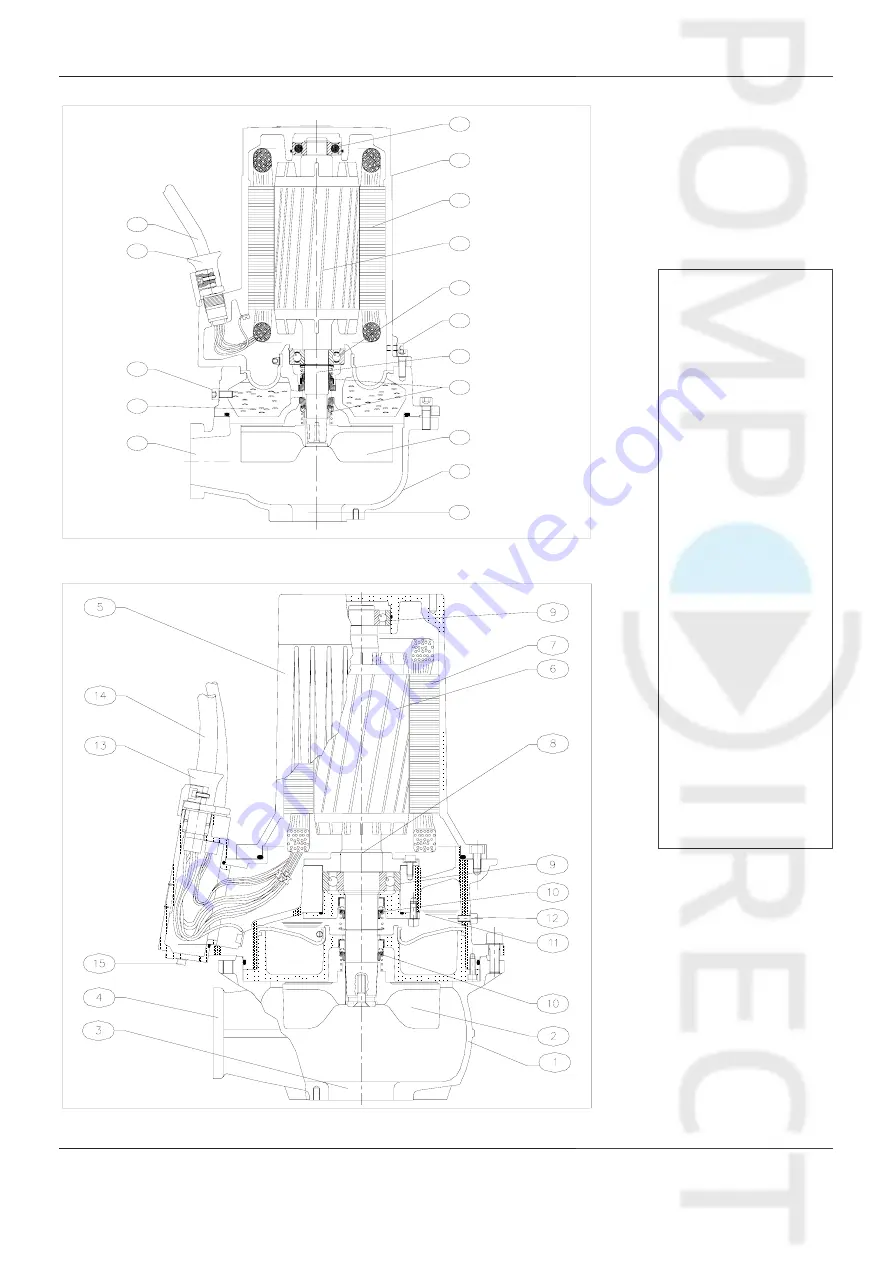
Operation &
Maintenance Manual
Pump
RW
782-001-GB
HSC
08-W36
Edition 4
7/32
1 Pumpcasing
2 Impeller
3 Suction
4 Delivery
5 Motorcasing
6 Rotor
7 Stator
8 Shaft
9 Bearings
10 Mechanical seal
(2x)
11 Oil reservoir
12 Oil plug
13 Cable entry
14 Cable
15 Inspection plug
5
7
15
8
10
2
1
4
3
13
12
11
9
6
9
14
OIL
Fig. 4.2
RW40
RW60
Fig. 4.3
www.robotpompen-onderdelen.nl
T +31(0)294-457712