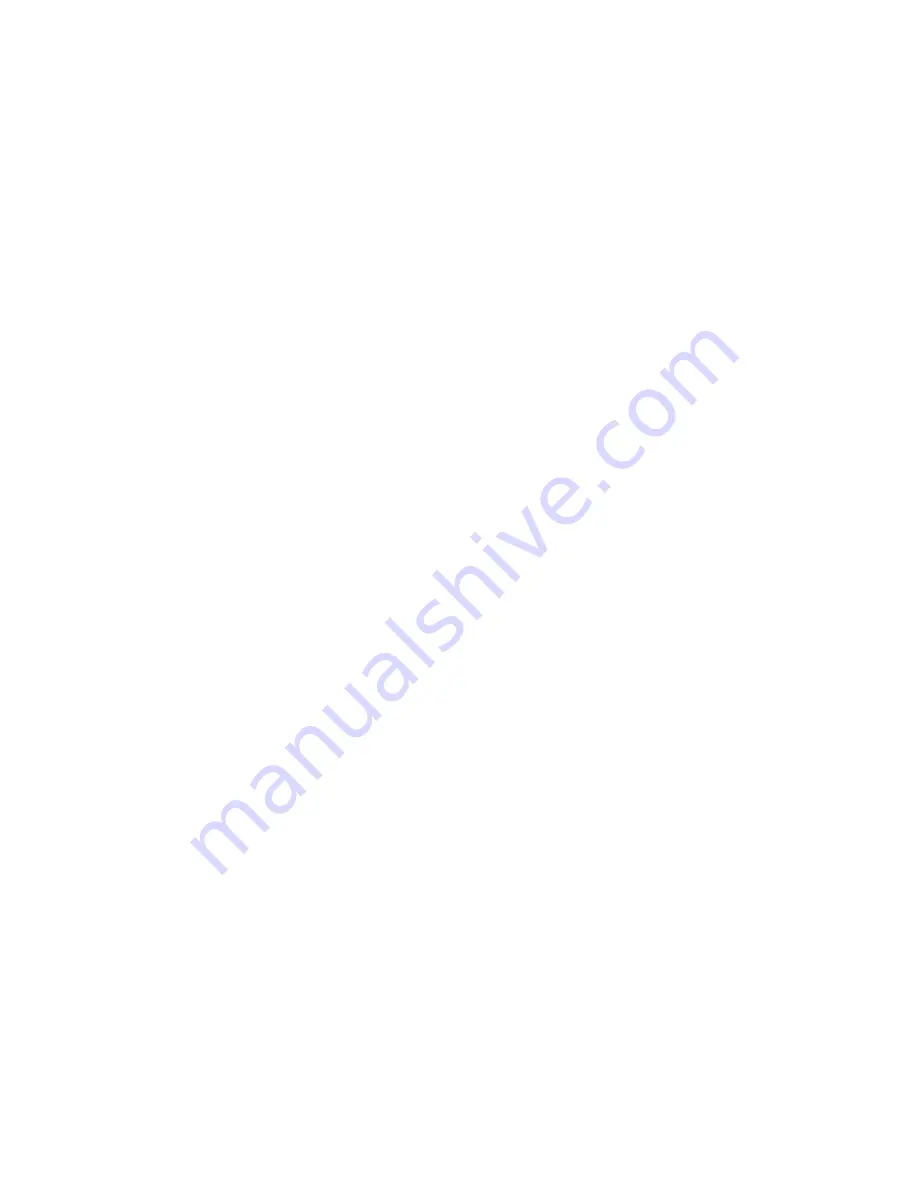
PreciseFlex_Robot
22
Robot Workcell Design
Introduction.
The PF400 is always configured as a “Collaborative Robot”.
It is designed for light
duty applications with a payload of either 500gms or 3kg depending on the model. The plate handler
robot is designed so that maximum forces in the horizontal plane do not exceed approximately 60
Newtons and maximum slow motion forces in the downward Z direction do not exceed 60 Newtons. At
the maximum Z downwards speed of 500mm/sec, crash forces can reach 206N for collision with a hard
surface. High speed impacts for the robot or linear rail, which could trap an operator against a surface
may be avoided by teaching an “Approach” position which is a greater distance from a fixture than any
operator appendage that might enter the workcell, and first moving to this “Approach” position at high
speed, then moving to the final position at a slow speed which will not create excessive force in the event
of a trapped operator.
