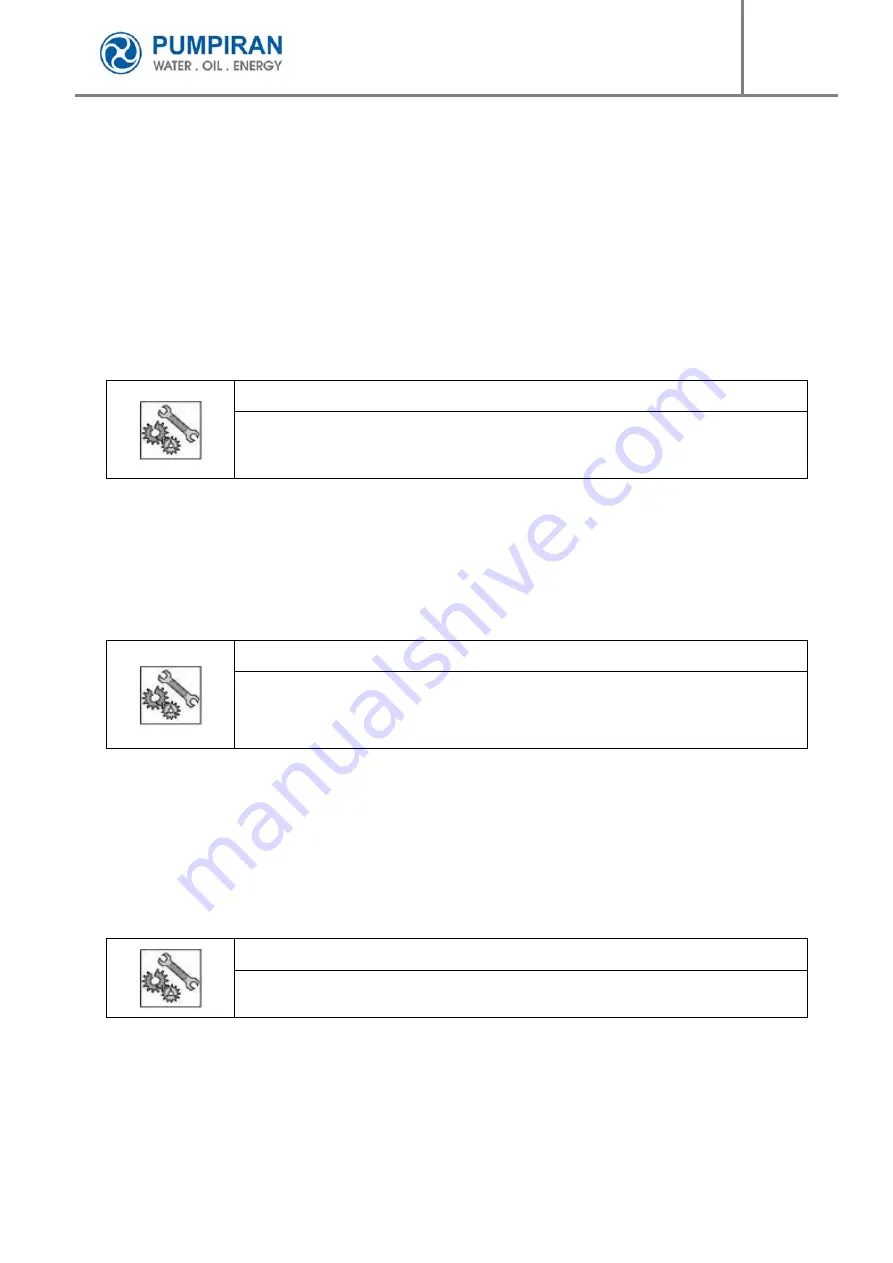
PB3 User Instruction
Page 26 of 39
e)
Ensure coupling is properly aligned and lubricated; and pump and driver are properly doweled.
(Refer to shaft /coupling alignment procedure).
f)
Ensure coupling guard is in place.
g)
Check torque of all bolting and plugs for tightness.
4.1.2 Initial startup procedure
a)
Close discharge valve if a bypass system is used. If not, crack open the discharge valve.
b)
Prepare the driver for start-up in accordance with the manufacturer’s instructions.
c)
Warm-up pump (if required).
Avoid severe thermal shocks to the pump as a result of sudden liquid temperature changes. The pump must be
preheated prior to start-up. Unless otherwise specified, the external temperature of the casing must be within
55.6 °C (100 °F) of the temperature of the liquid to be pumped at time of start-up.
Caution
Pump temperature stratification could occur. A maximum temperature delta of 28
°C (50 °F) between the upper and lower case shall be checked prior to starting the
pump
Due to the heavy metal sections, the casing will lag the liquid temperature during such changes, and severe
temperature stresses and subsequent misalignment of machined fits may result. Preheating is accomplished by
circulating a small amount of hot fluid through the casing by utilizing vents, drains or bypass from discharge
and suction. Preheat pump slowly at a rate not to exceed 55.6 °C (100 °F) per hour.
d)
Prime pump and ensure pump suction valve and bypass isolating valve are open.
Caution
Before starting or while operating the pump, the casing and suction line must be
completely filled with the liquid being pumped. The rotating parts depend on this
liquid for lubrication, and the pump may seize if operated without liquid.
e)
Ensure pump recirculating line (if provided) is open and free of obstructions.
f)
Check that pump is vented by observing leakage from casing vent and seal piping vent. Close vent when
liquid is emitted.
g)
Make sure seal piping is turned on.
h)
Prepare the driver for start-up in accordance with the manufacturer’s instructions.
i)
Check pump rotation by starting unit momentarily. The direction of rotation is shown on 10-4, pump
data sheet. Note the pump coasts to a gradual stop.
Caution
If pump stops abruptly when driver is shut down, investigate for pump binding. Take
necessary remedial action before resuming operation.
j)
Starting the driver (motor driven).
k)
Starting the driver (turbine driven).
l)
Start the turbine and bring it up to speed quickly.
m)
As soon as the pump is up to rated speed, open discharge valve. This will avoid abrupt changes in
velocity and prevent surging in the suction line.