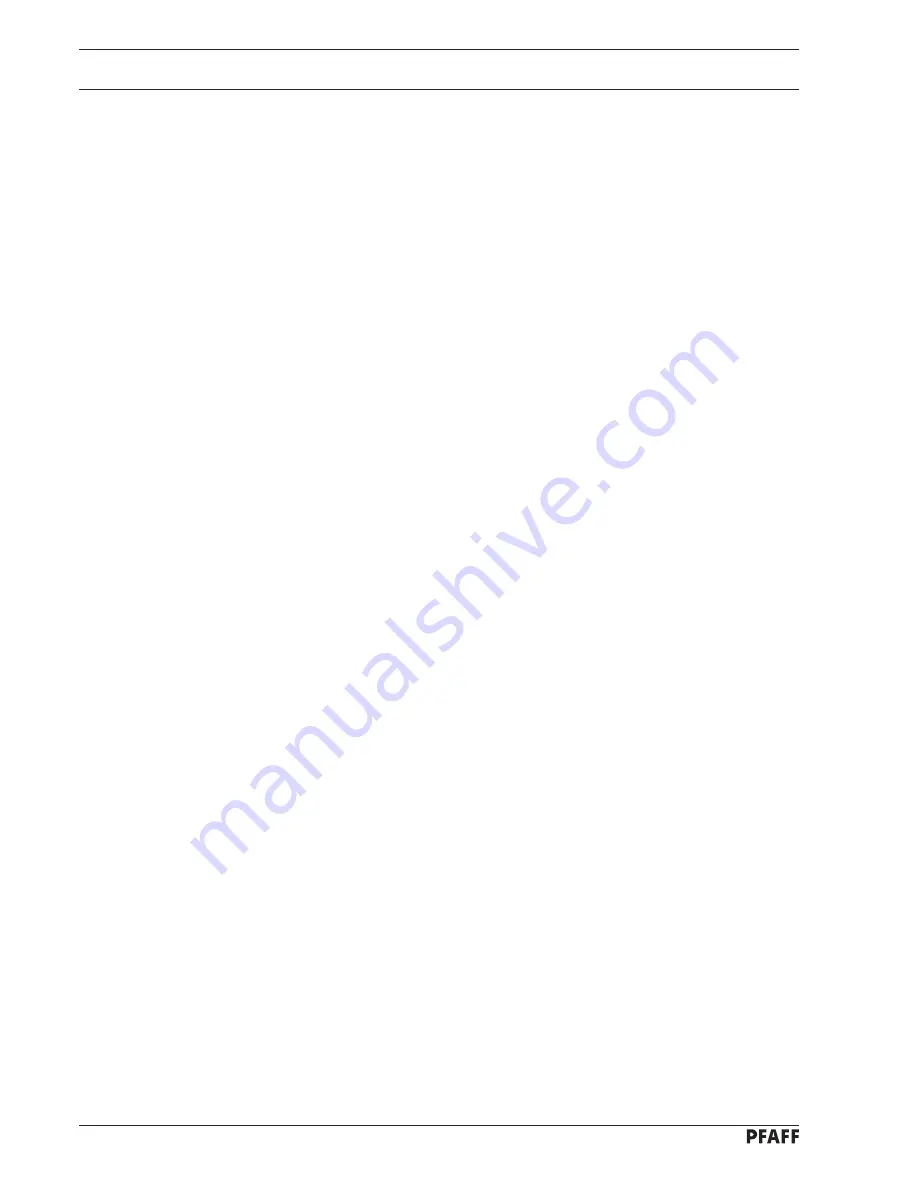
Safety
1 - 1
1
Safety
1
.01
Directives
This machine is constructed in accordance with the European regulations contained in the
conformity and manufacturer’s declarations.
In addition to this Instruction Manual, also observe all generally accepted, statutory and
other regulations and legal requirements - also those of the country in which the machine
will be operated - and all valid environmental protection regulations!
The regionally valid regulations of the social insurance society for occupational accidents or
other supervisory organizations are to be strictly adhered to!
1
.02
General notes on safety
●
This machine may only be operated by adequately trained operators and only after having
completely read and understood the Instruction Manual!
●
All Notes on Safety and Instruction Manuals of the motor manufacturer are to be read
before operating the machine!
●
The danger and safety instructions on the machine itself are to be followed!
●
This machine may only be used for the purpose for which it is intended and may not be
operated without its safety devices. All safety regulations relevant to its operation are to
be adhered to.
●
When exchanging sewing tools (e.g. needle, presser foot and bobbin), when threading
the machine, when leaving the machine unattended and during maintenance work, the
machine is to be separated from the power supply by switching off the On/Off switch or
by removing the plug from the mains!
●
Everyday maintenance work is only to be carried out by appropriately trained personnel!
●
Repairs and special maintenance work may only be carried out by qualified service staff
or appropriately trained personnel!
●
Work on electrical equipment may only be carried out by appropriately trained personnel!
●
Work is not permitted on parts and equipment which are connected to the power supply!
Exceptions to this are only to be found in the regulations EN 50110.
●
Modifications and alterations to the machine may only be carried out under observance
of all the relevant safety regulations!
Содержание 3574-2/02
Страница 1: ...296 12 17 977 Betriebsanleitung engl 11 96 3574 2 02 Instruction Manual...
Страница 89: ...Notes...