Workcell Design Recommendations for the PF400
Workcell designers are referred to EN ISO 10218-2:2011 for information on designing safe workcells.
Note especially that even a safe robot, when equipped with a tool that renders it dangerous, should be
protected from contact with an operator. For example, a robot which can only apply 60 Newtons of force
could plunge a sharp needle through a person’s hand.
Note that designing a robot workcell can be compared to driving a car. When approaching obstacles (or
parking) you slow down.
Safety Glasses.
It is required that operators who will move inside the work volume of any robot wear
safety glasses at all times, both to prevent any poking injury to the eyes, and also because the machine is
often moving around liquids which may be hazardous to the eyes.
Workcell Layout
. The PF400 is designed so that the gripper is the lowest point on the robot and cannot
descend all the way to the mounting surface (table). Because of this feature, the workcell designer
typically does not need to worry about the outer link or inner link of the robot trapping an operator’s
appendage. The workcell designer will be programming the robot to move 80 to 500 gram workpieces
from storage into expensive instruments and back to storage. When moving in and out of storage racks,
the robot may make large motions at higher speeds in the Z direction outside the storage rack. As long
as the workcell designer leaves 50mm or so between the table and the lowest access point on the
storage rack, the robot will never pin an operator’s hand to the table at a high speed. When the robot is
moving horizontally in and out of the storage racks the maximum forces are well below any injury
threshold.
See Appendix A below for an example PLr evaluation for an example PF400 workcell.
Содержание PF3400
Страница 8: ......
Страница 32: ...PreciseFlex_Robot 24 Appendix B TUV Verification of PF400 Collision Forces...
Страница 33: ...Introduction to the Hardware 25...
Страница 34: ...PreciseFlex_Robot 26...
Страница 35: ...Introduction to the Hardware 27...
Страница 37: ...Introduction to the Hardware 29 Appendix C Table A2 from ISO TS 15066 2016...
Страница 38: ...PreciseFlex_Robot 30 Table A2 Continued...
Страница 41: ...Introduction to the Hardware 33 PF400 500gm Safety Circuits PF3400 3kg Safety Circuits...
Страница 44: ...PreciseFlex_Robot 36 Finger Mount Height from Base PF400 Gripper Flange Mount Height from PF3400...
Страница 45: ...Installation Information 37...
Страница 46: ...PreciseFlex_Robot 38...
Страница 47: ...Installation Information 39...
Страница 48: ...PreciseFlex_Robot 40...
Страница 54: ...PreciseFlex_Robot 46 Schematic System Overview...
Страница 55: ...Hardware Reference 47 Schematic FFC Boards Revision B PF400...
Страница 56: ...PreciseFlex_Robot 48...
Страница 57: ...Hardware Reference 49 Schematic FFC Boards Revision C PF400...
Страница 58: ...PreciseFlex_Robot 50 Schematic FFC Boards 3kg PF400...
Страница 59: ...Hardware Reference 51...
Страница 60: ...PreciseFlex_Robot 52 Schematic Safety System Overview PF400 CAT3...
Страница 61: ...Hardware Reference 53...
Страница 62: ...PreciseFlex_Robot 54 Controller Power Amplifier Connectors Control Board Connectors...
Страница 63: ...Hardware Reference 55 Gripper and Linear Axis Controller Connectors...
Страница 64: ...PreciseFlex_Robot 56...
Страница 65: ...Hardware Reference 57...
Страница 66: ...PreciseFlex_Robot 58 Schematic Slip Ring for 60N Gripper...
Страница 67: ...Hardware Reference 59...
Страница 68: ...PreciseFlex_Robot 60...
Страница 69: ...Hardware Reference 61...
Страница 70: ...PreciseFlex_Robot 62...
Страница 71: ...Hardware Reference 63...
Страница 72: ...PreciseFlex_Robot 64...
Страница 73: ...Hardware Reference 65 Motor 60N Gripper...
Страница 74: ...PreciseFlex_Robot 66...
Страница 106: ...PreciseFlex_Robot 98 b The CALPP application takes about 1 minute to run...
Страница 124: ...PreciseFlex_Robot 116 Wiring for 60N Gripper with Battery Pigtail Wiring for Pneumatic Gripper...
Страница 125: ...117 Wiring for Vacuum Gripper Wiring for Vacuum Pallet Gripper...
Страница 129: ...121 Gripper racks centered in fully closed position Gripper racks centered in fully open position...