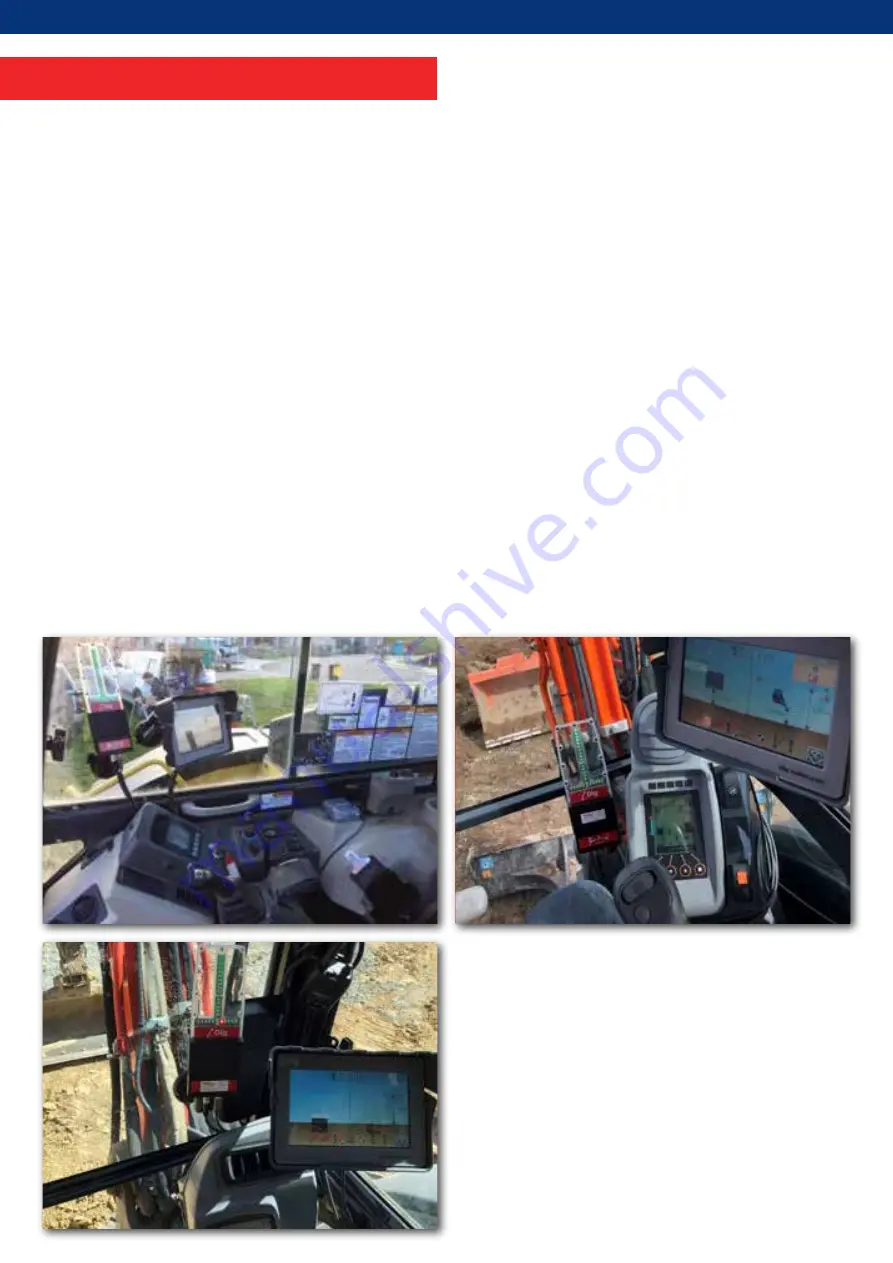
Stage 1 – Hardware Installation
This process will consist of the following steps:
•
Step 1 - Installation of LED Indicator and C-Box in cab
•
Step 2 - Installation of 2D Sensor in cab
•
Step 3 - Installation of Mounting Plates for Boom and Dipper Sensors
Step 1 - Installation of LED Indicator and C-Box
Machine is to be powered off.
•
Before plugging in the cables, find suitable locations to mount the LED Indicator and Screen.
•
The LED indicator should be put on the front window, in your field of vision of the working area outside.
•
The C-Box is usually mounted onto the right hand side window and at a distance that is comfortably
reached by hand.
•
Allow clearance for the front window to be opened or slid up into the roof.
•
Use window cleaner to clean both the glass and the suction cup mounts so as to achieve a good
contact.
•
Screw in cables and make tidy with conduit, cable ties etc.
•
DO NOT PLUG IN POWER
until
AFTER
2D Sensor is Installed.
•
Now you are ready to install the 2D Sensor.
LED indicator and C-Box installation
Examples of LED and C-Box locations below:
Содержание IDIG TOUCH XD610
Страница 1: ...Installation Walkthrough Guide ...
Страница 3: ...Pre Installation Checklists ...
Страница 5: ...Stage 1 Hardware Installation ...
Страница 11: ...Stage 2 Auto Calibration ...