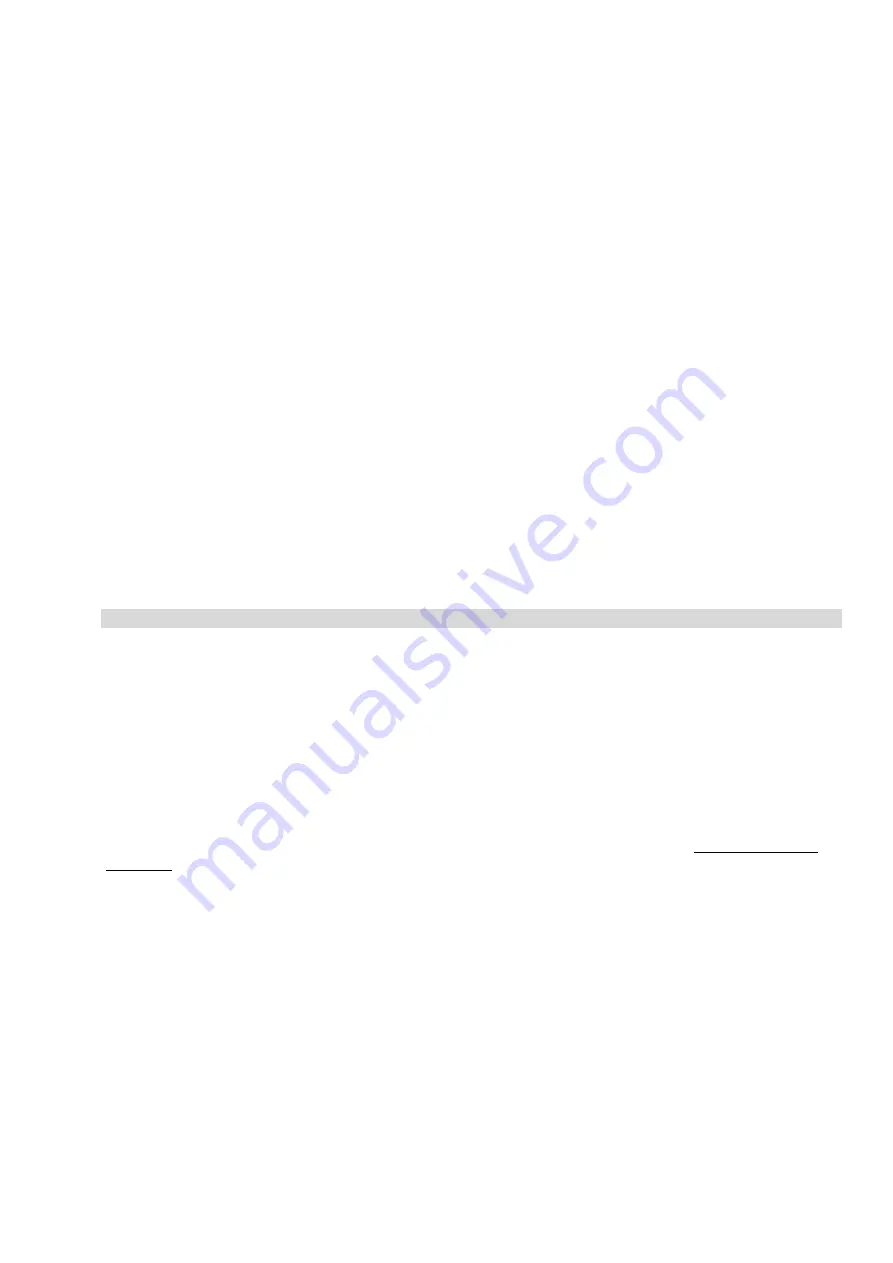
Discharge
thermostat
ZF models (ZF09 to ZF18) have an external discharge thermostat which controls the discharge temperature.
The thermostat cut-off point is 99°C +/- 4 K
The cut-in differential is 28 K +/- 5 K
ZF models (ZF24 to ZF48) have an internal discharge probe (temperature : 140°C)
ZB50KCE to ZB114KCE scroll compressors have the addition of the Advanced Scroll
Temperature Protection (ASTP). Advanced Scroll Temperature Protection is also a temperature
sensitive thermo-disc that acts to protect the compressor from discharge gas overheating. Once
the discharge gas reaches a critical temperature, the ASTP feature will cause the scrolls to
separate and stop pumping although the motor continues to run. After running for some time
without pumping gas, the motor protector will open.
NOTE: Depending upon the heat build-up in the compressor, it may take up to two hours
for the ASTP and motor protector to reset!
Crankcase heater
The crankcase heater must be powered and operational during compressor shut-downs.
AUTOMATIC MECHANICAL DEVICES
As standard the unit is controlled by pressure switches:
1 LP pressure switch (automatic reset) for each compressor
1 HP pressure switch (automatic reset) for each condenser fan.
As option electronic controlled could by installed (refer to instruction manual joined to electrical diagram)
Particular case of units with Digital compressor: LP control is managed by specific controller.
START-UP OPERATIONS
PRELIMINARY CHECKS AND OPERATIONS
General information
Ensure that all the threads are fully tightened on connection flanges, flexible connections and cables as jolting during transport
could cause screws and bolts to loosen.
Check also, for same reasons, if there are any breaks in the piping.
Ensure that the flexible connections are not in contact with metal parts. Vibrations from the compressor can cause wear in these
until they rupture at the point of friction.
Switch on crankcase heaters 24 hours before start-up.
Before starting up a machine with pressurised tanks, all service valves must first be opened upstream and downstream and all
external valves closed.
Determining the compressor rotation direction
Important:
Scroll compressors only have one rotation direction. Any rotation in the opposite sense may
lead to a compressor
destruction.
During the first start up, it is absolutely necessary to determine the phases connections to compressor terminals. That
handling must be tactful with hermetic compressors and must be extremely fast.
-
Place a LP pressure gauge at the compressor suction or on the header.
-
Start up the compressor with the start button
-
As soon as it is started, stop the compressor (this handling must last less than 1s)
-
During that time, if the pressure gauge showed that the pressure went down, the rotation direction is correct.
-
In the opposite case, invert the 2 phases on the compressor breaker and repeat the same operation for checking.
Leaks
testing
Pressurise the whole system, including the compressors, using a neutral gas
(Nitrogen) with a tracer at a minimum pressure of
10 bars and at a maximum pressure below 17 bars, isolating the LP (low pressure) switches.
Important
: If the LP (low pressure) circuit is fitted with a safety valve (e.g.: on the suction accumulator) the test pressure on that
part of the circuit should be approx. 20% below the operating pressure of this valve.
Thorough leakage detection using haloid lamp or electronic detector should be carried out on the power pack.
After these tests, the gas must be removed. Fit the drier cartridges in their casing.
17/21
Содержание GCV B2H ZF15
Страница 50: ...NOTICE D INSTRUCTIONS GENERALE POUR COFFRETS ET ARMOIRES ELECTRIQUES V3 0 Page 14 51...
Страница 77: ...NOTICE D INSTRUCTIONS GENERALE POUR COFFRETS ET ARMOIRES ELECTRIQUES V3 0 Page 40 51...
Страница 91: ...NOTICE D INSTRUCTIONS GENERALE POUR COFFRETS ET ARMOIRES ELECTRIQUES V3 0 Page 53 51...