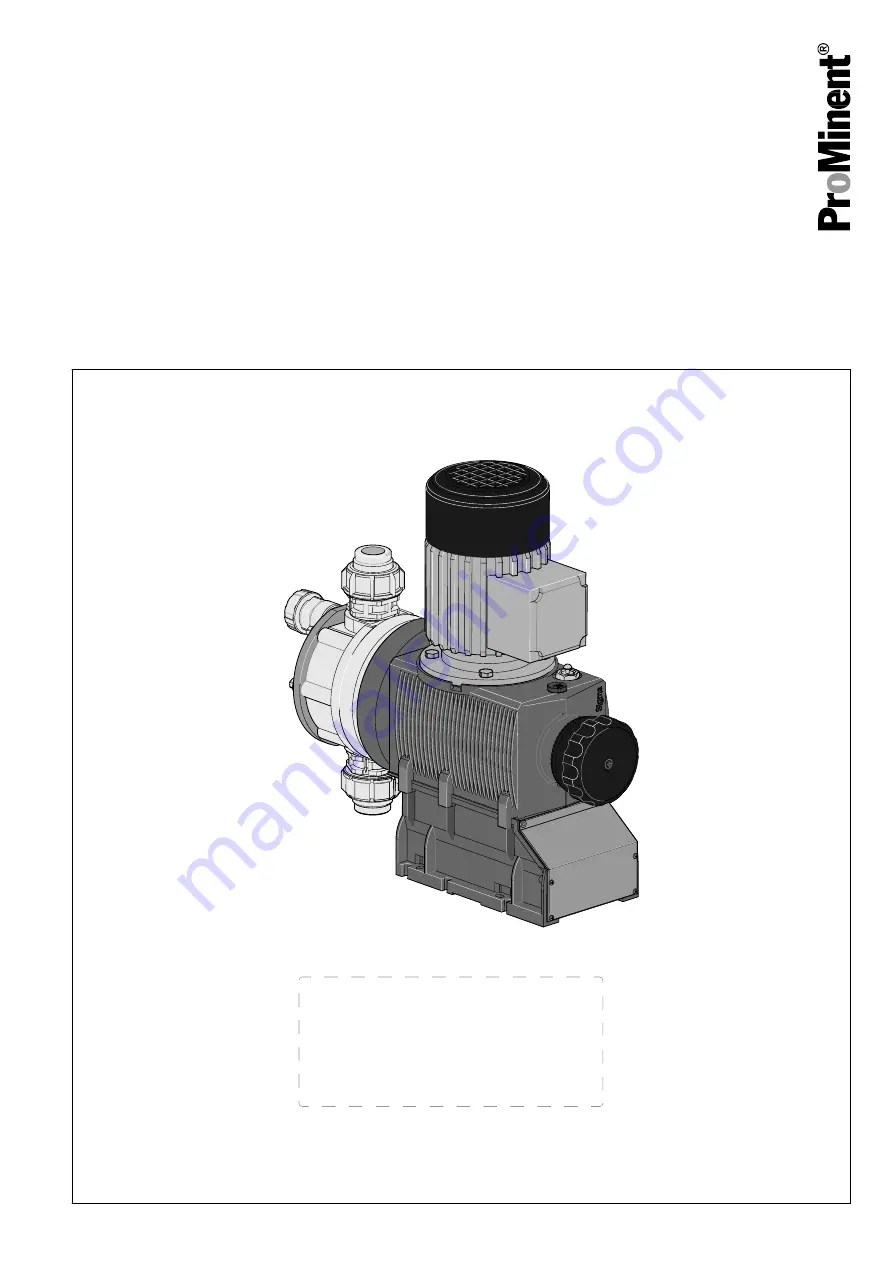
Diaphragm motor-driven metering pump
Sigma/ 2 Basic type S2Ba
Operating instructions
P_SI_0074_SW
Target group: Minimally instructed personnel
EN
Original operating instructions (2006/42/EC)
Part no. 985908
Version: BA SI 107 07/22 EN
Please carefully read these operating instructions before use. · Do not discard.
The operator shall be liable for any damage caused by installation or operating errors.
The latest version of the operating instructions are available on our homepage.
Содержание Sigma / 2 Basic S2Ba
Страница 87: ...87...