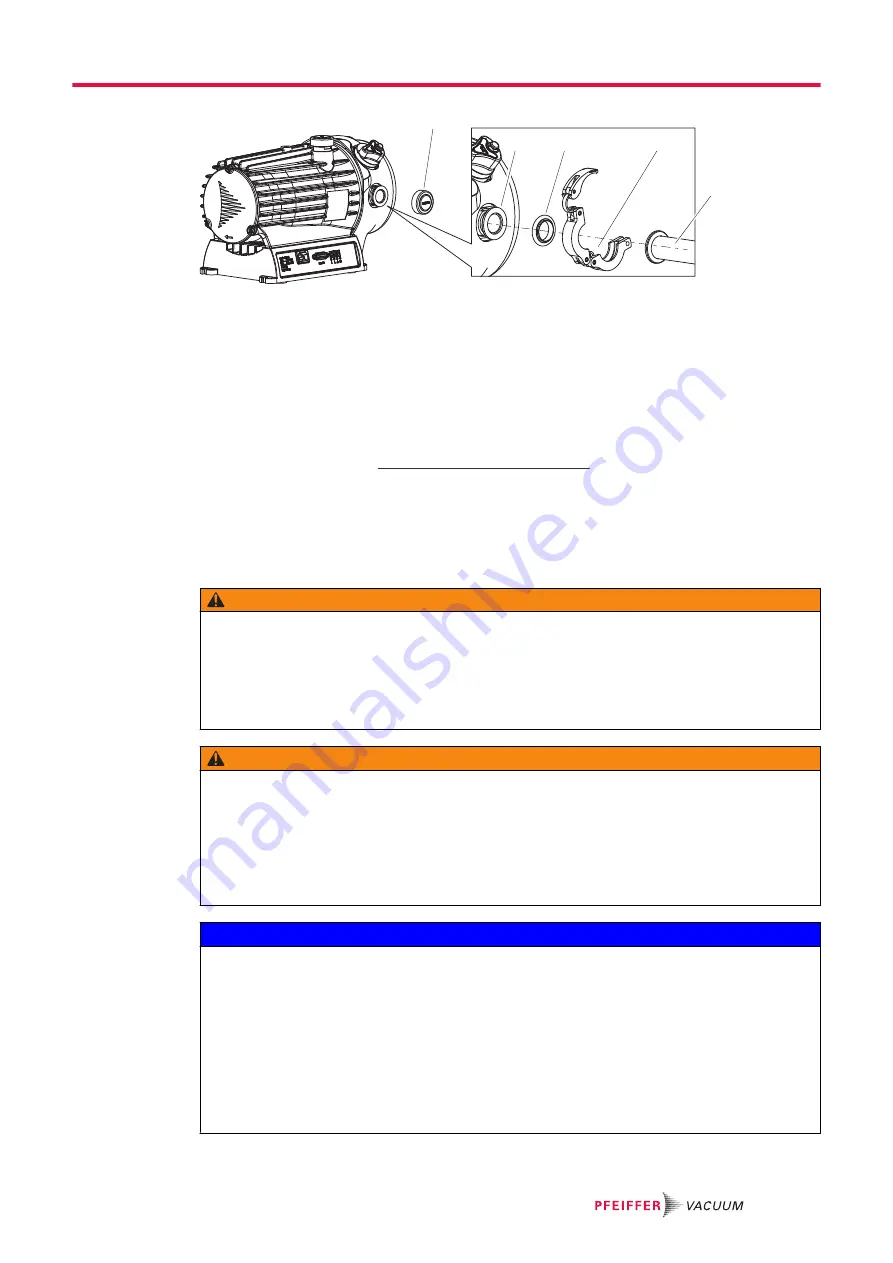
1
2
3
4
5
Fig. 7:
Example of exhaust connection
1 Protective cover
4
Circlip
2 Exhaust connection of the scroll pump
5
Vacuum components DN 25 ISO-KF
3 Centering ring
Procedure
1. Remove the protective cover from the exhaust connection.
2. Choose a minimum exhaust line cross section equal to the connection nominal diameter.
3. Install a vacuum connection with small flange components, e.g. fasteners and pipe components
DN 25 ISO-KF from the
Pfeiffer Vacuum Components Shop
4. Route the piping downwards from the vacuum pump, to prevent condensate return.
5. Support or suspend the piping to the vacuum pump so that no piping system forces act on the
vacuum pump.
5.4 Connecting gas ballast external supply
WARNING
Explosion hazard if particles enter at the gas ballast valve
When connecting the gas ballast line, there is a risk of foreign particles entering, which may cause an
exothermic reaction if the material pairing in the suction chamber is unfavorable.
► When connecting the external gas ballast supply, ensure that the gas ballast valve is closed.
► Clean the inlet area of the gas ballast valve by activating the gas supply with slight overpressure
when the valve is closed.
WARNING
Risk of injury from reactive, potentially explosive or otherwise hazardous gas/air mixtures
Uncontrolled gas inlet of air or gases containing oxygen may lead to the formation of potentially ex-
plosive gas/air mixtures in the vacuum system. Ignition can cause very serious injuries.
► Use inert gases only for the supply of ballast gas in order to prevent the formation of a potentially
explosive atmosphere.
► Ensure a closed inert gas system in order to avoid zone entrainment as a result of process gas
entering into the inert gas line.
NOTICE
Risk of damage from condensation in vacuum pump
Exceeding the saturation vapor pressure of process media during the compression phase leads to
condensation in the suction chamber. This results in an increase of the achievable ultimate pressure
and to a general deterioration of the performance data of the vacuum pump as a whole. Corrosion
and contamination impair service life.
► Use the gas ballast.
► Supply dry room air or inert gas in order to increase the vapor capacity of the process medium.
► Pump condensable vapors only when the vacuum pump is warm and the gas ballast valve open.
► Operate the vacuum pump with gas ballast a further approx. 30 minutes after finishing the proc-
ess in order to dissipate any residual moisture.
Installation
29/84
Содержание HISCROLL 12
Страница 52: ...Alternative Switch off via remote interface Remove the bridge between pins 7 ad 5 Operation 52 84...
Страница 83: ...83 84...
Страница 84: ...PU0097 ed B Date 2209 P N PU0097BEN...