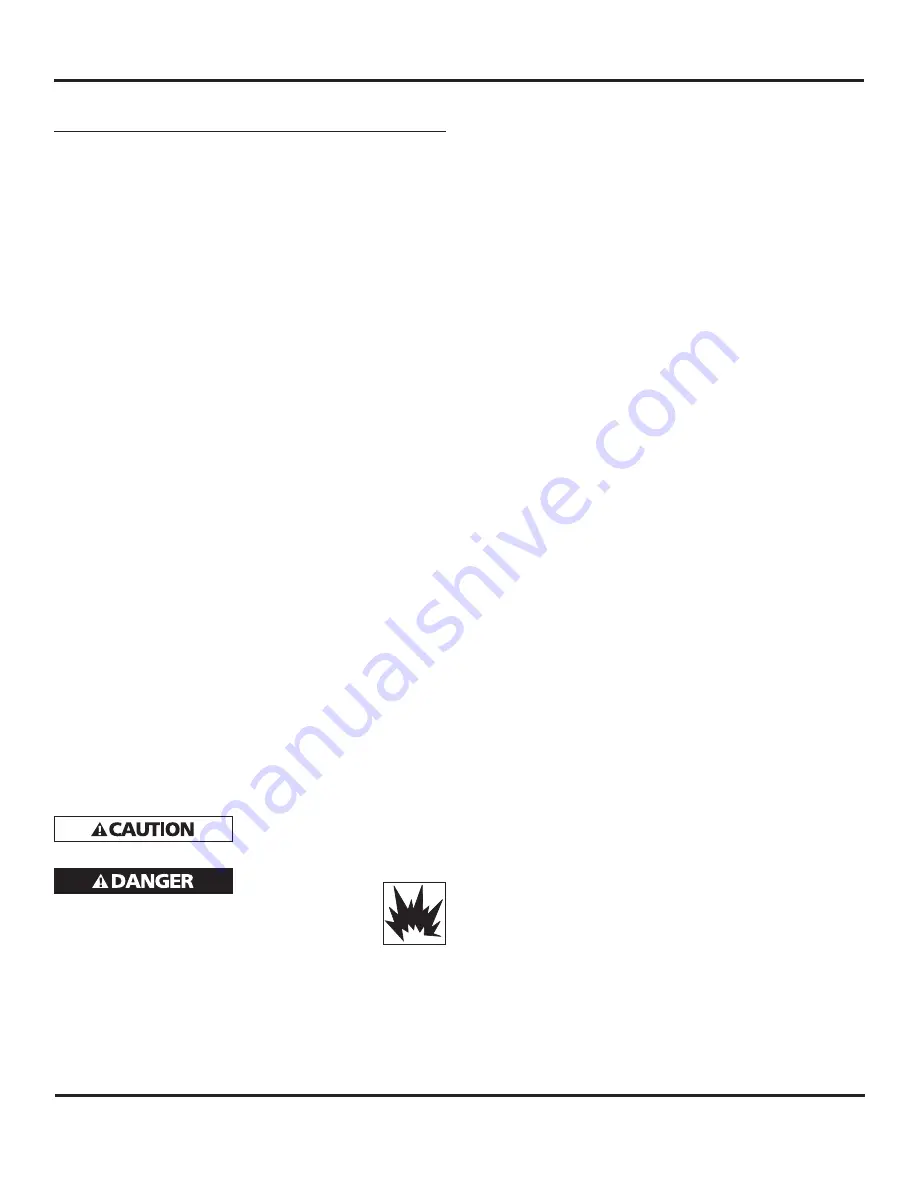
2
Claw Medical Vacuum Systems
Components
VaCUUm PUmPS
Powerex medical vacuum systems use electric motor driven
claw type pumps to create vacuum for the removal of
unwanted fluids and gases. The pumps remove the gases and
exhaust them to atmosphere through the exhaust piping
system.
Systems consist of multiple vacuum pumps that are
automatically controlled and may be isolated using valves
for service. One pump is used as the reserve. The control
system will trigger alarm actions in accordance with NFPA 99
requirements if the capacity of the reserve pump is needed.
The control system operates the available pumps in response
to vacuum demand as determined by the vacuum switches or
sensor. If needed, the controls will include minimum run timer
functions to prevent frequent starting and stopping of the
electric motors.
The vacuum pump assemblies are mounted with vibration
isolation Each vacuum pump has its own motor. The motors
are mated to the vacuum pumps by a flange mounting and
coupling system. Some models include auxiliary cooling fans.
Maintenance instructions are provided for the vacuum pumps
and motors in the separate manual. Each vacuum pump has
an intake assembly that includes 10 micron polyester filters
for each pump with a small fitting or pipe plug for releasing
the vacuum and facilitating the removal of the filter covers
when the pump is isolated the system is still under vacuum.
Each pump has an in-line check valve and an anti-reverse flow
valve to prevent them from running backwards when off. An
inlet screen protects the pump from large particles entering
the rotor / vane area.
reCeiVer Tank
The receiver tank in a Powerex Medical Vacuum System
is plumbed so that it sees the system vacuum. It is not
pressurized in normal use and should not be connected to
any pressure sources. The ASME National Board registered
air receiver is provided with a manual drain valve as standard
and optional auto drain and sight tube set ups are available.
Systems may be built with receivers separately mounted or
with vacuum pumps and controls integrally mounted.
Factory installed receiver is
used for vacuum capacity only
and is NOT a collection receiver.
Never drill holes in,
or perform any
welding on receiver tanks (unless qualified by
ASME to do so) or use them beyond the rated
pressure settings. Never mount other machinery or
equipment on receivers.
STanDarD ConTrol Panel
Built in a Nema 4/12 enclosure, the controls are UL508A
labeled and NFPA compliant. The panels have a single
incoming power connection point and two control
transformers with supplementary fused protected on primary
and secondary circuits. Systems are designed for automatic
alternation via PLC control. Systems with two to four motors
utilize field adjustable vacuum switches. Systems with five
or more motors utilize a vacuum transducer. Each motor in
the system is equipped with a magnetic starter and lockable
motor protector circuit disconnect.
All systems have a 30 minute alternation cycle with 10 minute
minimum run timers for each pump to prevent short cycling
and motor damage. Additional features include:
• “Reserve Pump in Use” alarm with visual and audible
indicators.
• “Reserve Transformer in Use” visual indicator.
• “Power On” light
• “Lamp Test” push button
• Audible alarm “Acknowledge” push button
• Alarm “Reset” push button
• Dry contacts on a labeled terminal strip for remote alarm
connection.
• Lighted HOA switch
• Hour meter for each motor