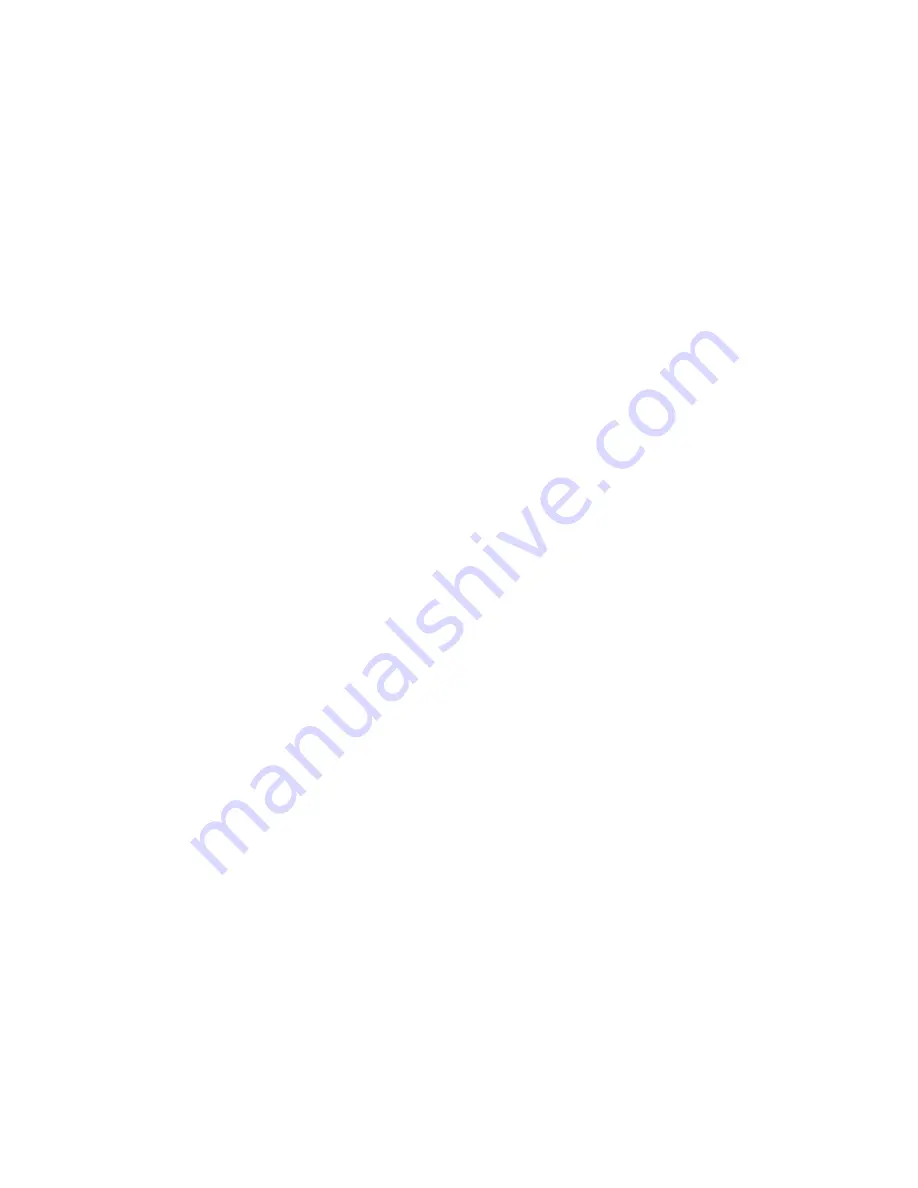
L20-406 Rev 7 (01/17) Page 23
5.4
ANNUAL/PERIODIC PREVENTATIVE MAINTENANCE AND INSPECTION
This section should ONLY be performed by a qualified service technician as part of a regular kitchen maintenance
program. This inspection should take place a minimum of once a year by an Authorized Service Technician recom
-
mended by Pitco. It may be necessary perform this inspection more than once a year.
5.4.1 SAFETY EVALUATION
√
Check power cord and plug.
√
Check all exposed wiring connections, switches, and indicator lights.
√
Check legs, casters, wheels, plate welds and ensure all nuts and bolts are secured.
5.4.2 MECHANICAL INSPECTION
√
Check fry tank for shortening leaks and excessive oil build up
√
Check for oil migration (Clean as required)
√
Check hood drain cup, ensure that it is not dripping onto the appliance. Empty as necessary.
√
Check hood for clean surface, oil/water condense can drip onto appliance.
√
Check drain/filtration system (if equipped) for leaks
√
Check for missing fryer parts.
√
Check for missing fasteners
5.4.3 TEMPERATURE CONTROL SYSTEM
√
Check electrical connections and harnesses
√
Check temperature probes and limits for carbon build up and plating. Clean as required
√
Check proper mounting of probes and sensors and verify all fasteners are secure.
√
Check DVI Drain Valve Interlock drops out controller.
√
Check Controller/thermostat features to ensure they are functioning.
√
Check Temperature Calibration
5.4.4 FILTER SYSTEM (IF EQUIPPED)
√
Check electrical connections and harnesses.
√
Check IEC power cords are fully engaged and secure.
√
Check for any air or shortening leaks and for excessive oil build-up.
√
Check O-Ring on filter pickup tube and replace as needed.
√
Check filter strainer on pickup tube.
√
Check operation of drain valve and DVI drain valve interlock.
√
Check operation of return oil valve and its pump switch.
√
Check all hardware in filter pan.
√
Check filter operation by filtering the fryers.
√
Check pump motor amp draw compare to nameplate amperage.
√
Check pump and motor; clean any excess oil from pump assembly.
√
Check all filter hoses for leaks and integrity.
5.4.5 HEATING ELEMENT
√
Check if the element is mechanically strong and in good condition. Look for scale build up and inspect for
signs of dry firing.
√
Verify element wires are in good working condition. Look for damage to wires or frayed insulation. Check
that the insulation is dry.
√
Verify that bulkhead connections/nut is tight and leak free. Look for grease build up and oily surfaces.
√
Verify amp-draw is within range as compared to the information on the data plate.
5.4.6 CONTROL BOX & ELECTRICAL COMPONENTS
√
Verify that heating contactors are in good condition. Check for worn or pitted contacts. Verify that wires
are tight and in good condition.
√
Verify that all components (transformer, terminal block, relays, drain switches, etc…) are in good condition.
Verify that wires are tight and in good condition.
√
Verify enclosures are free of leaks. Check for water stains and wet surfaces.
√
Verify that the covers and panels are intact and provide a safe condition. Check for loose parts.
√
Verify power cord is in good condition. Check for frayed or exposed wires. Verify that the insulation is in
good condition and the attachment to the appliance is tight.
PREVENTATIVE MAINTENANCE