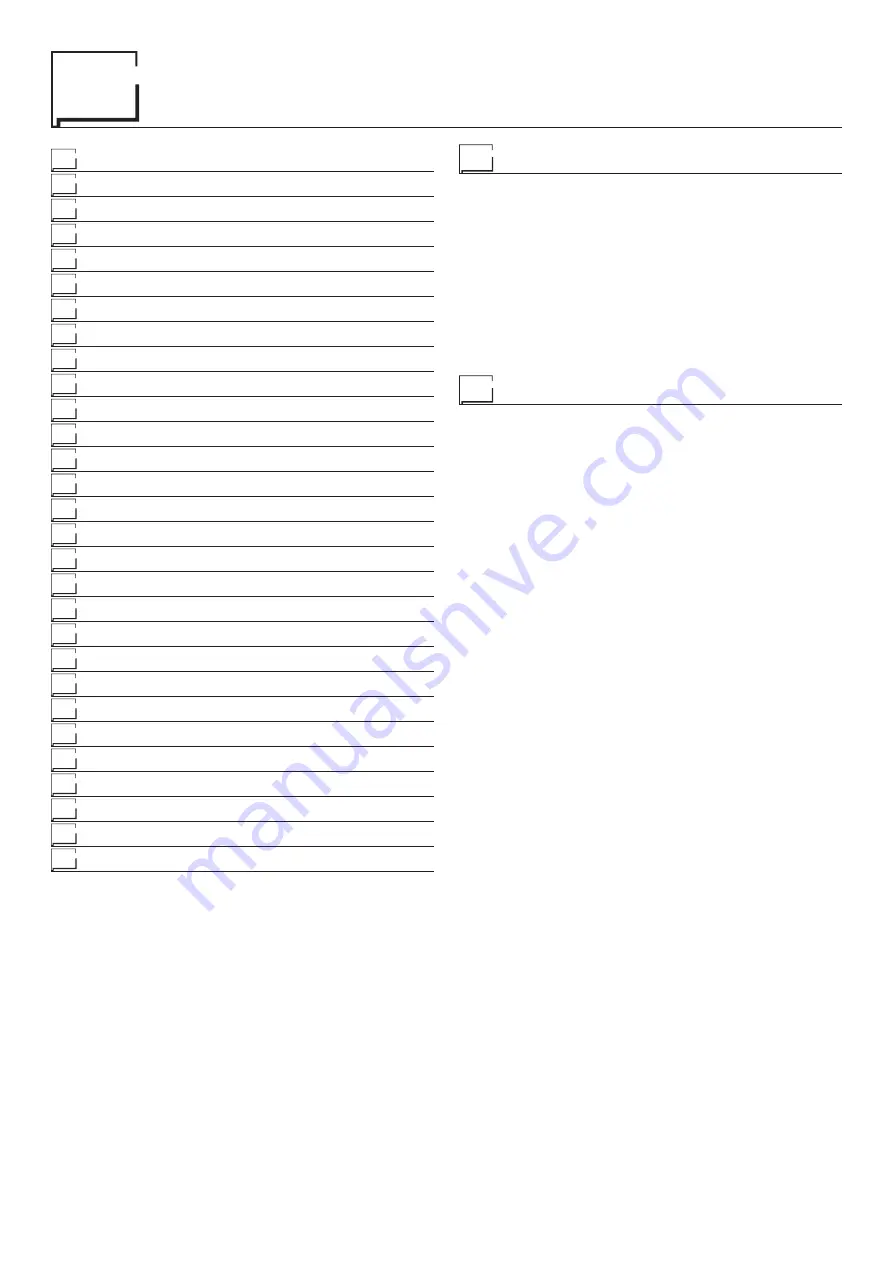
2
ENGLISH
EN
Introduction
2
Description
2
SK and SKM torches
3
CS - Original spare parts
3
Usage limits (IEC 60974-1)
3
SHARK 75 technical characteristics
4
SHARK 105 technical characteristics
4
Opening the packaging
5
Plasma cutting
5
Installation
5
Connection to the electrical supply
5
Usage norms
6
Connection of plasma torch and ground wire
7
Connection of compressed air
8
Sequence of operations to perform before cutting
8
Configuring the torch for manual cutting
9
Using the torch for manual cutting
10
Configuring the torch for automatic cutting
13
Using the torch for automatic cutting
17
Automatic CNC cutting tables
19
Maintenance
40
Possible problems and remedies
40
Troubleshooting table
41
Common cutting defects
43
Meaning of graphic symbols on machine
44
Key to the electrical diagram
44
Colour key
44
Wiring diagram SHARK 75
45
Wiring diagram SHARK 105
46
Introduction
Thank you for buying our product.
In order to get the best performance out of the machine and
ensure the maximum lifespan of its parts, the use and mainte-
nance instructions contained in this manual must be read and
strictly complied with, as well as
the safety instructions con-
tained in the relevant folder
. If repairs to the machine are
required, we recommend that our clients contact our service
centre workshops, as they have the necessary equipment and
personnel that are specifically trained and constantly updated.
All our machines and equipment are constantly developed and
so changes may be made in terms of their construction and
features.
Description
After significant investments and resources put into research,
these inverter generators, with new technology torches, make
a significant increase in the quality and speed of the cutting pro-
cess possible. This quality takes the form of precise outlines,
edges without burrs, a limited thermally altered zone, and a
sufficiently square edge.
Our
SHARK
systems are an efficient solution when it comes
to cutting any metal and perforated plates. The inverter’s elec-
tronic control, precision, and flexibility make it possible to de-
termine the most correct parameters, in order to ensure high
quality cutting specifically related to the thickness and type of
material to be cut.
Thanks to the new
SK
torches for manual cutting, and
SKM
for automated CNC cutting, the
SHARK
models make it pos-
sible to make cuts without using high frequencies to ignite the
arc, thereby reducing disturbance of the external environment.
Our powerful
SHARK
generators, with a professional, high flow
rate, air system, guarantee perfect cuts.
The salient technical characteristics that are common to all ma-
chines, are as follows:
• Three-phase power supply.
• Stability of cutting parameters, despite power supply fluc-
tuations.
• Automatically resetting protective devices against undervolt-
ages and overvoltages on the electricity mains.
• Trip switches to protect against overloading.
• Reduced energy consumption.
• Electronic control for excellent cut quality.
• Professional, high flow rate air system.
• Torch with pilot arc.
• Centralised torch connection.
• Electrical protective device on the torch to guarantee the op-
erator’s safety.
• Capacity to cut meshes and perforated plates.
• Capacity for contact cutting with currents less than 50A, with-
out using slides or other spacers.
• Air filter and regulator unit with automatic expulsion of impu-
rities, complete with pressure gauge for measuring the air
pressure at the machine intake.
• Innovative, functional design, with an inclined front panel,
making it clearly visible from any angle, for easy reading and
setting of parameters.
• Metal loadbearing structure, with front panels on impact-re-
sistant fibre, and commands protected against accidental
impacts.
• Strong handle built into the frame.
Содержание SHARK 105
Страница 45: ...45 Wiring diagram SHARK 75...
Страница 46: ...46 Wiring diagram SHARK 105...