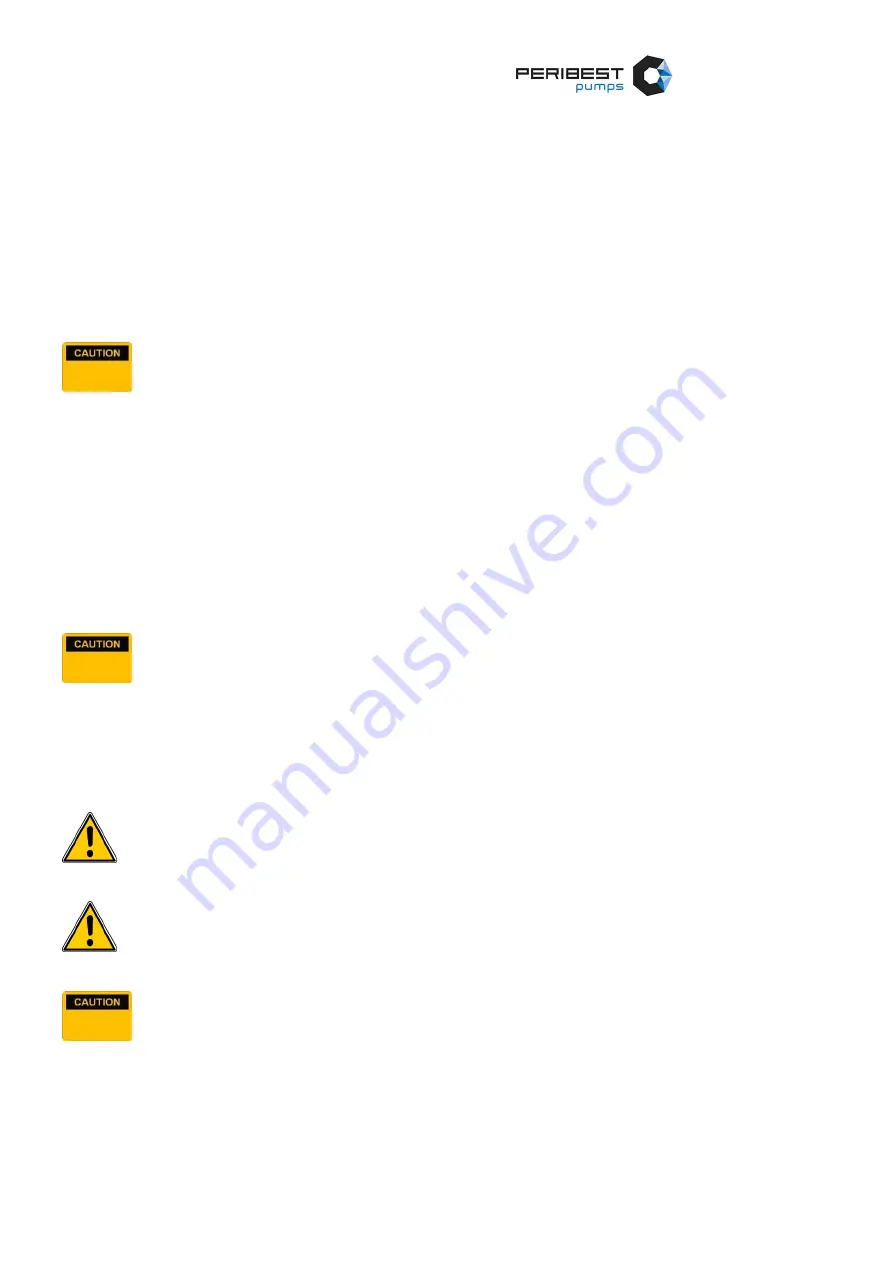
MANUAL PERIBEST I12
–
I17
–
I21
8 | 29
· Do not carry out any maintenance operations or dismantle the
pump without first making sure that the pipes are not under
pressure and are empty or isolated.
· As the peristaltic pump is volumetric and its functioning is positive
displacement, it is necessary to prevent a possible overload of
pressure, due to for example, the accidental closure of a valve. For
this reason it is advisable to fit a safety device such as: a safety valve,
pressure limiter, etc.
Operational lifetime of the pump hoses
The operational lifetime of the pump hoses cannot be precisely
specified. For this reason, the possibility of fracture and
consequential leakage of liquids must be accounted for. If the hose
leakage sensor (optional) is fitted, then the pump can be stopped
and / or an electrical valve can be actuated.
In addition, as the hose has an indeterminate life and due to the
possibility of its breakage or deterioration, the user is responsible
for the prevention of a possible (although most unlikely)
incorporation of particles form the hose into the product being
pumped. This can be achieved e.g. by means of filtration, a hose
rupture alarm or other means suitable for the respective process
CIP cleaning
In the event of CIP cleaning, it is necessary to obtain information
from the manufacturer about correct installation of the pump as well
as regarding the compatibility of the cleaning agents with the pump
hoses and the hydraulic connections.
Cleaning should be undertaken at the recommended maximum
temperature.
Direction of rotation/flow direction
The pump's direction of rotation in relation to the desired flow
direction must be checked prior to every start.
Disconnect the pump from the mains
You may only carry out work on the pump after it has previously
been switched off and disconnected from the mains.
Environmental influences
· The device is not suitable for outdoor operation
· Take suitable measures to protect the device from environmental
influences such as UV rays, moisture, frost, etc.
Содержание I12
Страница 1: ......
Страница 25: ...MANUAL PERIBEST I12 I17 I21 25 29 Spare parts ...