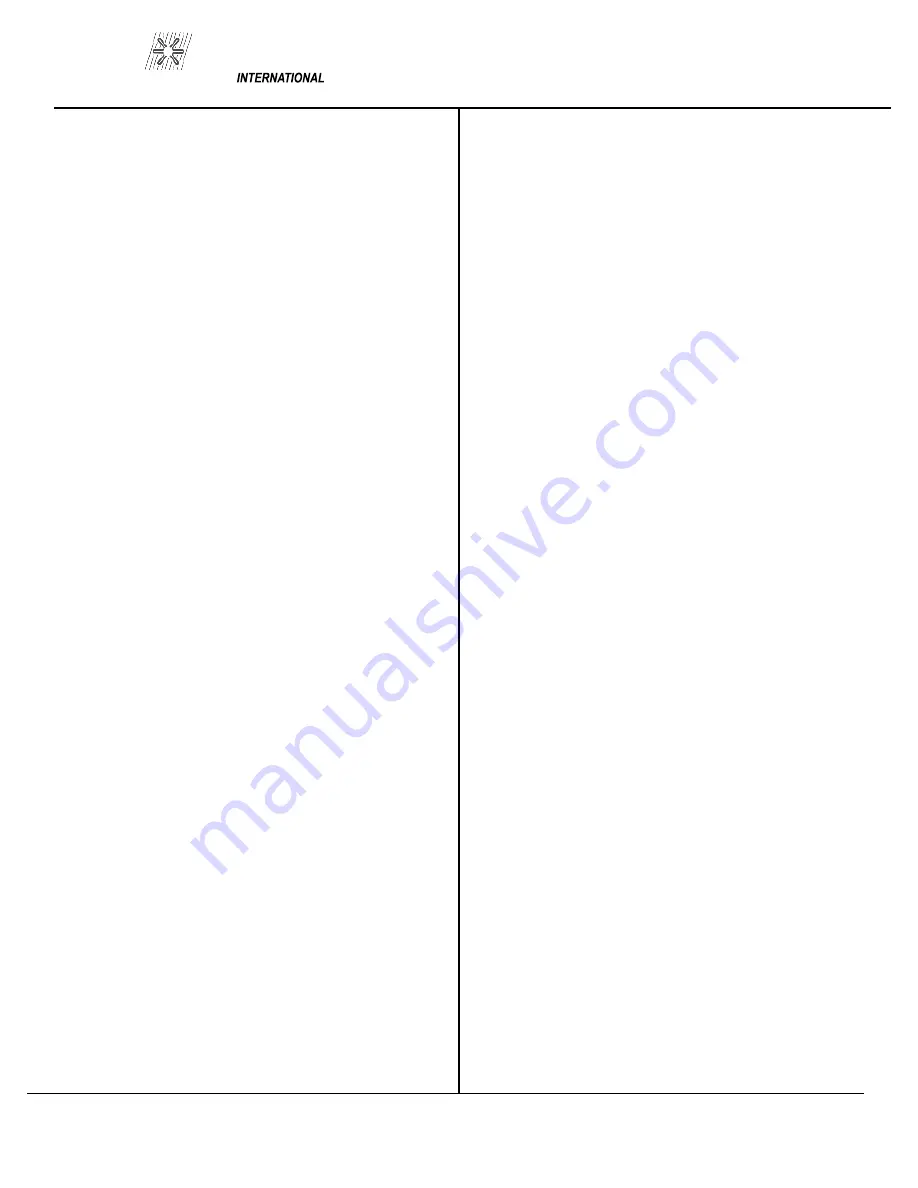
PRO
WEL D
3 0 0 -0 8 0 5
7.0 WELD TEST AND INSPECTIONS
Testing of weld quality beyond visual inspection
varies with stud characteristics. Refer to AWS
(American Welding Society) Structure Welding
Code AWS D.1-Rev. 1-76. Welding procedures
are covered in Sections 4.28 and 4.29. Weld test
and inspection is covered in Section 4.30, para-
graphs 1 through 4. (American Welding Society,
Inc., 2501 N.W. 7th, Street, Miami, Fla. 33125).
7.1 Weld Test
A. Bend Test
A bend test may be used to test weld results if the
stud may be destroyed. This is usually done with a
bending tool (a hollow pipe with an inside diameter
just large enough to fit over the diameter of the
studs). The bend tool is placed over the stud, down
to the base material. The stud is then be repeatedly
bent away from its axis until failure occurs.
B. Torque Test – Threaded Studs
A torque test may be used on threaded studs. The
stud is twisted to the point of failure. A twisting
tensile load is applied by using a collar, washer and
nut. A bend test can be used on threaded studs as
well.
C. Test Results
In an acceptable weld, failure will occur in the stud
material or tear out of a thin base plate. Failure in
the weld requires adjustment of procedure, weld
time and current setting.
7.2 Weld Inspection
Weld quality can be visually inspected. Refer to Fig-
ure 7-1 as a reference to the quality of the weld.
7.3 Causes Of Poor Or Erratic Welds
1. Loose chuck. Does not grip stud tightly.
(replace) Not enough engagement of stud to
chuck. (Adjust stop)
3. Poor surface condition of base material, excessive
oil, grease, rust, etc. (Clean)
4. Weld current or weld time setting too low or too
high. (Adjust to diameter of studs)
5. Broken or loose cables. (Repair)
6. Dirt in gun. (Clean)
7. Incorrect polarity. (Cables hooked-up wrong)
8. Cables too closely coiled.
9. Arc blow is evidenced by “one side” welds. In
severe cases there will be no melting under one
edge of flange while the opposite side is gouged
out or appears excessively hot. The principle
cause of arc blow is a magnetic field induced by
the current flow during the weld. It occurs most
often on long, narrow strips of metal or near
edges of sheets or plates. In some cases, a
change in grounding positions, or two ground on
the work piece, one at each end or edge of work,
will correct the problem
PAGE 5
Содержание AG-805
Страница 1: ...OPERATION MAINTENANCE MANUAL ...
Страница 2: ......
Страница 4: ...PRO WELD 300 0805 ...
Страница 5: ...300 0805 PRO WELD ...
Страница 6: ...PRO WELD 300 0805 ...
Страница 7: ...300 0805 PRO WELD ...
Страница 19: ...300 0805 PRO WELD ...
Страница 20: ...WELD PRO MANUFACTURED BY MADE IN THE U S A ...