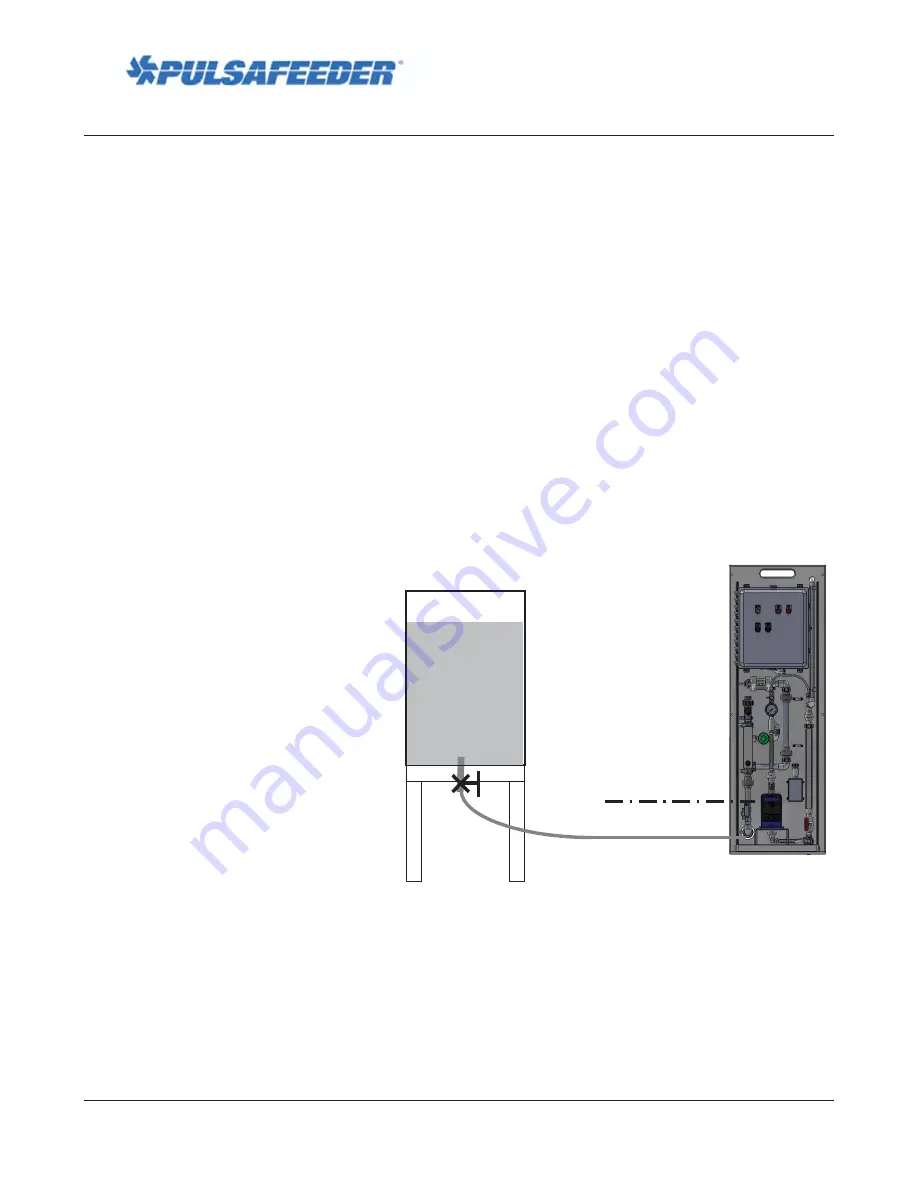
Automatic Polymer Makedown Systems
Installation, Operation and Maintenance Manual
72-910-APMDS-E Rev D
Skid Layout and Components
Page
8
Systems Overview
The Polymer Makedown System is designed to inject neat polymer into a clean water stream and to
agitate this mixture through a static mixer causing the polymer strands to expand into a ‘made-down’
aqueous solution. The solution is stored in the polymer solution day-tank and mixed occasionally with
the rotary mixer located in the tank. The tank outlet is typically connected to the dosing pump(s) which
inject the solution into the process application. The dosing pump(s) are not provided with the Polymer
Makedown System and are not powered by the System.
Supply Side
Dosing chemicals are usually sourced from a barrel or tote container. The source must be located
above the centerline of the neat polymer pump which is referred to as a “flooded suction”. Because
Neat Polymer is a high viscosity fluid, the supply should never be located below the centerline of the
pump(s) which is referred to as “suction lift.” Connections to and from the Neat Polymer Tank are
most commonly made with flexible hose or tubing although they may be made with hard piping. The
Neat Polymer Tank should be covered to prevent contamination.
Process side
Pump
Neat
Polymer
Tank
Supply
Line
Figure 3
Flooded Suction
Flooded Suction
This is the most trouble free type of installation.
Since the Supply Line tubing is filled with
chemical, priming is accomplished quickly and the
chance of losing prime is reduced.
Recommended for very low flow rate applications.
e.g. 2 ml/hr, or where pumping solutions such as
sodium hypochlorite or hydrogen peroxide which
can form air bubbles.
Supply Line should gradually slope downward
from the Solution Tank to the Skid Suction
Connection.
It is strongly recommended to add a drain
provision on the suction side to facilitate
emptying and flushing of the system for
maintenance.