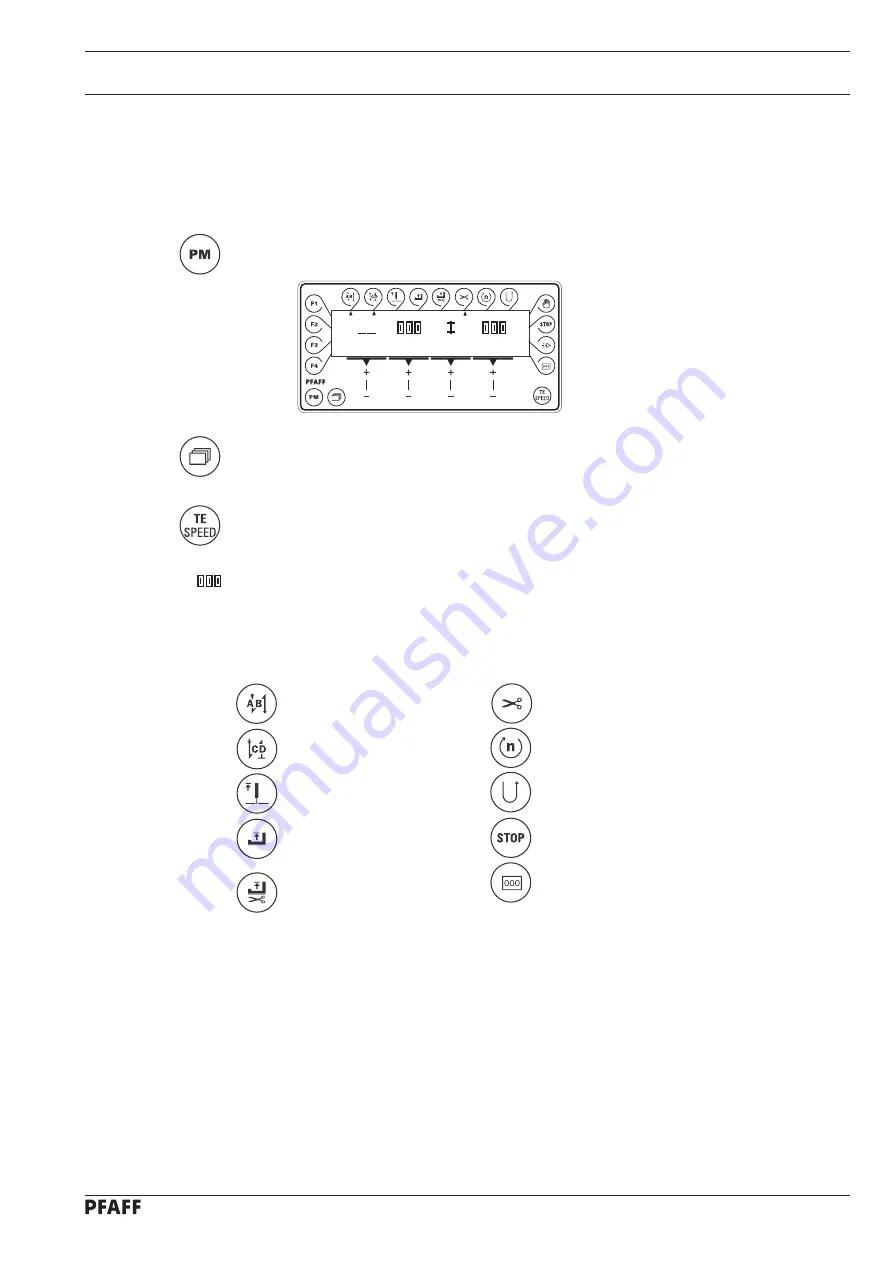
Sewing
10 - 2
10
.02
Programmed sewing (shoulder seams)
In the programmed sewing mode previously defined seam segments for the shoulder
seams are sewn automatically.
●
Switch on the machine.
●
If necessary, call up programmed sewing.
●
If necessary, change the tack value, also see
Chapter 9.09 Entering the start and end
backtacks.
●
If necessary, change the maximum speed, see
Chapter 9.08 Entering the maximum
speed.
●
If necessary, change the number of stitches for the fullness with the corresponding
+/- keys
, see
Chapter 9.07 Pre-selecting the stitch length and fullness
.
Further functions, also see
Chapter 7.07.02 Function keys:
Start backtacks on/off
Thread trimming on/off
End backtacks on/off
Fixed speed on/off
Needle position raised on/off
Reverse sewing direction on/off
Presser foot raised on/off
Programmed stop on/off
Presser foot raised after
Stitch count on/off
thread trimming on/off
●
Sewing is carried out with the pedal functions, see
Chapter 7.02 Pedal.
10
1
3
Содержание 3827-4/33
Страница 96: ...14 3 Circuit diagrams Version 10 01 2006 91 191 497 95 Page 1...
Страница 97: ...14 4 91 191 497 95 Page 2 Version 10 01 2006 Circuit diagrams...
Страница 98: ...14 5 Circuit diagrams Version 10 01 2006 91 191 497 95 Page 3...
Страница 99: ...Notes...