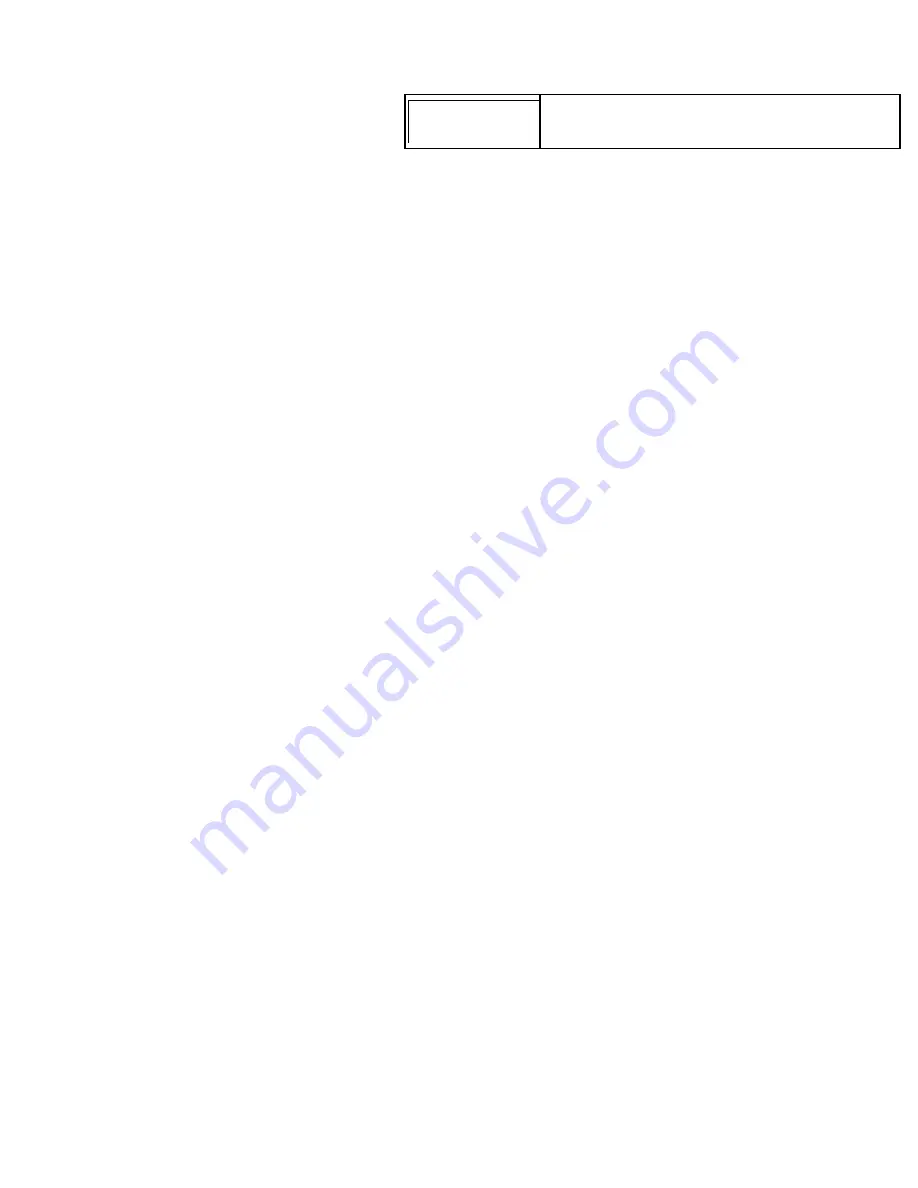
9-1-2009
22
FUEL SYSTEM
The fuel system piping must comply with the pump manufacturers’ specifications which are
included with the burner. In addition all fuel system piping must comply with local codes and
ordinances.
-
The quality of your fuel is of great importance. For most instances Your burner is designed to
burn clean water free #2 fuel. Where outside tanks are subject to temperatures below
0degreesF #1 fuel is recommended.
-
The oil supply line should be constructed of seamless heavy wall copper tubing with flared
fittings. Only oil resistant pipe dope should be used on threaded connections. The use of
Telfon Tape will void manufacturers’ warranty. Lines must be airtight, clean and free of
kinks. All joints and threaded fittings must be checked for leaks. A vacuum gauge should be
employed when testing the installation. It is recommended that older fuel lines be replaced.
-
A two pipe system should only be used when the oil supply is well below the pump. A return
fuel line may be used on installations where the tank level is below the level of the burner.
The return line must be equal in diameter to the suction line. The minimum size for the oil
line is 3/8in. copper tubing.
-
A Tiger Loop is recommended when the oil supply line is located 5 ft. below the burner.
-
Double filtration is recommended to insure maximum pump and nozzle life. The Total Gear
Suction Capacity (TGSC), will determine the filter size. The filter normally found in the tank
should be left in place while adding a high quality paper throwaway cartridge type filter or
line strainer to the fuel suction line. A 5 micron to 10 micron rating is recommended. The
paper filter or strainer should be mounted on the casing of the boiler. Flexible fuel lines with
adequate slack can thus be used allowing for easy removal of the burner or use of the swing
door without having to disconnect the fuel lines.
-
Shut off valves must be installed in the supply line at or near the oil storage tank and at the
burner in compliance with all codes. Inspect the shut off valve spindle packing for tightness
to insure that there are no air leaks. The valve must always be shut off if the burner is shut
down for an extended period of time. The burner should be tagged to indicate that the fuel
supply has been closed off. The electrical circuit to the burner must be cut off by removing
the fuse or circuit breaker to insure that no operation of the burner will occur while the fuel
supply is shut off.
-
Only fuel storage tanks bearing the Underwriters Laboratories label and accessories approved
as prescribed by local code may be used.
-
Never burn paper or garbage in the unit and check to insure that all rags, debris, stored
flammable liquids, or products producing flammable vapors are removed from the area of the
boiler.
GASOLINE, CRANKCASE OIL,
OR WASTE OIL MUST NEVER
BE USED
!
DANGER
Never Burn Gasoline, Waste Oil, or Crankcase Oil in this appliance.
Содержание DK2-3
Страница 5: ...9 1 2009 4 JACKET ASSEMBLY AND CONTROL INSTALLATION ...
Страница 8: ...9 1 2009 7 ...
Страница 9: ...9 1 2009 8 ...
Страница 12: ...9 1 2009 11 ...
Страница 27: ...9 1 2009 26 PARTS LIST AND BOILER DIAGRAM ...
Страница 29: ...9 1 2009 28 ...