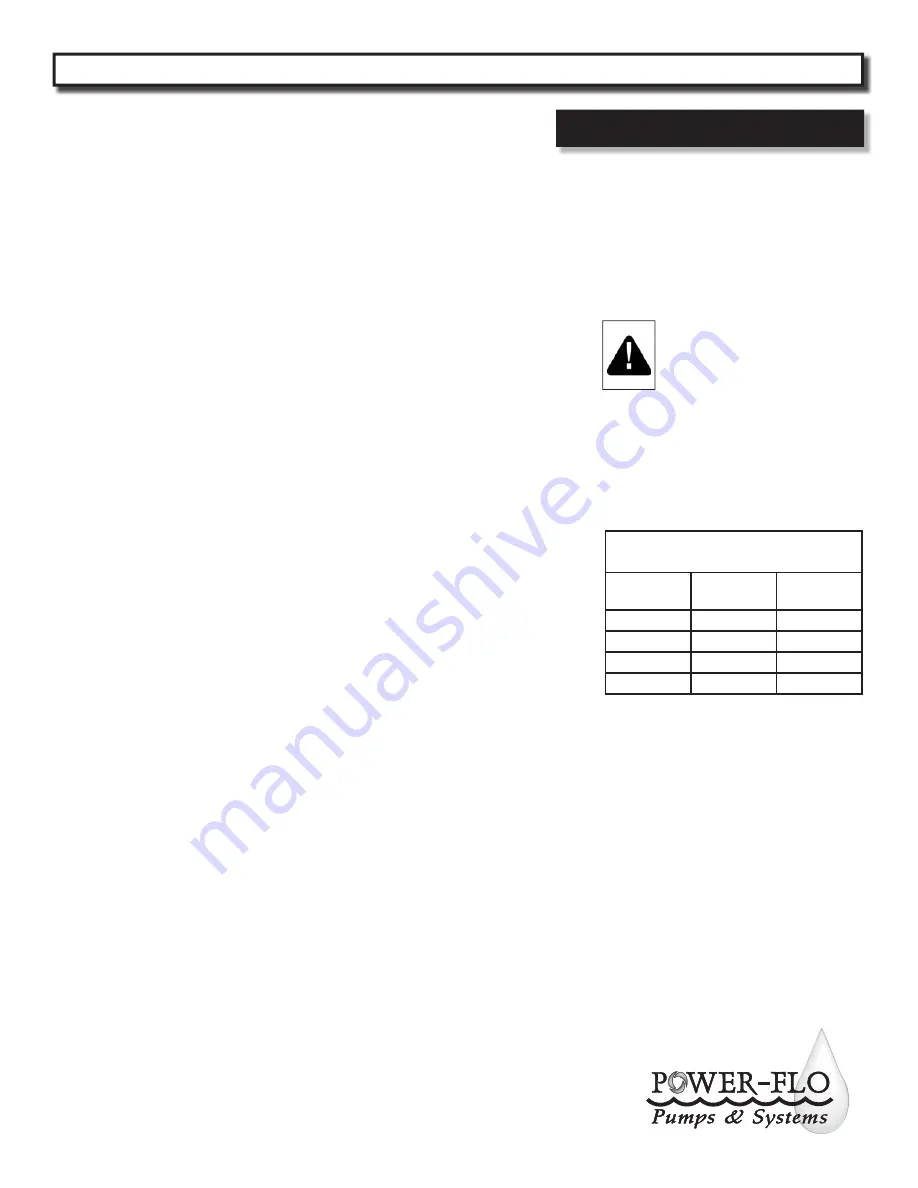
Power-Flo Pumps & Systems • 877-24PUMPS • www.powerfl opumps.com
7
Installation
There are several methods of installing
grinder pumps. See contract plans and/
or specifi cation: A slide rail in a package
system or concrete wet well is the most
common, which allows the pump(s)
to be installed or removed without
requiring personnel to enter the wet
well.
The sump or basin shall be sealed
and vented in accordance with local
plumbing codes.
This pump is designed
to pump grinder or wastewater,
nonexplosive and noncorrosive liquids
and shall NOT be installed in locations
classifi ed as hazardous in accordance
with the National Electrical Code (NEC)
ANSI/NFPA 70 or Canadian Electric
Code (CEC).
The pump should never be
installed in a trench, ditch, or hole with
a dirt bottom. The legs will sink into
the dirt and the suction will become
plugged.
The installation should be at a suffi
cient
depth to ensure that all plumbing
is below the frost line. If this is not
feasible, remove the check valve and
size the basin to accommodate the
additional backfl ow volume.
Discharge Piping
Discharge piping should be as short
as possible and sized no smaller than
the pump discharge.
Do not reduce
the discharge pipe size below that
which is provided on the pump.
Both
a check valve and a shut-off valve are
recommended for each pump. The
check valve is used to prevent backflow
into the sump. The shut-off valve is
used to manually stop system flow
during pump servicing.
Liquid Level Controls
The level control(s) should be mounted
on the discharge piping, a cable rack
or fl oat pole. The level control should
have adequate clearance so it cannot
hang up in it’s swing and that the pump
is completely submerged when the
level control is in the “Off ” mode. By
adjusting the cord tether the control
level can be changed. One cycle of
operation should be observed, so that any
potential problems can be corrected.
It is recommended that the level control
fl oat should be set to insure that the liquid
in the sump never drops below the top of
the motor housing or a minimum level of
10 inches above the basin fl oor.
Electrical Connections
Power cable -
The power cable mounted
to the pump must not be modified in any
way except for shortening to a specific
application. Any splice between the pump
and the control panel must be made in
accordance with the electric codes. It
is recommended that a junction box, if
used, be mounted outside the sump or be
of at a minimum Nema 4 construction if
located within the wet well.
DO NOT USE
THE POWER CABLE TO LIFT PUMP.
Always rely upon a Certifi ed Electrician for
installation.
Thermal Protection:
The normally closed (N/C) over
temperature sensor is embedded in the
motor windings and will detect excessive
heat in the event an overload condition
occurs. The thermal sensor will trip when
the windings become too hot and will
automatically reset when the pump
motor cools to a safe temperature. It is
recommended that the thermal sensor be
connected in series to an alarm device to
alert that an overtemperature condition
and/or motor starter coil to stop pump.
In the event of an overtemperature,
the source of this condition should be
determined and repaired immediately.
Thermal protection shall not be used as a
motor overload device. A separate motor
overload device must be provided in
accordance with NEC code.
WARNING! - DO NOT LET
THE PUMP CYCLE OR RUN IF
AN OVERLOAD CONDITION
OCCURS !
If current through the temperature sensor
exceeds the values listed, an intermediate
control circuit relay must be used to
reduce the current or the sensor will not
work properly.
TEMPERATURE SENSOR ELECTRICAL
RATINGS
Volts
Continuous
Amperes
Inrush
Amperes
110-120
3.00
30.0
220-240
1.50
15.0
440-480
0.75
7.5
600
0.60
6.0
Moisture Sensor:
To detec any moisture present a normally
open (N/O) probe is installed in the seal
chamber. The probe should be connected
in series to an alarm device or motor
starter coil to alert the operator that
moisture has been detected. Check the
probe leads for continuity, (∞ resistance
= no moisture). Also check the junction
box and control panel for moisture
content as this may induce a false signal.
IF MOISTURE DETECTION OCCURRES,
MAINTENANCE SHOULD BE DONE TO
IDENTIFY AND REPAIR.
Receiving & Installation
PFG 3, 5 & 7.5HP
Submersible Grinder Pumps