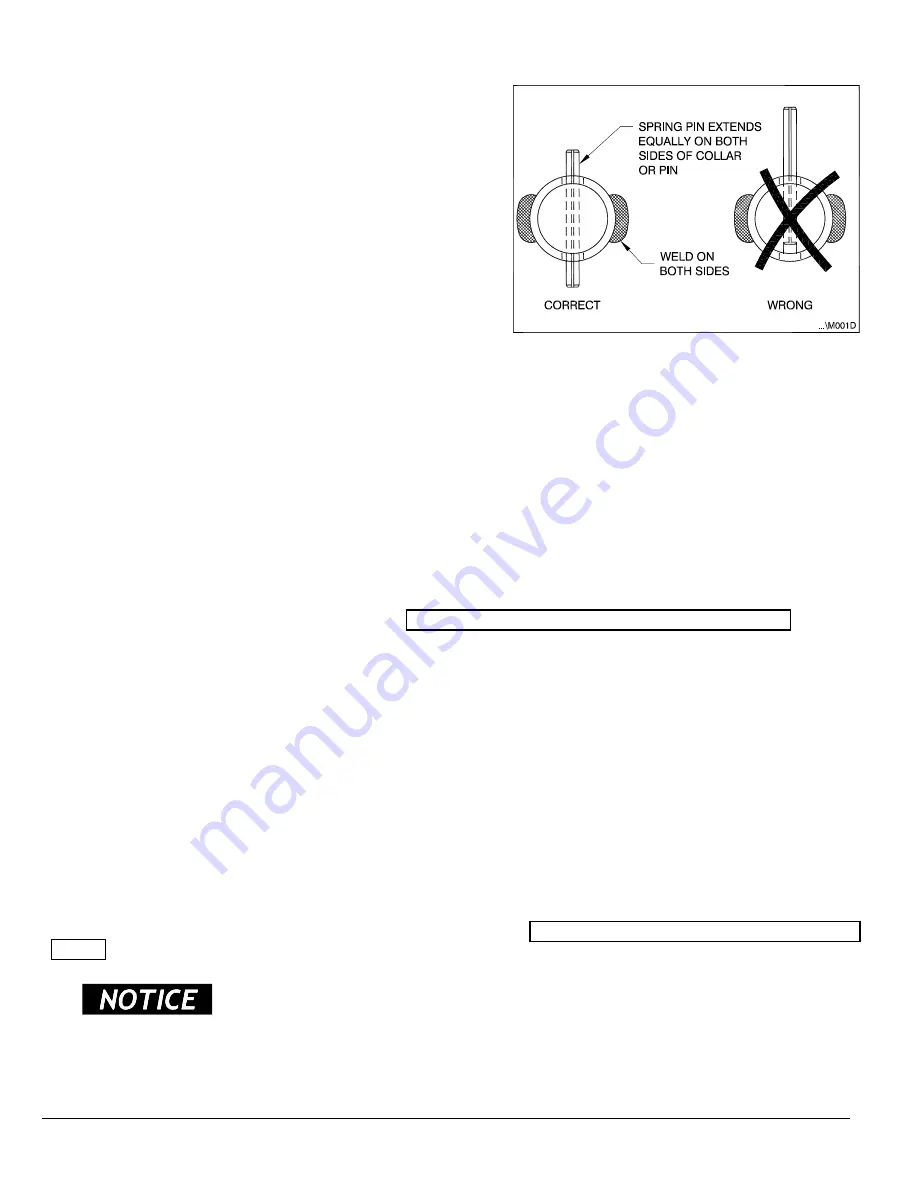
17
PENTALIFT EQUIPMENT CORPORATION
M086R06
December 8, 2017 10:37 AM
LDL Dock Lift Owners Manual
8. Check the hinged bridge to ensure that its stops are not
damaged, allowing it to droop more than 45 degrees below
horizontal, check the hinge spools for cracks and or broken
welds.
Check all spring pins, items 2, 29 and 35 in Figure 13, page 19, to
confirm they are not damaged and that they are properly inserted.
Confirm that all welds on the spring pin collars are intact. (See
Figure 11, page 16)
Ensure that any specified interlocks (e.g. overhead doors,
restraints) are fully functional.
Ensure the toe sensor (if equipped) is functional by raising the lift
to full height and lifting the toe sensor bar under each of the toe
sensor limit switches (there are normally 4 switches). Confirm the
unit does not lower with the toe sensor bar raised. Repeat the lifting
on each of the limit switches and confirm the unit will not lower when
the bar is lifted under any of the switches.
NOTE:
The toe sensor option is an electrical safety device with an actuator
suspended beneath the platform which halts downward travel of the dock lift if it contacts with an obstruction. (This feature
is not functional in the event of hydraulic failure.)
Figure 11: Spring Pins
Hydraulic Oil:
Weekly:
Once a week, or after repetitive operation, the lift should be raised to its full height. This will get rid of cylinder oil
seepage build-up and lubricate the upper cylinder barrel.
Monthly:
For ease of maintenance, lifetime lubricated bushings have been used on all rollers, leg pivot points as well
as the upper cylinder pivot. However, units installed outdoors or in wet and dirty environments should be
recommended lubrication
service interval is every 30 days
or at a greater frequency as required in severe
environments.
Dexron III Automatic Transmission Fluid
is recommended.
The oil level should be checked once a month. When the dock lift is fully lowered, the oil level in the reservoir of a
1 or 3 hp power unit should be approximately 2 – 3 inches from the top. A 5 hp or higher power unit should have
the oil in the reservoir filled to the full mark on the sight gauge. The oil should be changed once a year under
normal operating conditions. The standard replacement Hydraulic Fluid is DEXRON III Automatic Transmission
Fluid which has an operating range of -10°C (14°F) to 50°C (122°F). If the hydraulic oil is non-standard, check
the hydraulic reservoir for fluid label which will specify the particular fluid requirements. It is strongly urged that a
maintenance log be maintained with the dates of monthly inspections, the name of the inspector and results of the
inspection.
Seasonal or semiannual maintenance:
Change hydraulic fluid for ambient temperature changes if appropriate. Check the
fluid reservoir to see if there is any evidence of accumulated condensation creating water contamination. The fluid
will appear “milky” and light pink in color. Water accumulation will damage the hydraulic pump.
Dock lifts also require grease at the base of the hydraulic cylinders; See “Figure 12: Lubrication Oil and Grease Points” on
The standard hydraulic oil supplied with the equipment is good from -20º C (-4ºF) minimum
to +54ºC (+129ºF) maximum unless otherwise specified on the equipment order. When
operating the equipment in temperatures lower than -20ºC (-4ºF) or above +54ºC (+129ºF), the pump may create
cavitation, causing permanent damage to the power unit. This will void all warranty. The standard replacement
Hydraulic Fluid is DEXRON III Automatic Transmission Fluid which has an operating range of -10°C (14°F) to
50°C (122°F). If the hydraulic oil is non-standard, check the hydraulic reservoir for fluid label which will specify the
particular oil requirements.