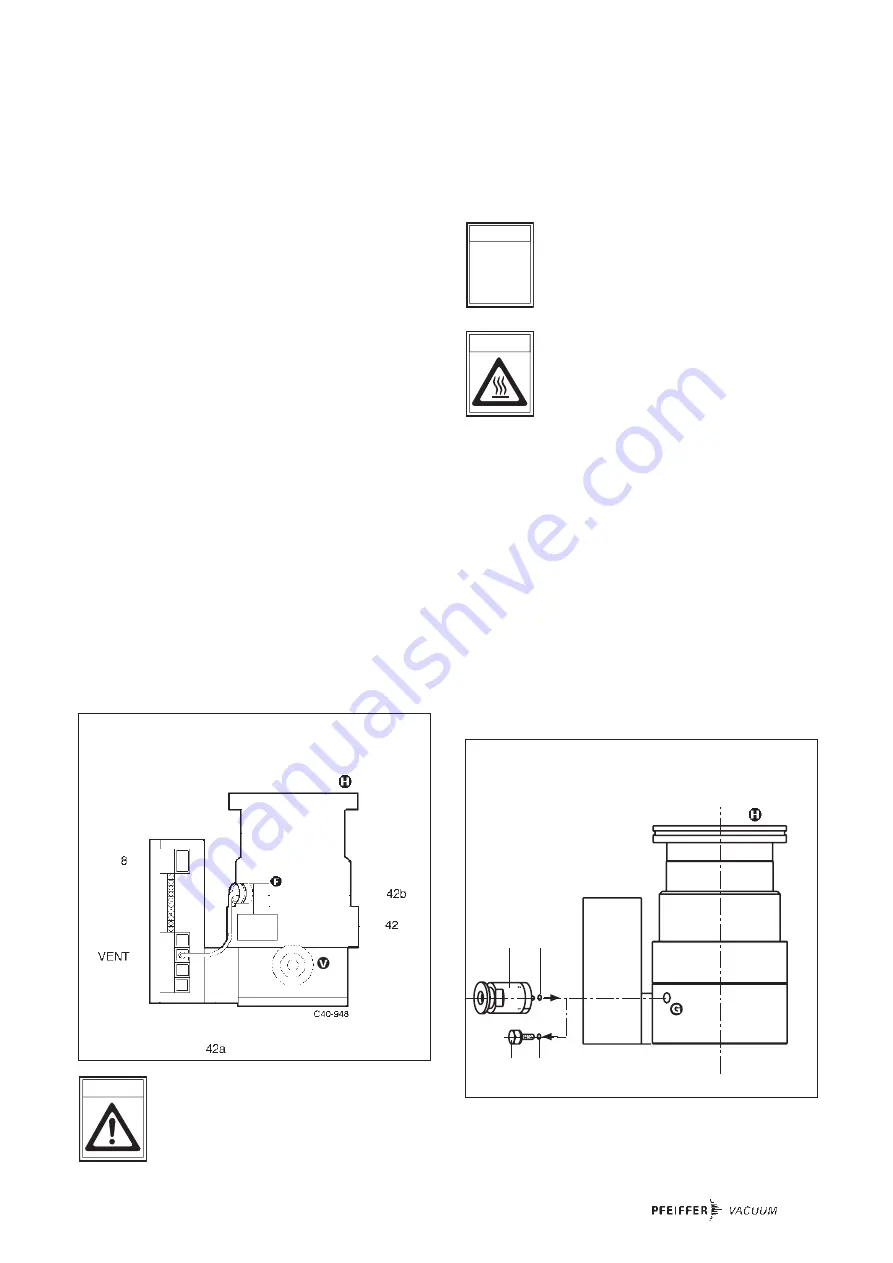
7
Connecting the venting valve
8
Electronic Drive Unit TC 600
42
Venting valve TVF 005
42a Control lead venting valve/TC 600
42b Plug
The maximum pressure at the venting valve is
1.5 bar absolute.
Please refer to Operating Instructions PM 800 507 BN for
details on Venting Valve TVF 005.
CAUTION
3.4. Connecting The Cooling Unit
Turbopumps TMH 071 P/TMU 071 P can optionally be
provided with enhanced convection cooling, air cooling or
water cooling.
The turbopumps must be operated with air or water cooling
where the fore-vacuum pressure is increased (> 0.1 mbar)
and/or operations with gas loads.
Use and installation:
– For water cooling please refer to Operating Instructions
PM 800 546 BN.
– For air cooling please refer to Operating Instructions
PM 800 543 BN.
– Permissible installation positions for the cooling unit
where convection cooling is involved please see
Section 9.1. ”Dimensions Diagram”.
3.5. Connecting The Venting Valve
The Venting Valve TVF 005 provides automatic venting in the
event of a power failure and switching off.
Fitting the venting valve
➡
Unscrew the venting screw from the venting connection of
the turbopump.
➡
Screw in venting valve 42 with seal (USIT ring) on hexago-
nal SW 14.
Electrical connection
➡
Plug control lead 42a into the connection ”VENT” of the
TC 600 (8) on the turbopump.
The venting mode of the venting valve is selected via the DCU
or Serial Interface RS 485.
3.6. Connecting The Casing Heating Unit
The attainment of final pressures is accelerated when turbo-
pumps and vacuum chambers are baked out.
The heating duration is dependent on the degree of dirt and
on the required final pressure level. The heating duration
should be at least 4 hours.
Where casing heating is involved the
turbopump must be water cooled.
High temperatures are generated when the tur-
bopump is baked out. There is a danger of
burns resulting from touching hot parts, even
after the casing heating has been switched off.
Ideally, the heating sleeve.and the pump casing
should be insulated during installation. Do not
touch the heating sleeve and the pump casing
during the baking out process.
Please refer to Operating Instructions PM 800 542 BN for
details on the casing heating unit and its installation.
3.7. Connecting The Sealing Gas Valve
To protect the pump, particularly where corrosive or dust pro-
ducing processes are involved, it is necessary to use sealing
gas.
Connection is made via the sealing gas valve (please see
“Accessories”).
WARNING
☞
PLEASE NOTE
Please refer to Operating Instructions PM 800 229 BN for
details on installing the sealing gas valve and adjusting the
sealing gas flow.
66 66a
9 15
Connecting the sealing gas valve
9
Locking screw sealing gas connection
15
Dichtung
66
Sperrgasventil
66a Dichtung